下载PDF
QlikView puts EuroMaint on the fast track to total control
技术
- 分析与建模 - 实时分析
适用行业
- 铁路与地铁
适用功能
- 离散制造
- 物流运输
用例
- 预测性维护
- 自动化制造系统
服务
- 数据科学服务
- 系统集成
挑战
EuroMaint, a leading maintenance solution provider for vehicles in the Swedish rail industry, was facing challenges in reviewing its workflow and synchronizing resources across 20 different applications for equipment support delivery. The company was heavily dependent on IT specialists for custom report development, which was not only costly but also resulted in long turnaround times. They needed an easy-to-use and intuitive analysis solution that could provide an integrated view into operations, bringing together financial, staffing, and operational data.
关于客户
EuroMaint offers complete maintenance solutions for vehicles in the Swedish rail industry. They develop, produce, and deliver technical system services, maintenance, and logistics for the supply of materials for all kinds of rail vehicles and their components. The offering also applies to industrial machinery. EuroMaint’s main product is a comprehensive maintenance solution – the total service concept. The foundation for EuroMaint’s business activities are safety and quality assurance. The daily challenge is to offer services that guarantee high availability of the customers’ vehicles. This is accomplished through customized solutions and complete routines for quality assurance.
解决方案
EuroMaint deployed QlikView to 15 employees across 3 functional areas. With more than 90 QlikView applications, EuroMaint now analyzes invoicing, vehicle history, maintenance operations, and forecasting – all focused on driving more efficient operations to enable its customers with improved vehicle availability and uptime. With QlikView Server, EuroMaint easily handles the massive amounts of data associated with maintenance operations that is aggregated from more than 20 different applications, including its Movex ERP system. The solution provided an integrated view into operations, bringing together financial, staffing, and operational data. It also increased flexibility in developing new applications with the internal team, reducing dependence on specialist IT services.
运营影响
数量效益
相关案例.
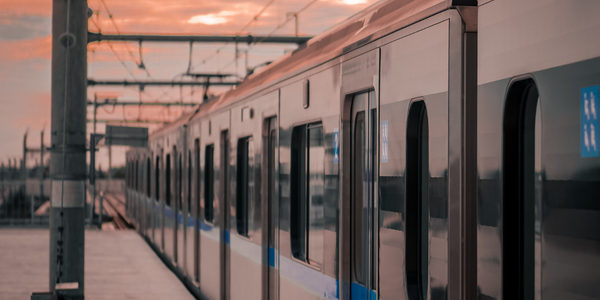
Case Study
Building Smart IoT-Connected Railways
• Difficult environment. Communications equipment on trains must function properly in harsh conditions, such as environment temperatures ranging from -25°C to +85°C, according to the EU standard EN50155.• Railway regulations. All products in a train must adhere to strict standards, relating to working vibration, power consumption, and lifetime.• Lengthy process. Time to market in the railway industry can take years from concept to mass production, so product design requires a solid long term vision.
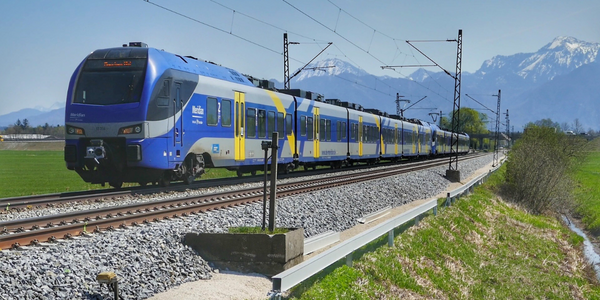
Case Study
Connected Transportation: A Smarter Brain for Your Train with Intel
A modern locomotive, for example, has as many as 200 sensors generating more than a billion data points per second. Vibration sensors surround critical components, video cameras scan the track and cab, while other sensors monitor RPM, power, temperature, the fuel mix, exhaust characteristics, and more.Most of today’s locomotives lack sufficient on-board processing power to make full use of all this data. To make matters worse, the data from different subsystems, such as the brakes, fuel system, and engine, remain separate, stored in isolated “boxes” that prevent unified analysis. The data is available, but the technology needed to process it in the most effective manner is not. As new sensors are added to the machine, the problem escalates.
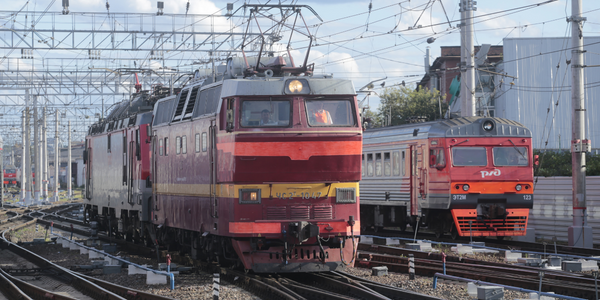
Case Study
Using LonWorks to Keep Acela Trains Zip Along
Canadian transportation company, Bombardier was tasked with building a bullet train system on rails that were designed for lower speed trains. In addition, they had to ensure safe and optimal operation at high speeds, maximize train uptime and enhance communication with passengers.
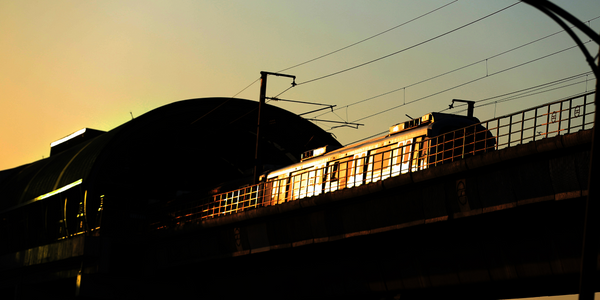
Case Study
Delhi NCR Metro: A Mobile App Revolutionizing Public Transportation
The Delhi NCR Metro, a major public transportation system in India, was facing a challenge in providing accurate and comprehensive information to its daily commuters and tourists. The lack of a centralized platform for information about metro station details, train schedules, fare details, parking, elevators, and tourist locations was causing inconvenience to the users. The challenge was to develop a mobile app that could provide all this information accurately and conveniently. The app needed to be equipped with GPS services to help users find the nearest metro and renowned locations. An interactive map was also required to assist travelers who were familiar with the metro lines. The goal was to provide maximum information with minimum input.
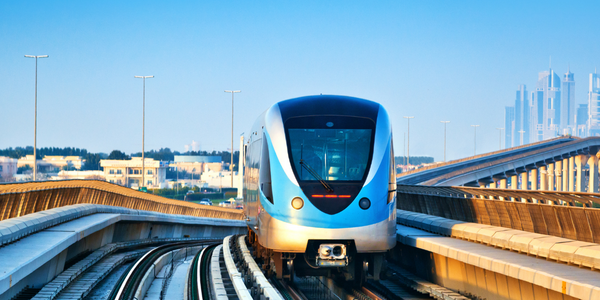
Case Study
Automated Railcar Inspections Increase Security and Revenue
Providing industry and government customers with intelligent inspection, automation, safety, and security solutions, Duos Technologies Group, Inc. (“Duos” or the “Company” - Nasdaq: DUOT) continually pushes the boundaries of IT. To keep pace with expanding AI-enabled data capture analytics for its edge railcar inspections, the company chose the latest Dell EMC PowerEdge servers.Duos Technologies’ challenge was finding a way to leverage technology as a force multiplier to meet customer requirements for a better, faster inspection process for trains running at full speed. Duos developed innovative data analytic solutions with AI at the edge to conduct more reliable railcar inspections, which are available 24/7/365 in all climates and conditions.