下载PDF
University of Texas – Arlington Leverages IoT for Racecar Design
技术
- 分析与建模 - 数字孪生/模拟
- 传感器 - 自动驾驶传感器
适用行业
- 航天
- 汽车
适用功能
- 产品研发
- 销售与市场营销
用例
- 时间敏感网络
- 虚拟现实
服务
- 测试与认证
挑战
德克萨斯大学阿灵顿分校的 Formula SAE 赛车队在重新设计 2019 年赛车的踏板箱组件时面临着重大挑战。以前的踏板盒组件由碳纤维和泡沫芯体制成,带有铝制踏板和安装件,存在车身弯曲和需要加固的问题,不幸的是,这增加了超出原始设计的重量。该团队还发现设计和模拟过程非常耗时。面临的挑战是使踏板盒组件更坚固、更轻且更易于制造,同时减少设计和仿真所花费的时间。
关于客户
德克萨斯大学阿灵顿分校 (UTA) Racing FSAE 团队成立于 1976 年,一直参加美国、英国、日本和澳大利亚的各种比赛。 37 年来,该团队已制造了 30 多辆汽车,并在多个国家登上了领奖台。该团队分为九个子系统,每个子系统由一名总工程师领导,负责系统集成和主要设计目标。 UTA Racing 隶属于德克萨斯大学阿灵顿分校机械与航空航天 (MAE) 系。
解决方案
该团队决定使用铝制部件而不是碳纤维部件重新设计踏板箱组件,这将使制造和修改变得更容易(如有必要)。他们使用 Altair 的 SimLab 进行仿真研究,该模型提供了更快且结构良好的输出。该模型使用 Optistruct 在 HyperMesh 中求解。在评估和选择各种设计后,团队以相同的方式制造了所有组件。踏板箱设计为可针对不同驾驶员进行调节,并满足 95% 男性和 5% 女性驾驶员模板的 FSAE 规则。
运营影响
数量效益
相关案例.
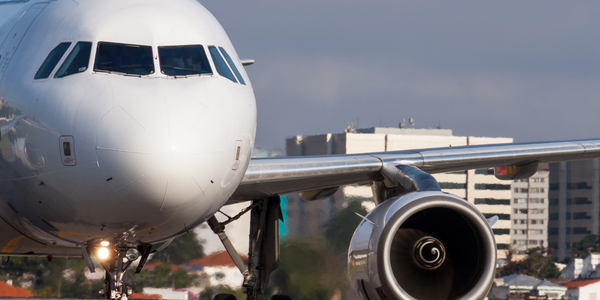
Case Study
Airbus Soars with Wearable Technology
Building an Airbus aircraft involves complex manufacturing processes consisting of thousands of moving parts. Speed and accuracy are critical to business and competitive advantage. Improvements in both would have high impact on Airbus’ bottom line. Airbus wanted to help operators reduce the complexity of assembling cabin seats and decrease the time required to complete this task.
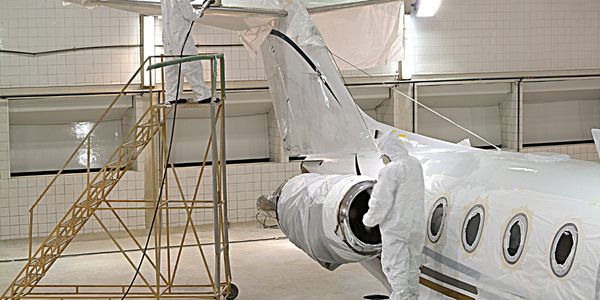
Case Study
Aircraft Predictive Maintenance and Workflow Optimization
First, aircraft manufacturer have trouble monitoring the health of aircraft systems with health prognostics and deliver predictive maintenance insights. Second, aircraft manufacturer wants a solution that can provide an in-context advisory and align job assignments to match technician experience and expertise.
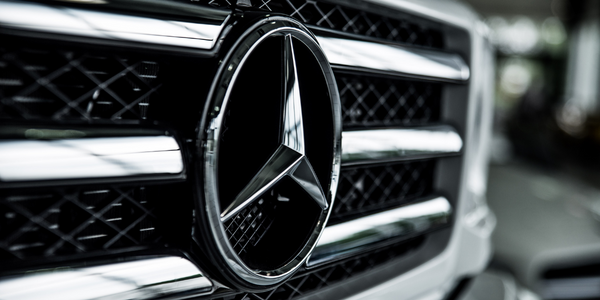
Case Study
Integral Plant Maintenance
Mercedes-Benz and his partner GAZ chose Siemens to be its maintenance partner at a new engine plant in Yaroslavl, Russia. The new plant offers a capacity to manufacture diesel engines for the Russian market, for locally produced Sprinter Classic. In addition to engines for the local market, the Yaroslavl plant will also produce spare parts. Mercedes-Benz Russia and his partner needed a service partner in order to ensure the operation of these lines in a maintenance partnership arrangement. The challenges included coordinating the entire maintenance management operation, in particular inspections, corrective and predictive maintenance activities, and the optimizing spare parts management. Siemens developed a customized maintenance solution that includes all electronic and mechanical maintenance activities (Integral Plant Maintenance).
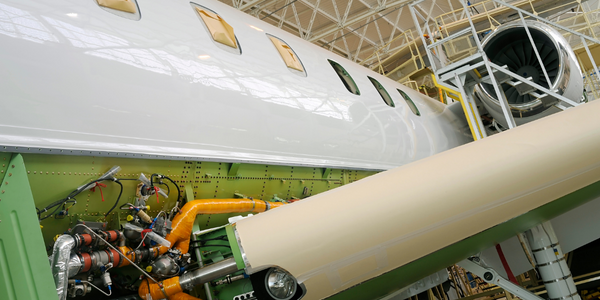
Case Study
Aerospace & Defense Case Study Airbus
For the development of its new wide-body aircraft, Airbus needed to ensure quality and consistency across all internal and external stakeholders. Airbus had many challenges including a very aggressive development schedule and the need to ramp up production quickly to satisfy their delivery commitments. The lack of communication extended design time and introduced errors that drove up costs.