下载PDF
Research, Recommendations, & Reality: How Gong Helped Mintel Increase Win Rates by 34%
技术
- 分析与建模 - 实时分析
适用功能
- 销售与市场营销
- 商业运营
用例
- 实时定位系统 (RTLS)
- 远程协作
服务
- 数据科学服务
- 系统集成
挑战
Mintel, a global leader in market research, was facing a challenge in improving their efficiency. With a large portfolio of over 6,000 clients worldwide, it was difficult for them to detect patterns in calls, which delayed improvements to customer service processes. They needed a single tool that could provide guidance based on data from feedback in client calls. The company was also struggling with getting internal teams up to speed with new initiatives, which often resulted in lost or stalled deals. The lack of a tool to review calls meant that the knowledge gap was not being closed quickly enough.
关于客户
Mintel is a global leader in market research with over 50 years of experience in understanding what consumers want and why. The company has a large portfolio of more than 6,000 clients worldwide. Mintel's go-to-market teams are data-driven and are always looking for ways to improve their effectiveness with customers. The company works with clients across many industries and often rolls out new initiatives. However, getting internal teams up to speed with these initiatives can consume valuable time, resulting in lost or stalled deals. Mintel's sales and client success teams were seeking a more efficient and effective way to deliver customer care based on feedback.
解决方案
Mintel adopted Gong, a tool that surfaces numbers that help them succeed by improving their internal and client-facing processes. Gong helped Mintel create a culture of coaching that enables employees to track their own progress and share client feedback with the colleagues who need to hear it most. Gong easily identifies areas for improvement so teams at Mintel can adopt policies that eliminate gaps in client service. The company also conducts pipeline reviews using Gong’s Deal Boards, enabling sales leaders to quickly scan stats and prioritize which deals need help now, based on how sales calls are going. Gong also provides advice to Mintel’s teams regularly and automatically, helping them improve their efficiency and win rate.
运营影响
数量效益
相关案例.
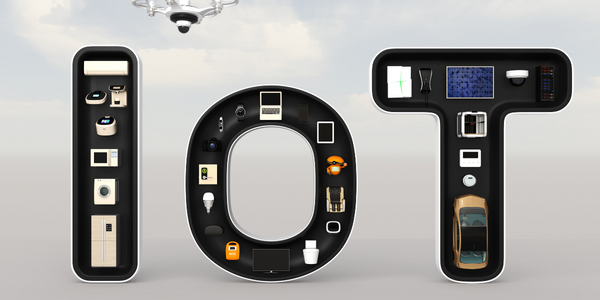
Case Study
Premium Appliance Producer Innovates with Internet of Everything
Sub-Zero faced the largest product launch in the company’s history:It wanted to launch 60 new products as scheduled while simultaneously opening a new “greenfield” production facility, yet still adhering to stringent quality requirements and manage issues from new supply-chain partners. A the same time, it wanted to increase staff productivity time and collaboration while reducing travel and costs.
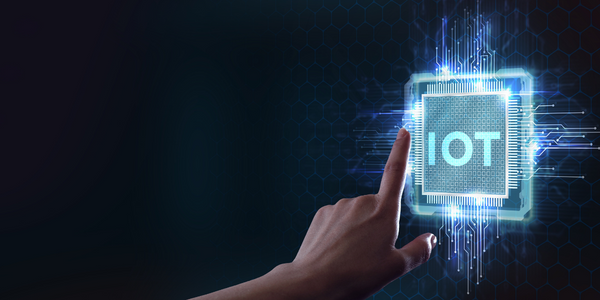
Case Study
Leading Tools Manufacturer Transforms Operations with IoT
Stanley Black & Decker required transparency of real-time overall equipment effectiveness and line productivity to reduce production line change over time.The goal was to to improve production to schedule, reduce actual labor costs and understanding the effects of shift changes and resource shifts from line to line.
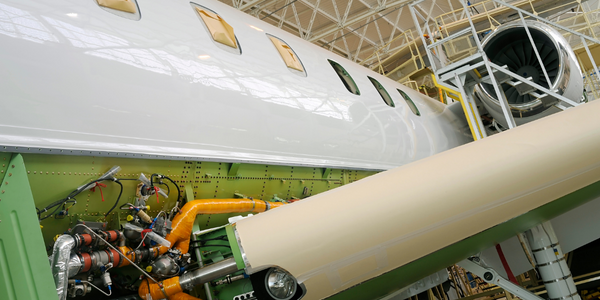
Case Study
Aerospace & Defense Case Study Airbus
For the development of its new wide-body aircraft, Airbus needed to ensure quality and consistency across all internal and external stakeholders. Airbus had many challenges including a very aggressive development schedule and the need to ramp up production quickly to satisfy their delivery commitments. The lack of communication extended design time and introduced errors that drove up costs.
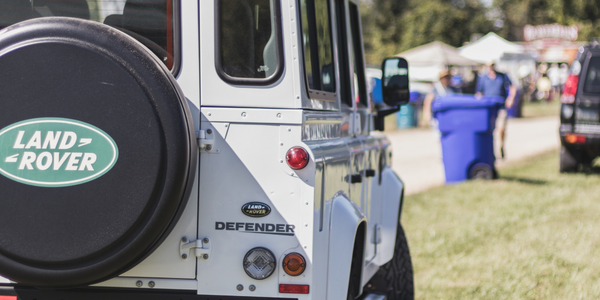
Case Study
Jaguar Land Rover Speeds Order-to-Cash Cycle
At Jaguar Land Rover, vehicles physically move around the facility for testing, configuration setting, rework and rectification, leading to a longer search time to get each vehicle to its next process facility. The main goal is to minimize the vehicles' dwell time between end of line and the delivery chain which was previously a manually intensive process. Jaguar Land Rover's goal was to build on the success of an earlier RFID project and improve the efficiency of delivering vehicles to meet dealer orders.
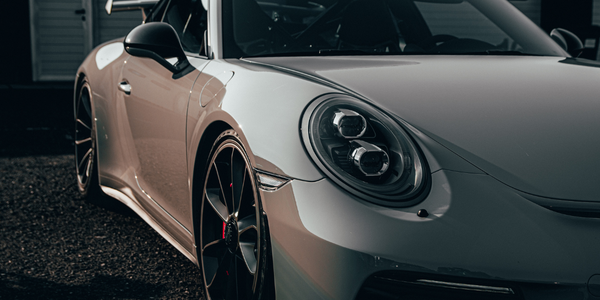
Case Study
Porsche Announces Augmented Reality at Scale, Powered by Atheer
The usual practice for car repairs at a Porsche car dealership is to have a factory representative or regional engineer visit to help diagnose the problem, and sometimes a faulty assembly is shipped back to company HQ for damage analysis. All that costs time and money for customers and dealers alike.
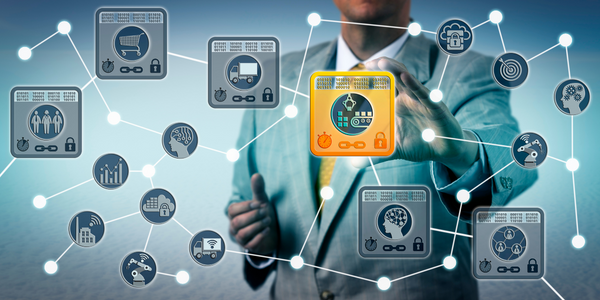
Case Study
Covisint Improves Mitsubishi's Collaboration With Its Supply Chain
Mitsubishi sought to improve supplier relationships on a global basis and to offer an easy-to-use solution to interact with them. In August 2004, Mitsubishi selected Covisint’s platform to help improve sharing of information and collaborative business processes with its global suppliers. Covisint enabled Mitsubishi to provide its suppliers with immediate access to information and applications to obtain more collaborative working relationships