下载PDF
Optimizing Lamp Design with IoT: A Philips Case Study
技术
- 传感器 - 气体传感器
- 传感器 - 电表
适用行业
- 电子产品
- 石油和天然气
适用功能
- 产品研发
用例
- 智能照明
挑战
电子行业的全球领导者皇家飞利浦电子公司在开发陶瓷放电金属卤化物 (CDM) 灯时面临着重大挑战。主要挑战是创建一种在热学和机械性能上均坚固且能够持续指定使用寿命的灯设计。为了实现这一目标,需要精确模拟气体放电、壁温和机械应力。这些因素的复杂性使得开发出能够满足飞利浦所追求的耐用性和寿命高标准的灯变得困难。挑战不仅在于制造出能够承受严格使用的灯,还在于了解可能影响灯性能的各种物理因素之间错综复杂的相互作用。
关于客户
荷兰皇家飞利浦电子公司是世界上最大的电子公司之一,也是欧洲最大的电子公司之一,2003 年销售额达 290 亿欧元。该公司业务涉及三个相互关联的领域:医疗保健、生活方式和技术,在 60 多个国家/地区拥有 166,800 名员工。飞利浦是照明市场的全球领导者,它通过创新领导力和识别新市场机会的系统方法的结合来保持这一地位。本案例研究重点关注飞利浦照明部门及其在高压气体放电灯设计中使用 ANSYS Multiphysics。
解决方案
为了应对这一挑战,飞利浦求助于 ANSYS Multiphysics,这是一款功能强大的工具,使他们能够对 CDM 灯进行全面的热机械分析。气体放电被视为具有导电性的流体,这一过程通过 ANSYS Multiphysics 的耦合场能力得以实现。飞利浦总共采用了四个耦合物理场来模拟灯:流体(气体放电中的温度和速度)、电(气体放电中产生的热量)、热(灯壁和电馈通中的温度)和机械(灯管中的应力)。陶瓷墙)。这种多方面的方法使飞利浦能够在早期阶段全面了解设计性能,从而加快新灯的开发并优化灯的设计。
运营影响
相关案例.
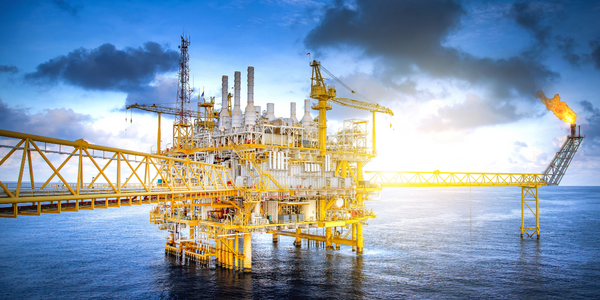
Case Study
Taking Oil and Gas Exploration to the Next Level
DownUnder GeoSolutions (DUG) wanted to increase computing performance by 5 to 10 times to improve seismic processing. The solution must build on current architecture software investments without sacrificing existing software and scale computing without scaling IT infrastructure costs.
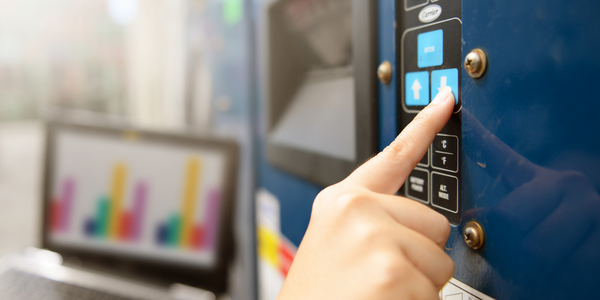
Case Study
Remote Temperature Monitoring of Perishable Goods Saves Money
RMONI was facing temperature monitoring challenges in a cold chain business. A cold chain must be established and maintained to ensure goods have been properly refrigerated during every step of the process, making temperature monitoring a critical business function. Manual registration practice can be very costly, labor intensive and prone to mistakes.
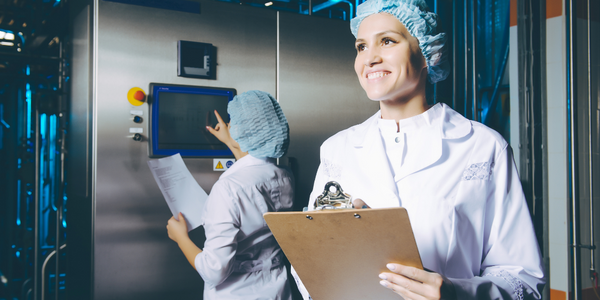
Case Study
Remote Wellhead Monitoring
Each wellhead was equipped with various sensors and meters that needed to be monitored and controlled from a central HMI, often miles away from the assets in the field. Redundant solar and wind generators were installed at each wellhead to support the electrical needs of the pumpstations, temperature meters, cameras, and cellular modules. In addition to asset management and remote control capabilities, data logging for remote surveillance and alarm notifications was a key demand from the customer. Terra Ferma’s solution needed to be power efficient, reliable, and capable of supporting high-bandwidth data-feeds. They needed a multi-link cellular connection to a central server that sustained reliable and redundant monitoring and control of flow meters, temperature sensors, power supply, and event-logging; including video and image files. This open-standard network needed to interface with the existing SCADA and proprietary network management software.
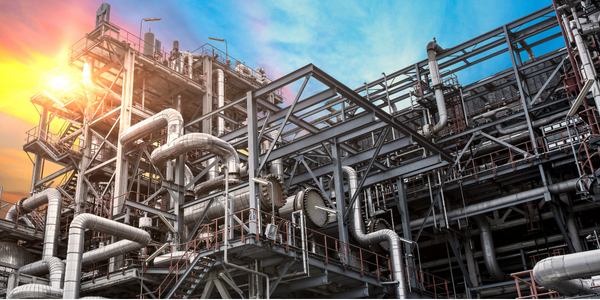
Case Study
Refinery Saves Over $700,000 with Smart Wireless
One of the largest petroleum refineries in the world is equipped to refine various types of crude oil and manufacture various grades of fuel from motor gasoline to Aviation Turbine Fuel. Due to wear and tear, eight hydrogen valves in each refinery were leaking, and each cost $1800 per ton of hydrogen vented. The plant also had leakage on nearly 30 flare control hydrocarbon valves. The refinery wanted a continuous, online monitoring system that could catch leaks early, minimize hydrogen and hydrocarbon production losses, and improve safety for maintenance.