下载PDF
Optimizing Dragline Performance and Productivity at VR Steel with Altair EDEM™
技术
- 分析与建模 - 虚拟和增强现实(AR/VR)软件
- 可穿戴设备 - 虚拟现实(VR)眼镜/耳机/控制器
适用行业
- 金属
- 矿业
适用功能
- 产品研发
- 质量保证
用例
- 虚拟原型与产品测试
- 虚拟现实
服务
- 测试与认证
挑战
VR Steel 是一家设计、建造和维修装配式采矿设备附件的公司,面临着针对全球各种介质和采矿条件优化拉铲铲斗性能和生产率的挑战。他们需要开发一种新的、优化的铲斗设计,以平衡效率、容量、耐用性和预计的运营和维护成本。该公司希望简化设计流程,为客户提供设计解决方案,保证轻松填充和完全清空、以最大容量运行、增强磨损保护、降低运营成本并提高整体效率。
关于客户
VR Steel (Pty) Ltd 是一家设计、建造和维修装配式采矿设备附件的公司。他们的客户包括采矿业的主要参与者,例如 Anglo Coal、Arch Coal、BHP Billiton、BMA Coal、Coal India、CRM 和 Xstrata。 VR Steel 在美国、南非、澳大利亚、巴西和印度拥有拉铲铲斗客户。该公司致力于提供创新的解决方案,提高采矿业的生产力和效率。
解决方案
为了应对这一挑战,VR Steel 利用 EDEM 结合多体动力学仿真软件来模拟散装土壤动力学以及铲斗和提升装置的动力学。这种创新的集成颗粒机动力学解决方案成功模拟了瞬态颗粒结构相互作用,模拟了拉铲铲斗的完整挖掘周期。该虚拟性能测试预测了原型铲斗的模式和填充率、铲斗和齿轮的瞬态负载以及磨损模式和速率。 EDEM 虚拟原型的使用使 VR Steel 能够现场测试新的设计选项、为特定用户创建定制设计、构建更少的物理原型、缩短设计周期并提高客户的生产力。
运营影响
数量效益
相关案例.
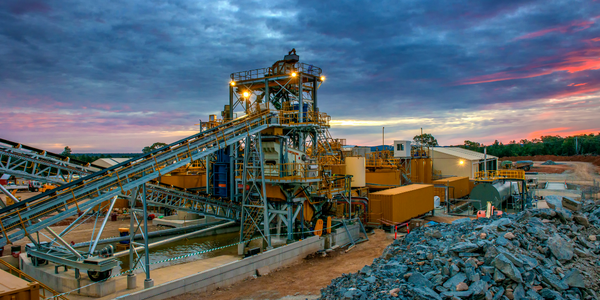
Case Study
Goldcorp: Internet of Things Enables the Mine of the Future
Goldcorp is committed to responsible mining practices and maintaining maximum safety for its workers. At the same time, the firm is constantly exploring ways to improve the efficiency of its operations, extend the life of its assets, and control costs. Goldcorp needed technology that can maximize production efficiency by tracking all mining operations, keep employees safe with remote operations and monitoring of hazardous work areas and control production costs through better asset and site management.
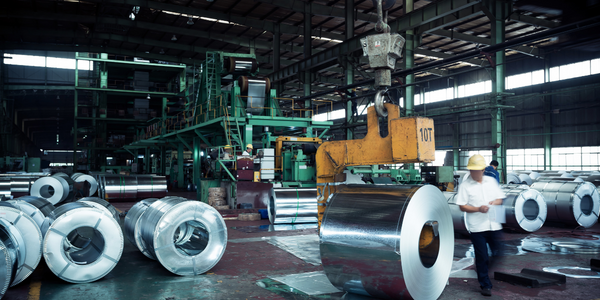
Case Study
KSP Steel Decentralized Control Room
While on-site in Pavlodar, Kazakhstan, the DAQRI team of Business Development and Solutions Architecture personnel worked closely with KSP Steel’s production leadership to understand the steel production process, operational challenges, and worker pain points.
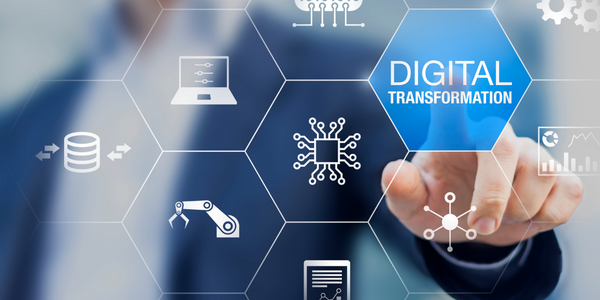
Case Study
Bluescope Steel on Path to Digitally Transform Operations and IT
Increasing competition and fluctuations in the construction market prompted BlueScope Steel to look toward digital transformation of its four businesses, including modern core applications and IT infrastructure. BlueScope needed to modernize its infrastructure and adopt new technologies to improve operations and supply chain efficiency while maintaining and updating an aging application portfolio.
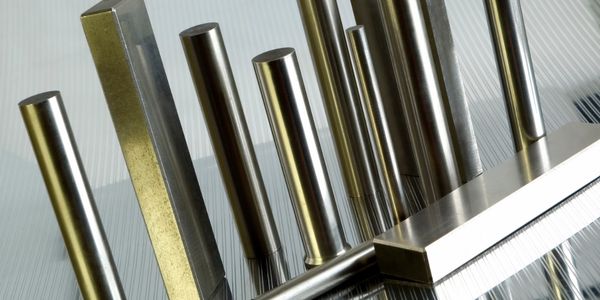
Case Study
RobotStudio Case Study: Benteler Automobiltechnik
Benteler has a small pipe business area for which they produce fuel lines and coolant lines made of aluminum for Porsche and other car manufacturers. One of the problems in production was that when Benteler added new products, production had too much downtime.
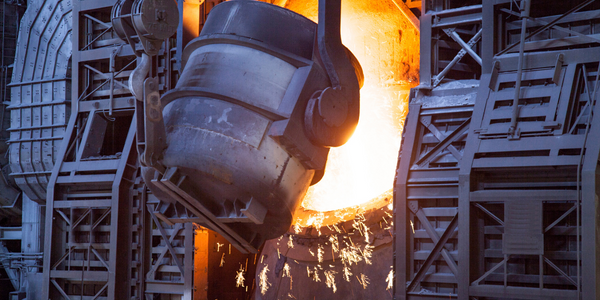
Case Study
Continuous Casting Machines in a Steel Factory
With a very broad range of applications, steel is an important material and has been developed into the most extensive alloy in the engineering world. Since delivering high quality is absolutely crucial for steel plants, ensuring maximum productivity and the best quality production are the keys to competitiveness in the steel industry. Additionally, working conditions in steel factories are not suitable for workers to stay in for long periods of time, so manufactures usually adopt various machines to complete the steel production processes. However, the precision of these machines is often overestimated and the lack of flexibility also makes supervisors unable to adjust operating procedures. A renowned steel factory in Asia planned to improve its Distributed Control System (DCS) of furnaces as well as addressing the problem of insufficient accuracy. However, most well-known international equipment suppliers can not provide a satisfactory solution and local maintenance because the project needed new technologies to more accurately control equipment operations. By implementing Advantech’s automated monitoring and control solution, steel factories can not only improve the manufacturing processes but can also allow users to add additional functions to the existing system so as to make sure the operation runs at high efficiency.
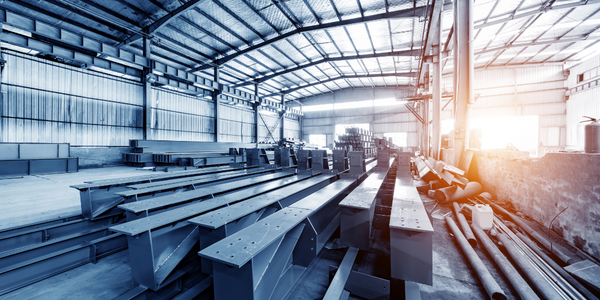
Case Study
Automated Predicitive Analytics For Steel/Metals Industry
Asset to be monitored: Wire Compactor that produces Steel RebarCustomer Faced The Following Challenges:Dependent upon machine uptime.Pressure cylinders within the compactor fail to control compression and speed causing problems in binding the coil.Equipment failure occurs in the final stage of production causing the entire line to stop, can you say bottleneck?Critical asset unequipped with sensors to produce data.