Download PDF
AllStyle Coil's Transformation with OptiProERP and SAP Business One
Technology Category
- Analytics & Modeling - Real Time Analytics
- Functional Applications - Manufacturing Execution Systems (MES)
Applicable Functions
- Procurement
- Warehouse & Inventory Management
Use Cases
- Additive Manufacturing
- Manufacturing Process Simulation
Services
- System Integration
The Challenge
AllStyle Coil Company, the largest independent coil manufacturer in the United States, was facing significant challenges with their existing IBM AS400 system. The system had become too expensive to maintain and was not providing the necessary manufacturing functionality. The company had grown from a 40,000-square-foot to an 800,000-square-foot manufacturing facility, and their existing system was not able to keep up with the growth. They had tried to deploy Global Shop Solutions, but found it too rigid and ineffective for their needs. They needed a system that could handle their business from end to end, provide real-time updates on orders, and offer deeper visibility into financial operations.
About The Customer
AllStyle Coil Company is the largest independent coil manufacturer in the United States and a leader in HVAC innovation. The family-owned business has grown from a 40,000-square-foot to an 800,000-square-foot manufacturing facility. They are known for their commitment to quality and innovation, and they have a reputation for being a leader in their industry. They have a diverse customer base and a wide range of products, and they are constantly looking for ways to improve their operations and provide better service to their customers.
The Solution
AllStyle Coil chose to implement OptiProERP with SAP Business One, replacing multiple systems. They chose OptiProERP for its simplicity, flexibility, and ability to handle all their business and manufacturing processes. The software's automated business and manufacturing capabilities are helping AllStyle Coil eliminate duplicate manual entries, provide customers with real-time updates on orders, and have deeper visibility into financial operations. Inventory counts are now automated, significantly reducing errors. Additionally, with all data housed in one system, anyone can find order statuses instantly without physically tracking down a purchase order and going to manufacturing to see where it is on the production schedule. AllStyle Coil also plans to adopt a customer portal integrated with OptiProERP so customers can see and track orders.
Operational Impact
Quantitative Benefit
Related Case Studies.
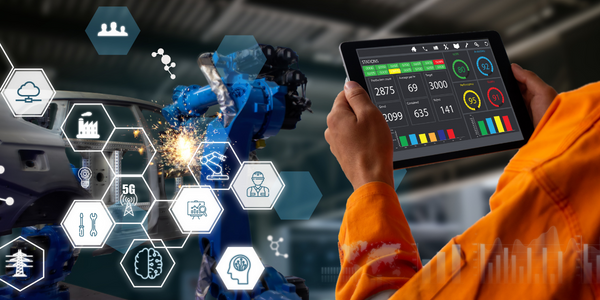
Case Study
Battery manufacturer Industrial Digital Twin
For optimum control of product quality, Banner relies on a high production depth. Its 560 production employees produce nearly all the components in¬-house that they need to make finished batteries on Banner’s six assembly lines. This includes the plastic parts for the battery cases as well as the paste-filled lead oxide grids. Their production involves two to five¬ days rest in maturing chambers to create optimum current absorption and storage capacity. Banner’s ongoing success was accompanied by a continuous, organic growth of the production facilities, adding or extending hall after hall until the complex filled the site that had seemed ever so spacious when the company moved here from a smaller place in 1959. These developments led to a heterogeneous production environment. “This confronts us with significant challenges, particularly concerning intra¬logistics issues, such as scheduling for the maturing chambers,” says Franz Dorninger, technical director at Banner. “We contemplated various ways to overcome this problem, including relocating to new premises.”
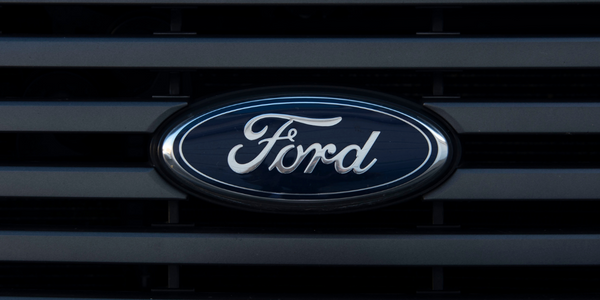
Case Study
Ford Motor Company on the Road to 3D Manufacturing
To date, key challenges have stood in the way of 3D printing becoming a manufacturing tool for the automaker. The first issue is a fundamental one — conventional 3D printing technologies make parts layer-by-layer, slowly crafting one layer at a time, creating parts that aren’t nearly as robust as those stamped or injection molded. While the slow speed of this process is a major drawback, the bigger problem is that the parts produced are not isotropic and not durable enough to be used in production vehicles. In addition, most parts used in vehicles today must withstand temperature extremes from the hottest desert to the coldest Arctic environments and still maintain their integrity. With only a handful of stock materials available for 3D printers, meeting the automaker’s unique demands has not been possible.
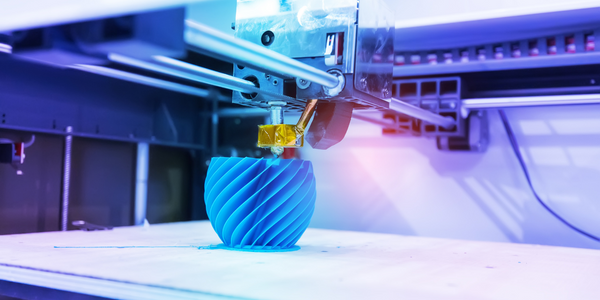
Case Study
3D Printed Prototypes Streamline Equipment Introduction
Vauxhall set out to introduce a modified process hanger with a new part that would be used to support each vehicle body throughout the production process. This part is a critical piece and had to perfectly fit both the machinery and the auto body to create correct clearances and avoid damage during production.
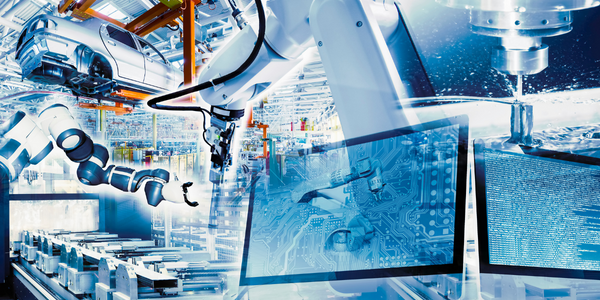
Case Study
Bekaert's Journey to Manufacturing Digitalization with TCS
Bekaert, a major player in the steel wire industry, was facing significant challenges in its manufacturing operations due to outdated data platforms. The company was unable to trace genealogy beyond a week's data and lacked diagnostic analysis of plant operations, which severely hampered decision-making. The absence of automation in benchmarking operations and extensive reporting on plant management further complicated the situation. To enhance efficiency and effectiveness in multiple focus areas, Bekaert needed a modern data platform capable of managing large volumes of data and generating actionable insights. The company aimed to drive quality, overall equipment effectiveness (OEE), and plant productivity based on these insights.
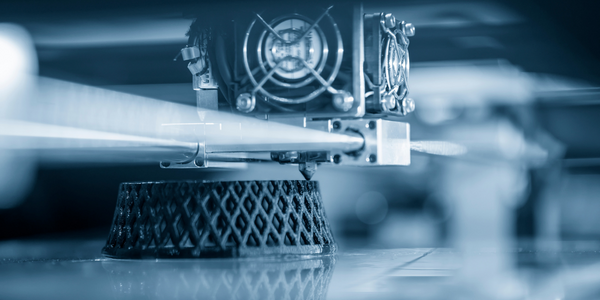
Case Study
3D-Printing of Tooling Parts
Selective Laser Melting (SLM), an additive manufacturing technology, can be used for the production of tooling components with conformal cooling channels. ABB OY, Drives and Controls, was able to tremendously reduce the cycle time for a cabling grommet due to a redesign and optimization of a tooling insert. The optimized geometry of the part not only reduces the cycle time but also leads to less scrap parts in production.The aim of the case study of implementing conformal cooling for this insert was to improve the efficiency of the production and to increase the product quality resulting in less defective products.