下载PDF
Technicolor Ups Its Game with a Multimodal TMS
技术
- 功能应用 - 运输管理系统 (TMS)
- 功能应用 - 仓库管理系统 (WMS)
适用功能
- 物流运输
- 仓库和库存管理
用例
- 车队管理
- 库存管理
- 供应链可见性(SCV)
- 预测性维护
服务
- 系统集成
- 软件设计与工程服务
挑战
Technicolor faced the challenge of managing high volumes of parcel shipments efficiently and cost-effectively, ensuring timely deliveries for important product launches and movie premieres. The company needed a solution that could handle the increasing demand for physical media and entertainment-related devices, while also managing cross-border shipments and various transportation modes. The pressure to meet delivery deadlines and optimize costs across different transportation modes added to the complexity of their logistics operations.
关于客户
Technicolor SA, a Paris-based company, is a digital innovator with a rich history in the cinema industry. The company provides advanced visual and audio postproduction services for television, movies, and games, and produces physical media like DVDs, Blu-ray discs, and CDs. Technicolor also explores new consumer experiences in theaters and at home, with research and innovation labs making advances in connected home technology, artificial intelligence, imaging science, and immersive entertainment like virtual reality. Technicolor Global Logistics (TGL), the company's 3PL unit, launched in 2006, provides fulfillment, distribution, and replenishment services to retailers and theaters for major Hollywood studios and other clients.
解决方案
Technicolor selected MercuryGate TMS to manage its logistics operations. The TMS, with parcel management as a native feature, allows Technicolor to process parcel shipments quickly and analyze, compare, and make decisions across different transportation modes on a single platform. The integration of the Mojo software module further enhances the TMS by comparing cost and service across all transportation modes, identifying profitable consolidation opportunities, and ensuring timely deliveries. This solution enables Technicolor to handle high volumes of shipments efficiently, meeting customer delivery requirements and optimizing costs.
运营影响
数量效益
相关案例.
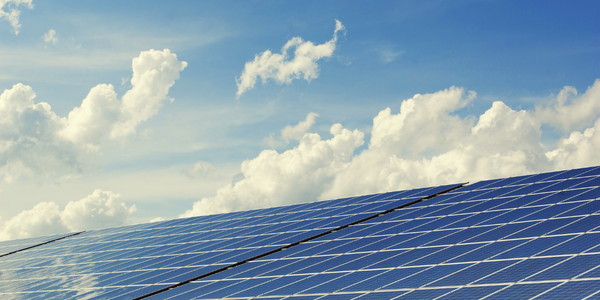
Case Study
Remote Monitoring & Predictive Maintenance App for a Solar Energy System
The maintenance & tracking of various modules was an overhead for the customer due to the huge labor costs involved. Being an advanced solar solutions provider, they wanted to ensure early detection of issues and provide the best-in-class customer experience. Hence they wanted to automate the whole process.
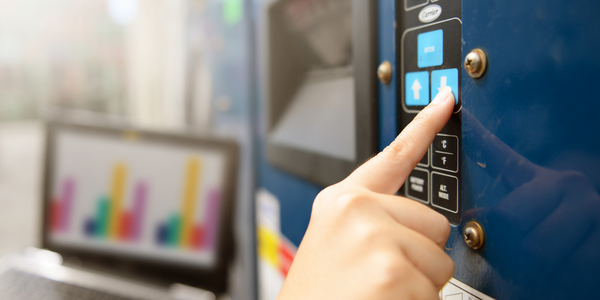
Case Study
Remote Temperature Monitoring of Perishable Goods Saves Money
RMONI was facing temperature monitoring challenges in a cold chain business. A cold chain must be established and maintained to ensure goods have been properly refrigerated during every step of the process, making temperature monitoring a critical business function. Manual registration practice can be very costly, labor intensive and prone to mistakes.
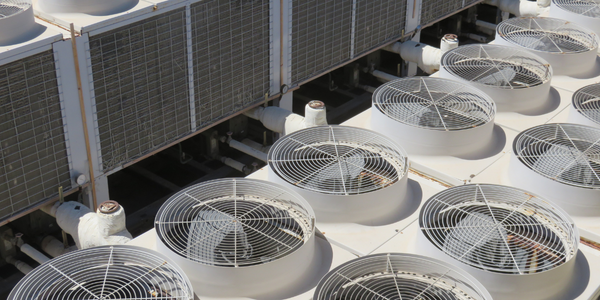
Case Study
Predictive Maintenance for Industrial Chillers
For global leaders in the industrial chiller manufacturing, reliability of the entire production process is of the utmost importance. Chillers are refrigeration systems that produce ice water to provide cooling for a process or industrial application. One of those leaders sought a way to respond to asset performance issues, even before they occur. The intelligence to guarantee maximum reliability of cooling devices is embedded (pre-alarming). A pre-alarming phase means that the cooling device still works, but symptoms may appear, telling manufacturers that a failure is likely to occur in the near future. Chillers who are not internet connected at that moment, provide little insight in this pre-alarming phase.
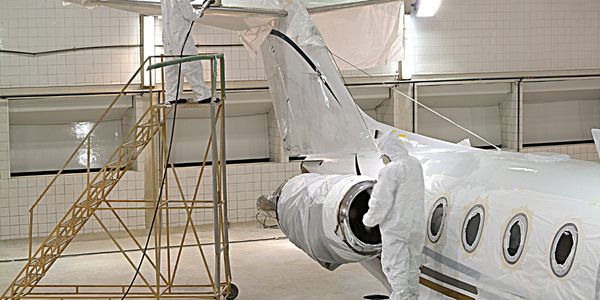
Case Study
Aircraft Predictive Maintenance and Workflow Optimization
First, aircraft manufacturer have trouble monitoring the health of aircraft systems with health prognostics and deliver predictive maintenance insights. Second, aircraft manufacturer wants a solution that can provide an in-context advisory and align job assignments to match technician experience and expertise.
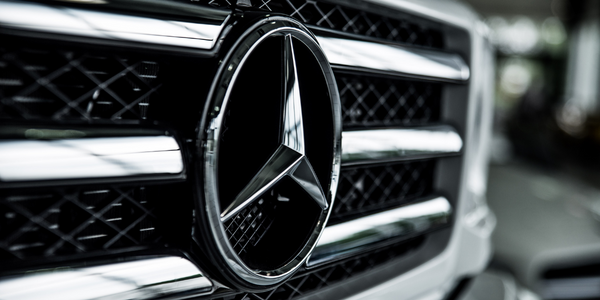
Case Study
Integral Plant Maintenance
Mercedes-Benz and his partner GAZ chose Siemens to be its maintenance partner at a new engine plant in Yaroslavl, Russia. The new plant offers a capacity to manufacture diesel engines for the Russian market, for locally produced Sprinter Classic. In addition to engines for the local market, the Yaroslavl plant will also produce spare parts. Mercedes-Benz Russia and his partner needed a service partner in order to ensure the operation of these lines in a maintenance partnership arrangement. The challenges included coordinating the entire maintenance management operation, in particular inspections, corrective and predictive maintenance activities, and the optimizing spare parts management. Siemens developed a customized maintenance solution that includes all electronic and mechanical maintenance activities (Integral Plant Maintenance).