下载PDF
Sigma Alimentos desires automation for new expansion
技术
- 自动化与控制 - 自动化与过程控制系统
- 功能应用 - 仓库管理系统 (WMS)
- 功能应用 - 远程监控系统
适用行业
- 食品与饮料
适用功能
- 仓库和库存管理
- 物流运输
用例
- 库存管理
- 仓库自动化
- 预测性维护
服务
- 系统集成
- 软件设计与工程服务
挑战
Due to their success and growth, Sigma determined the need for a new large distribution center, to support a number of smaller, second tier distribution centers. The new facility was partially under construction as a conventional operation, when it was determined by Sigma they desired to automate this facility. One parameter of the project was the need to use the already installed steel framing structure in the building – not to tear it and start over. Sigma Alimentos required the new cooler (40° F) distribution center to support full pallet storage, case picking, buffering of pre-picked items for future retrieval and truck loading, and the automation of the inventory management process to support all their warehousing operations. Sigma Alimentos pallets are 40” x 48” and weigh up to 3300 lbs. fully loaded. Westfalia’s Savanna.NET® WMS would need to interface with Sigma’s existing host software system. Westfalia designers worked closely with Sigma’s executives to define and meet specific requirements using both standard and customized system elements.
关于客户
A division of Grupo Alfa, Sigma Alimentos operates one of Mexico’s largest refrigerated distribution networks and leads the Mexican market in processed meat and cheese products, with brands that include Chalet and El Cazo Mexicano. Sigma recently installed a Westfalia Automated Storage & Retrieval System (AS/RS) at their new distribution center in Monterrey, Mexico. This new refrigerated distribution center was Sigma’s first automated warehouse, and utilizes Westfalia’s Savanna.NET® Warehouse Management System (WMS) too.
解决方案
The AS/RS configured by Westfalia to fit within the existing structure includes two Storage Retrieval Machines (SRM), one in each aisle, plus a center pick tunnel within the rack structure. Unique system features include order picking lanes on both the outside and within the AS/RS rack structure, two and four-pallet capacity high speed transfer cars, accumulation conveyors at shipping, stretch wrapping, and the ability to add dual (two) load handling capability on each of the SRM’s for future expansion in capacity “throughput.” The conveying system includes 3-strand, CDLR’s, gravity rollers, right angle transfer cars, a newly designed quad transfer car, a pallet squaring station, a slave board dispenser, and an electric pallet dispenser. All pallet movements and machinery are controlled by Savanna.Net and interface to Sigma’s SAP host software. The Satellite® load handling device moves pallets quickly and smoothly in and out of the racks, and onto the SRM. The entire system is capable of placing pallets loads up to 12 pallets deep in a single storage lane, and of having various lane depths within a single aisle. In Sigma Alimentos case, pallets will be stored 4- and 5- deep in storage lanes.
运营影响
数量效益
相关案例.
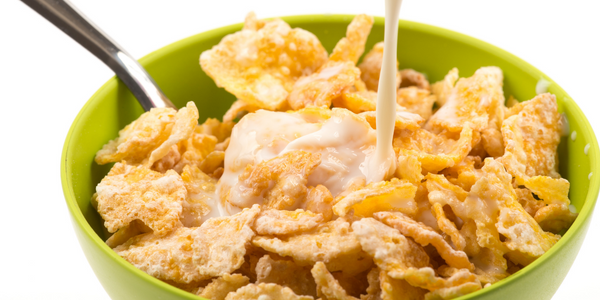
Case Study
The Kellogg Company
Kellogg keeps a close eye on its trade spend, analyzing large volumes of data and running complex simulations to predict which promotional activities will be the most effective. Kellogg needed to decrease the trade spend but its traditional relational database on premises could not keep up with the pace of demand.
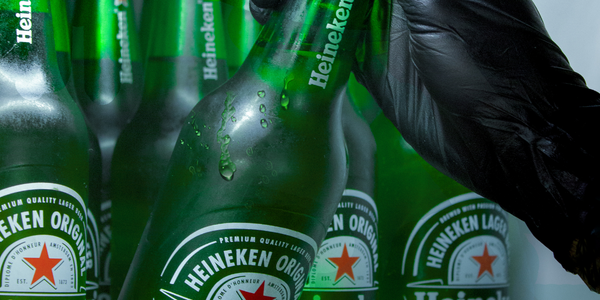
Case Study
HEINEKEN Uses the Cloud to Reach 10.5 Million Consumers
For 2012 campaign, the Bond promotion, it planned to launch the campaign at the same time everywhere on the planet. That created unprecedented challenges for HEINEKEN—nowhere more so than in its technology operation. The primary digital content for the campaign was a 100-megabyte movie that had to play flawlessly for millions of viewers worldwide. After all, Bond never fails. No one was going to tolerate a technology failure that might bruise his brand.Previously, HEINEKEN had supported digital media at its outsourced datacenter. But that datacenter lacked the computing resources HEINEKEN needed, and building them—especially to support peak traffic that would total millions of simultaneous hits—would have been both time-consuming and expensive. Nor would it have provided the geographic reach that HEINEKEN needed to minimize latency worldwide.
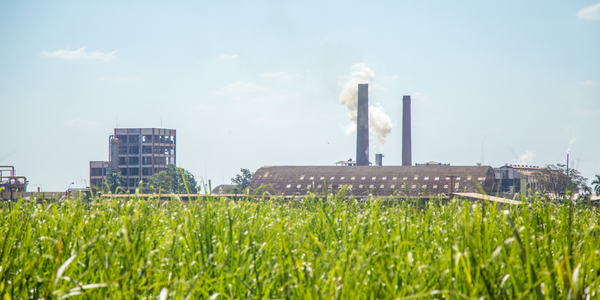
Case Study
Energy Management System at Sugar Industry
The company wanted to use the information from the system to claim under the renewable energy certificate scheme. The benefit to the company under the renewable energy certificates is Rs 75 million a year. To enable the above, an end-to-end solution for load monitoring, consumption monitoring, online data monitoring, automatic meter data acquisition which can be exported to SAP and other applications is required.
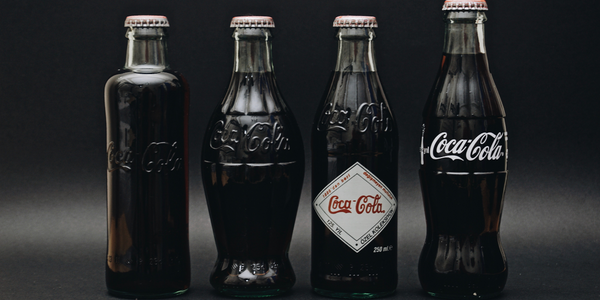
Case Study
Coca Cola Swaziland Conco Case Study
Coco Cola Swaziland, South Africa would like to find a solution that would enable the following results: - Reduce energy consumption by 20% in one year. - Formulate a series of strategic initiatives that would enlist the commitment of corporate management and create employee awareness while helping meet departmental targets and investing in tools that assist with energy management. - Formulate a series of tactical initiatives that would optimize energy usage on the shop floor. These would include charging forklifts and running cold rooms only during off-peak periods, running the dust extractors only during working hours and basing lights and air-conditioning on someone’s presence. - Increase visibility into the factory and other processes. - Enable limited, non-intrusive control functions for certain processes.
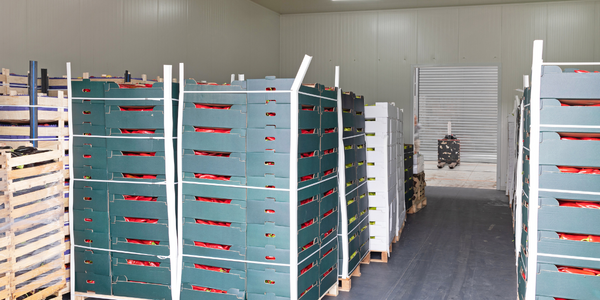
Case Study
Temperature Monitoring for Restaurant Food Storage
When it came to implementing a solution, Mr. Nesbitt had an idea of what functionality that he wanted. Although not mandated by Health Canada, Mr. Nesbitt wanted to ensure quality control issues met the highest possible standards as part of his commitment to top-of-class food services. This wish list included an easy-to use temperature-monitoring system that could provide a visible display of the temperatures of all of his refrigerators and freezers, including historical information so that he could review the performance of his equipment. It also had to provide alert notification (but email alerts and SMS text message alerts) to alert key staff in the event that a cooling system was exceeding pre-set warning limits.
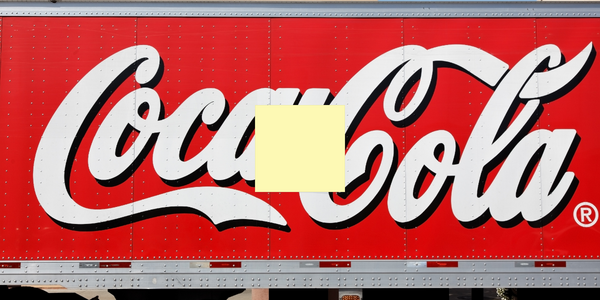
Case Study
Coca-Cola Refreshments, U.S.
Coca-Cola Refreshments owns and manages Coca-Cola branded refrigerators in retail establishments. Legacy systems were used to locate equipment information by logging onto multiple servers which took up to 8 hours to update information on 30-40 units. The company had no overall visibility into equipment status or maintenance history.