下载PDF
Recasting a High-end Foundry into a Data-driven Manufacturer
技术
- 分析与建模 - 实时分析
- 应用基础设施与中间件 - 数据交换与集成
- 功能应用 - 制造执行系统 (MES)
适用行业
- 汽车
- 航天
- 半导体
适用功能
- 质量保证
- 流程制造
- 产品研发
用例
- 预测性维护
- 机器状态监测
- 过程控制与优化
- 供应链可见性(SCV)
服务
- 系统集成
- 软件设计与工程服务
- 培训
挑战
Palmer Foundry faced significant challenges in meeting customer quality assurance guidelines due to data being scattered across multiple spreadsheets and laptops, making it difficult to access and analyze. The company also had limited statistical process control (SPC) skills and an overburdened IT department, which made the introduction of new software a concern. Despite their success in delivering high-quality products, Palmer needed to prove their quality control processes to meet industry guidelines and customer requirements. They saw an opportunity to adopt a manufacturing intelligence system to improve decision-making and business strategy.
关于客户
Palmer Foundry, located in Massachusetts, specializes in designing and manufacturing high-end, precision aluminum castings for various industries, including semiconductor, automotive, energy, aerospace, and robotics. The foundry is known for its demanding specifications and diligent control of raw materials and processes. Despite their success and customer satisfaction, Palmer faced pressure from existing and prospective customers to meet stringent quality assurance guidelines. The company realized the need to prove their quality control processes and saw an opportunity to adopt a manufacturing intelligence system to enhance their decision-making and business strategy.
解决方案
Palmer Foundry implemented NWA Focus EMI® from Northwest Analytics, a full-featured manufacturing intelligence solution. The installation was completed over the phone, and within three weeks, Palmer was operating with direct data-source connectivity, global analytics, real-time role-based visualization, and alarm notification services. NWA Focus EMI allowed Palmer to access data directly from original sources, pass it through a global analytics layer, and deliver actionable information through an intelligence viewer. This provided Palmer with real-time information, visual displays, and a color-coded warning system for deviations from project or raw materials parameters. The solution enabled Palmer to validate raw materials, gain greater process visibility and control, and provide documented process quality control data to customers.
运营影响
数量效益
相关案例.
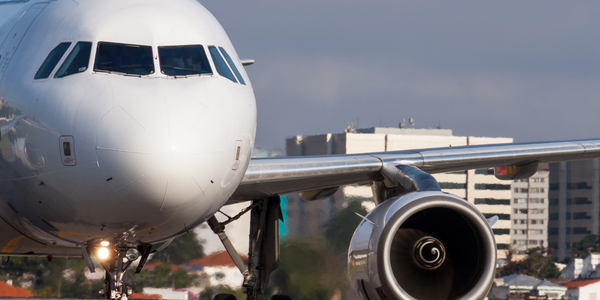
Case Study
Airbus Soars with Wearable Technology
Building an Airbus aircraft involves complex manufacturing processes consisting of thousands of moving parts. Speed and accuracy are critical to business and competitive advantage. Improvements in both would have high impact on Airbus’ bottom line. Airbus wanted to help operators reduce the complexity of assembling cabin seats and decrease the time required to complete this task.
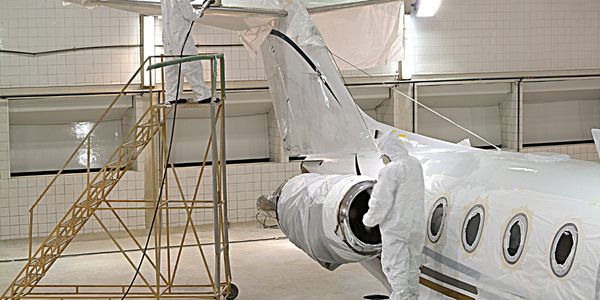
Case Study
Aircraft Predictive Maintenance and Workflow Optimization
First, aircraft manufacturer have trouble monitoring the health of aircraft systems with health prognostics and deliver predictive maintenance insights. Second, aircraft manufacturer wants a solution that can provide an in-context advisory and align job assignments to match technician experience and expertise.
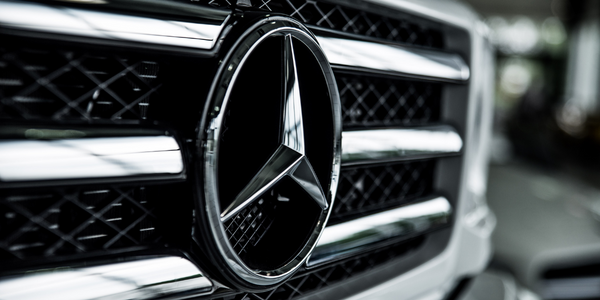
Case Study
Integral Plant Maintenance
Mercedes-Benz and his partner GAZ chose Siemens to be its maintenance partner at a new engine plant in Yaroslavl, Russia. The new plant offers a capacity to manufacture diesel engines for the Russian market, for locally produced Sprinter Classic. In addition to engines for the local market, the Yaroslavl plant will also produce spare parts. Mercedes-Benz Russia and his partner needed a service partner in order to ensure the operation of these lines in a maintenance partnership arrangement. The challenges included coordinating the entire maintenance management operation, in particular inspections, corrective and predictive maintenance activities, and the optimizing spare parts management. Siemens developed a customized maintenance solution that includes all electronic and mechanical maintenance activities (Integral Plant Maintenance).
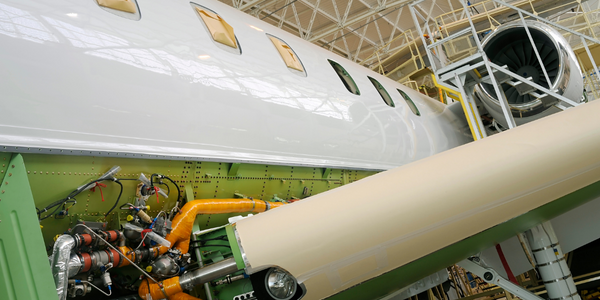
Case Study
Aerospace & Defense Case Study Airbus
For the development of its new wide-body aircraft, Airbus needed to ensure quality and consistency across all internal and external stakeholders. Airbus had many challenges including a very aggressive development schedule and the need to ramp up production quickly to satisfy their delivery commitments. The lack of communication extended design time and introduced errors that drove up costs.