下载PDF
Yamaha Streamlines Contract Creation with Nintex DocGen™ for Salesforce
技术
- 传感器 - 声学传感器
- 传感器 - 全球定位系统
适用行业
- 包装
- 零售
适用功能
- 物流运输
- 销售与市场营销
用例
- 智能包装
- 智能合约
挑战
雅马哈是一家领先的乐器和音频设备供应商,在管理其法律合同和协议方面面临着重大挑战。公司的发展导致了不同部门的创建,每个部门都有自己的一套法律证据和协议,规定了产品如何营销和销售。这些部门销售给拥有多个商店地点的零售商,使得手动创建文档成为一项复杂且耗时的任务。当国民帐户包含来自多个雅马哈部门的产品时,该过程变得更加复杂,需要每个部门的主经销商协议和法律协议。大量的电子邮件和文件常常让零售商感到困惑,导致文件被忽视或不完整。尽管是 Salesforce 和 DocuSign 用户,雅马哈仍必须走出这些环境来完成文档,从而产生了对文档自动化解决方案的渴望。
关于客户
雅马哈是世界领先的乐器和音频设备供应商之一。他们的产品满足广泛的客户需求,从学生到专业音乐家和唱片艺术家。公司的发展导致其多样化的产品和分销渠道创建了不同的部门,包括 PAC(吉他、音箱、鼓)、乐队和管弦乐队(行进乐队、玫瑰游行)以及键盘部门。每个部门都有自己的一套法律证据和协议,规定其产品的营销和销售方式。这些部门向拥有数十甚至数百家商店或经销商的零售商销售产品。
解决方案
Yamaha 求助于 Nintex DocGen for Salesforce 来管理整个文档创建过程。该系统允许 Yamaha 直接将 Salesforce 数据合并到文档中,并将单个文档包发送给零售商和经销商。雅马哈开展的第一个项目是自动化信用申请流程。他们创建了一个 Nintex DocGen 文档包,其中包括信贷应用程序和其他支持文档,直接从 Salesforce 提取数据以预填充字段。 Nintex DocGen 还帮助 Yamaha 自动生成、组装和分发主经销商协议 (MDA)、法律协议以及 Yamaha 公司和部门向零售商及其经销商展示的内容。雅马哈创建了一个包含所有必要合同和协议的单一文档包。他们通过内置触发器进一步改进了流程,以便在收到签名的文档包时,父协议和子协议都将自动更新,并将历史记录记录在 Salesforce 中。
运营影响
数量效益
相关案例.
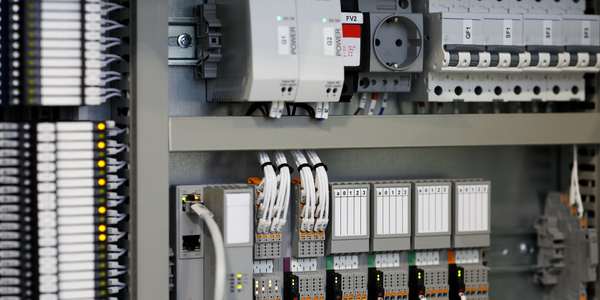
Case Study
Improving Production Line Efficiency with Ethernet Micro RTU Controller
Moxa was asked to provide a connectivity solution for one of the world's leading cosmetics companies. This multinational corporation, with retail presence in 130 countries, 23 global braches, and over 66,000 employees, sought to improve the efficiency of their production process by migrating from manual monitoring to an automatic productivity monitoring system. The production line was being monitored by ABB Real-TPI, a factory information system that offers data collection and analysis to improve plant efficiency. Due to software limitations, the customer needed an OPC server and a corresponding I/O solution to collect data from additional sensor devices for the Real-TPI system. The goal is to enable the factory information system to more thoroughly collect data from every corner of the production line. This will improve its ability to measure Overall Equipment Effectiveness (OEE) and translate into increased production efficiencies. System Requirements • Instant status updates while still consuming minimal bandwidth to relieve strain on limited factory networks • Interoperable with ABB Real-TPI • Small form factor appropriate for deployment where space is scarce • Remote software management and configuration to simplify operations
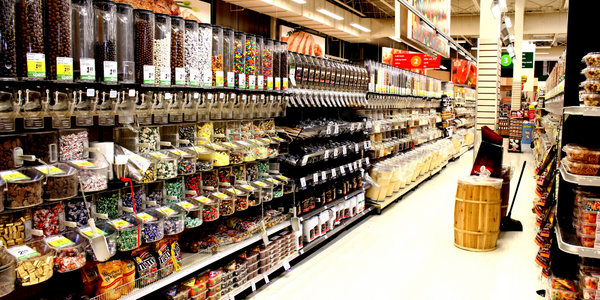
Case Study
How Sirqul’s IoT Platform is Crafting Carrefour’s New In-Store Experiences
Carrefour Taiwan’s goal is to be completely digital by end of 2018. Out-dated manual methods for analysis and assumptions limited Carrefour’s ability to change the customer experience and were void of real-time decision-making capabilities. Rather than relying solely on sales data, assumptions, and disparate systems, Carrefour Taiwan’s CEO led an initiative to find a connected IoT solution that could give the team the ability to make real-time changes and more informed decisions. Prior to implementing, Carrefour struggled to address their conversion rates and did not have the proper insights into the customer decision-making process nor how to make an immediate impact without losing customer confidence.
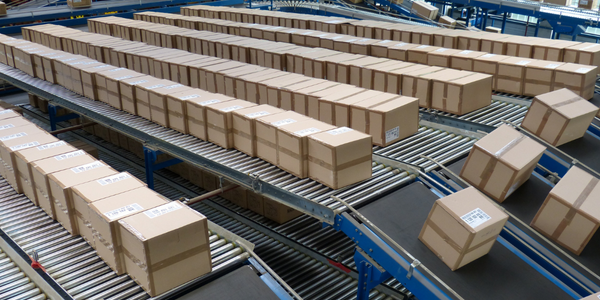
Case Study
IoT Data Analytics Case Study - Packaging Films Manufacturer
The company manufactures packaging films on made to order or configure to order basis. Every order has a different set of requirements from the product characteristics perspective and hence requires machine’s settings to be adjusted accordingly. If the film quality does not meet the required standards, the degraded quality impacts customer delivery causes customer dissatisfaction and results in lower margins. The biggest challenge was to identify the real root cause and devise a remedy for that.
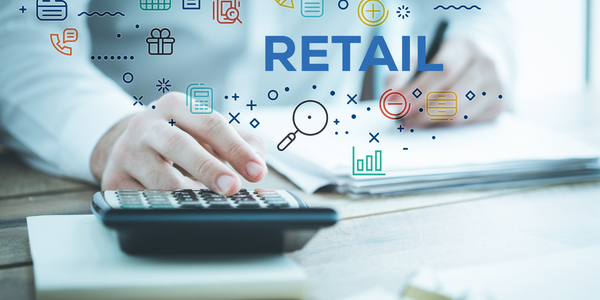
Case Study
Digital Retail Security Solutions
Sennco wanted to help its retail customers increase sales and profits by developing an innovative alarm system as opposed to conventional connected alarms that are permanently tethered to display products. These traditional security systems were cumbersome and intrusive to the customer shopping experience. Additionally, they provided no useful data or analytics.
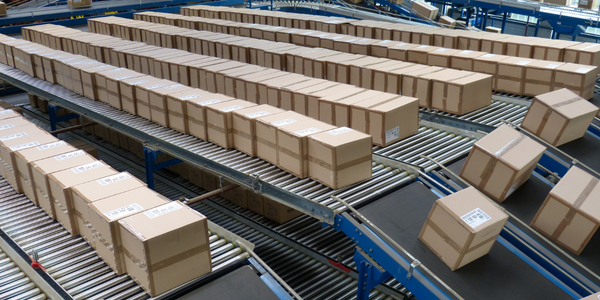
Case Study
Zenon the Ideal Basis for An Ergonomic HMI
KHS develops and produces machines and equipment for filling and packaging in the drinks industry. Because drinks manufacturing, filling and packaging consist of a number of highly complex processes, the user-friendly and intuitive operation of equipment is increasingly gaining in significance. In order to design these processes as simple as possible for the user, KHS decided to introduce a uniform, transparent and standardized solution to the company. The HMI interface should meet the requirement for people with different qualifications and enable them to work on a standard platform.