下载PDF
US Synthetic cuts the scrap with QlikView business analysis
技术
- 分析与建模 - 实时分析
适用行业
- 石油和天然气
适用功能
- 人力资源
用例
- 预测性维护
- 实时定位系统 (RTLS)
服务
- 数据科学服务
挑战
US Synthetic, a leading provider of polycrystalline diamond cutters (PDCs) for oil and gas exploration, faced challenges in reporting and analysis. The company's Made2Manage ERP system and internally developed custom tables contained large amounts of detailed data, but employees were not able to utilize that data in a meaningful way. Even the generic reports within Made2Manage were difficult to access, and creating ad hoc reports was even more time-consuming and inefficient. The company needed a solution that would provide real, accessible, and useful information at all levels within the organization. The company's non-linear floor made it challenging for managers to follow the product from work order to delivery. Because products may backtrack in the process flow and ultimately take a different route to completion, production managers were losing visibility of those products and their status.
关于客户
US Synthetic is the leading provider of polycrystalline diamond cutters (PDCs) for oil and gas exploration. The company has spent more than a decade perfecting its products to drill faster and last longer – especially in tough conditions that test the limits of the most durable drilling equipment. The company employs over 600 people, and is located in Orem, Utah. US Synthetic is part of Dover Corporation. In 1997, US Synthetic became the industry’s leading supplier of diamond products. Over 10 years later, US Synthetic continues to actively expand this leadership position – not only by developing innovative new diamond solutions, but also by ensuring process efficiency within internal operations.
解决方案
US Synthetic deployed QlikView to 50 employees for operational analysis in only one week. Through QlikView, US Synthetic now analyzes yields and production, lead time, customer profitability, and safety rates. With QlikView Server and Publisher, US Synthetic easily supports analysis and visibility while handling the large data volume of millions of records. The company was able to build the first application – a production floor dashboard – in a five-day engagement with a QlikView consultant. The Yields & Production application was an important priority for US Synthetic, as it allowed the company to track and compare yields and problems across days, factories, and shifts. US Synthetic is now able to determine which factories are performing best against standard cost/yield. Product line and floor managers are able to identify trends in product quality and performance and proactively make adjustments at any factory that may be underperforming.
运营影响
数量效益
相关案例.
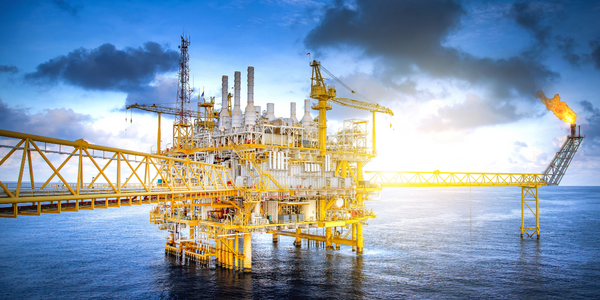
Case Study
Taking Oil and Gas Exploration to the Next Level
DownUnder GeoSolutions (DUG) wanted to increase computing performance by 5 to 10 times to improve seismic processing. The solution must build on current architecture software investments without sacrificing existing software and scale computing without scaling IT infrastructure costs.
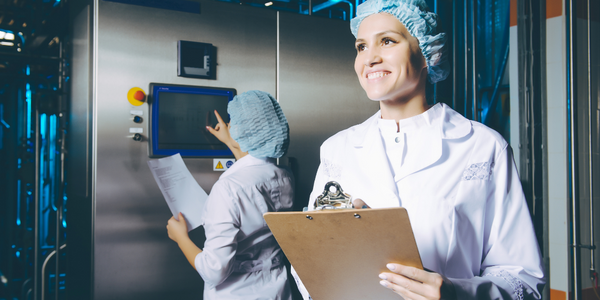
Case Study
Remote Wellhead Monitoring
Each wellhead was equipped with various sensors and meters that needed to be monitored and controlled from a central HMI, often miles away from the assets in the field. Redundant solar and wind generators were installed at each wellhead to support the electrical needs of the pumpstations, temperature meters, cameras, and cellular modules. In addition to asset management and remote control capabilities, data logging for remote surveillance and alarm notifications was a key demand from the customer. Terra Ferma’s solution needed to be power efficient, reliable, and capable of supporting high-bandwidth data-feeds. They needed a multi-link cellular connection to a central server that sustained reliable and redundant monitoring and control of flow meters, temperature sensors, power supply, and event-logging; including video and image files. This open-standard network needed to interface with the existing SCADA and proprietary network management software.
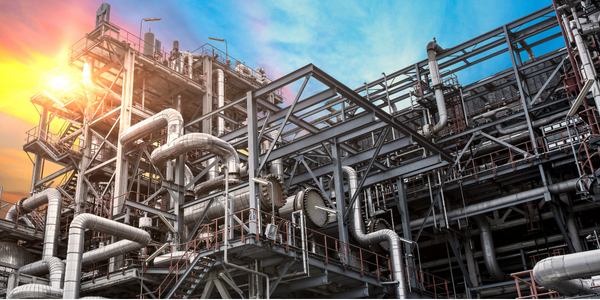
Case Study
Refinery Saves Over $700,000 with Smart Wireless
One of the largest petroleum refineries in the world is equipped to refine various types of crude oil and manufacture various grades of fuel from motor gasoline to Aviation Turbine Fuel. Due to wear and tear, eight hydrogen valves in each refinery were leaking, and each cost $1800 per ton of hydrogen vented. The plant also had leakage on nearly 30 flare control hydrocarbon valves. The refinery wanted a continuous, online monitoring system that could catch leaks early, minimize hydrogen and hydrocarbon production losses, and improve safety for maintenance.