下载PDF
R+V Versicherung AG standardizes premium collection with Europe’s largest SAP FS-CD solution
技术
- 功能应用 - 企业资源规划系统 (ERP)
适用功能
- 商业运营
用例
- 补货预测
- 减废预测
服务
- 系统集成
- 软件设计与工程服务
挑战
R+V Versicherung AG 是德国一家领先的保险提供商,其目标是打造“未来保险”。该公司希望在整个欧洲提供精简的保险服务,降低运营费用,并提供具有商业吸引力的保费费率。但是,其现有的业务管理解决方案无法提供全球范围的企业财务和工作流程视图。该公司希望更详细地了解自己的运营绩效,更有效地管理财务,并尽可能引入标准化流程的自动化。多年来,R+V 已经建立了一系列高度定制的专用应用程序来管理保费收取,其技术环境逐渐变得更加复杂,每个办公地点都有所差异。在快速变化的保险市场中,应用程序的复杂性也阻碍了 R+V 响应业务需求的能力,该市场还受到新法规和不断变化的法规的影响。
关于客户
R+V Versicherung AG 总部位于威斯巴登,是德国领先的保险提供商之一,为个人和企业客户提供定制保险服务。R+V 拥有近 700 万客户和约 13,000 名员工,2010 年保费收入超过 110 亿欧元。作为德国合作银行协会的一部分,该公司在德国各地的 Volks- und Raiffeisen 银行的 13,500 多家分行提供服务,并通过当地代表和代理机构进行销售。R+V 依靠 SAP ERP 解决方案来完成财务、会计和人力资源等核心业务管理任务。
解决方案
R+V 与 IBM 全球商业服务部及其他公司合作,改造其保费收取流程和组织结构。使用 IBM 组件业务模型 (CBM) 方法,R+V 能够分析其业务流程并设计流程优化的工作流管理以及相应的面向服务架构,以支持 SAP 保险收付款 (FS-CD) 的引入 - 这是该解决方案在欧洲的最大实施。结合 SAP 激励和佣金管理 (SAP FS-ICM) 和 Ferber Software 的 IKAROS 债务追偿管理解决方案,新平台可在整个企业内提供集成和自动化的工作流流程。新解决方案可连接到 12-15 个保单管理系统和在线门户,例如经纪人门户和呼叫中心门户。自动化接口将 SAP FS-CD 交易传输到 SAP 财务解决方案和 SAP NetWeaver 数据仓库。
运营影响
数量效益
相关案例.
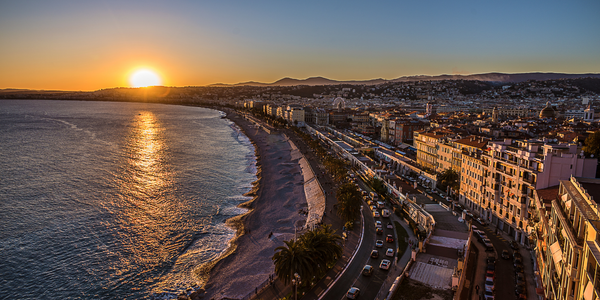
Case Study
PrismTech - Vortex platform in Nice’s Connected Boulevard project
In 2008, the City of Nice made a commitment to become a model Eco City and put in place a plan for renovation by launching the Connected Boulevard Project. One of the key areas of focus was to develop green transportation and reduce the negative consequences of urban activity on the citizens of the city.
Case Study
Designing an intuitive UI for effective product demand forecasting in retail
The client, a leading luxury store chain operating in over 100 countries, was facing challenges with their product demand forecasting process. The process involved a significant amount of manual work, with all sales-related data being kept in Excel tables and calculated manually. The client's merchandising and planning experts used a demand forecasting web application to make estimations of customer demand over a specific period of time. The solution calculated historical data and other analytical information to produce the most accurate predictions. However, the client wanted to improve the efficiency and effectiveness of this process, making it faster, more accurate, and less complicated for their employees. They sought to unify all processes under an intuitive UI.
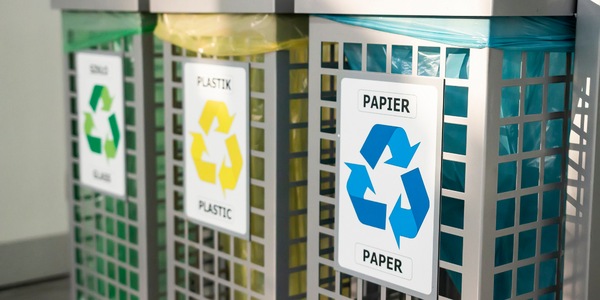
Case Study
Nordsense: Revolutionizing Waste Management with IoT
The world generates 2.01 billion tons of municipal solid waste annually, and traditional waste management methods are proving to be highly inefficient. Approximately 80% of waste is collected at the wrong time, leading to overflowing bins, unsanitary environments, citizen complaints, illegal dumping, and increased cleaning and collection costs. Early waste collections also contribute to unnecessary carbon emissions, increased traffic congestion, and higher operating costs. Nordsense, a Denmark-based company, aims to address these challenges and revolutionize the waste management sector using IoT sensors and data insights.
Case Study
Bosch Rexroth's Green Engineering Success with Altium Designer
Bosch Rexroth, a Fortune 100 company and one of the world’s largest suppliers of technology and services, has been committed to sustainability and green engineering practices for nearly half a century. The company recognizes the potential of green engineering to reduce costs, improve product performance, enhance corporate reputation, and open up new market opportunities. However, to truly be considered 'green', engineers must consider factors such as product life cycle, reusability, and the elimination of toxic chemicals. Bosch Rexroth’s engineering division faced the challenge of designing its latest Rexroth Frequency Converter Fe series to be more economical and environmentally friendly. The goal was to reduce parts, size, and power consumption, while improving reliability and stability.
Case Study
Blue Bottle Coffee Enhances Ordering Accuracy and Reduces Waste with ML-Driven Demand Forecasting
Blue Bottle Coffee (BBC), a global coffee roaster and retailer, faced a significant challenge in managing the supply of pastries across its international network of cafes. The company was using a manual ordering system, where cafe leaders estimated the required quantity of pastries based on historical sales data, current inventory, and growth projections. This system was effective when BBC had a few cafes, but with over 70 cafes worldwide, it became inefficient and inaccurate. The inaccuracies led to either under-ordering, causing sell-outs and customer dissatisfaction, or over-ordering, resulting in food waste and profit loss. The suboptimal utilization of pastries was also affecting BBC's bottom line. Therefore, BBC needed a scalable, precise, and predictive ordering solution to improve pastry ordering accuracy, reduce food waste, and meet its sustainability goals.