Download PDF
Bental Motion Systems: Enhancing Design Efficiency with Altair Solutions
Technology Category
- Sensors - Infrared Sensors
- Sensors - Thermal Conductivity Sensors
Applicable Industries
- Aerospace
- Semiconductors
Applicable Functions
- Product Research & Development
- Quality Assurance
Use Cases
- Virtual Prototyping & Product Testing
Services
- System Integration
- Testing & Certification
The Challenge
Bental Motion Systems, a member of the Gevasol Group, has been designing and manufacturing advanced power and motion systems for demanding industries such as defense, aerospace, and semiconductors since 1983. The company produces a variety of end applications including motors, alternators, and electrical brakes. To meet increasing demands, Bental continues to advance its in-house capabilities in development, analysis and design, testing, and quality assurance. However, the company faced a challenge in accelerating the design of electric machines while reacting quickly to customer-specific requirements. The R&D team needed to extend its usage of the Altair software suite to cover more physics and gain flexibility in their approach depending on the project phase.
About The Customer
Bental Motion Systems is a member of the Gevasol Group and has been in operation since 1983. The company specializes in designing and manufacturing advanced power and motion systems for demanding industries such as defense, aerospace, and semiconductors. Bental produces a variety of end applications including motors, alternators, and electrical brakes. The company is committed to meeting increasing demands by continually advancing its in-house capabilities in development, analysis and design, testing, and quality assurance. The R&D group, led by three post-graduate PhD designers, enables quick response and turnaround.
The Solution
Bental Motion Systems adopted Altair's suite of software solutions to address their design challenges. Altair FluxMotor™ was used for motor pre-design, enabling quick concept exploration and accurate feasibility checks. The team also referenced previous designs stored on their company server to gain quick insights and select the most appropriate starting point for a new design. Once feasibility was approved and validated with the customer, the complete FluxMotor project was exported to Flux2D for detailed electromagnetics design and thermal simulations. For more specific analysis, Flux 3D was used to check the machine's magnetic field surrounding, predict the winding head temperature, and perform axial direction analysis. Altair Inspire™ supported the team when a more global approach was required, and Altair AcuSolve™ was used for advanced thermal analysis. The increasing use of Altair HyperStudy™ for data exploration and multiphysics optimization showed promising possibilities for innovation and performance optimization.
Operational Impact
Quantitative Benefit
Related Case Studies.
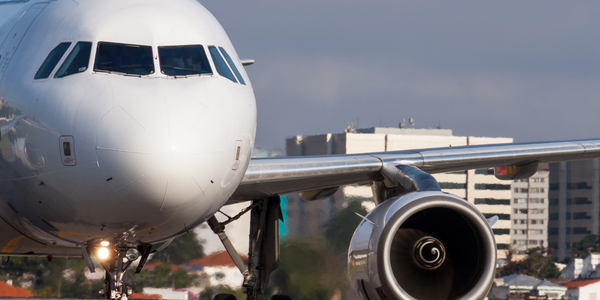
Case Study
Airbus Soars with Wearable Technology
Building an Airbus aircraft involves complex manufacturing processes consisting of thousands of moving parts. Speed and accuracy are critical to business and competitive advantage. Improvements in both would have high impact on Airbus’ bottom line. Airbus wanted to help operators reduce the complexity of assembling cabin seats and decrease the time required to complete this task.
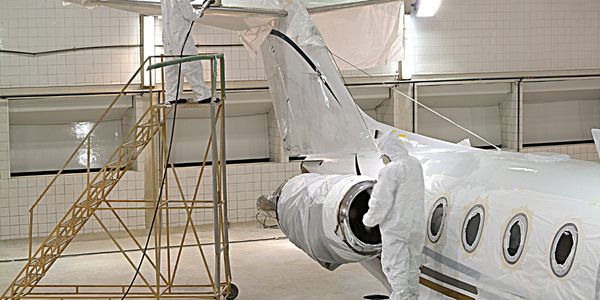
Case Study
Aircraft Predictive Maintenance and Workflow Optimization
First, aircraft manufacturer have trouble monitoring the health of aircraft systems with health prognostics and deliver predictive maintenance insights. Second, aircraft manufacturer wants a solution that can provide an in-context advisory and align job assignments to match technician experience and expertise.
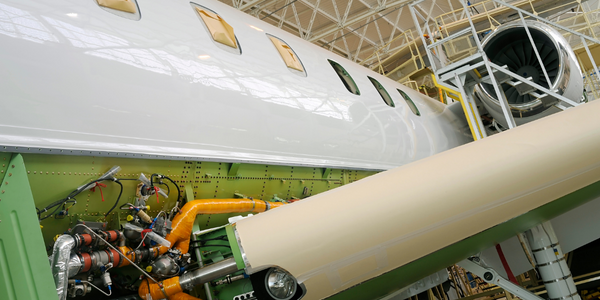
Case Study
Aerospace & Defense Case Study Airbus
For the development of its new wide-body aircraft, Airbus needed to ensure quality and consistency across all internal and external stakeholders. Airbus had many challenges including a very aggressive development schedule and the need to ramp up production quickly to satisfy their delivery commitments. The lack of communication extended design time and introduced errors that drove up costs.
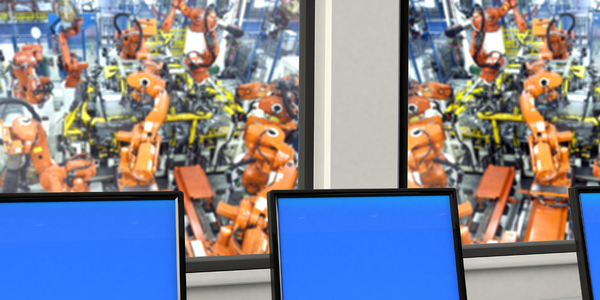
Case Study
KINESYS Semiconductor Factory Automation Software
KINESYS Software provides both Integrated Device Manufacturer (IDM) and Original Equipment Manufacturer (OEM) customers world-class software products and solutions for advanced wafer and device traceability and process management. KINESYS offers state of the art database technology with a core focus on SEMI standards. KINESYS’ challenge was to make back-end processing failure-free and easy to use for clients while supporting licensing models more adaptable to changing industry needs.
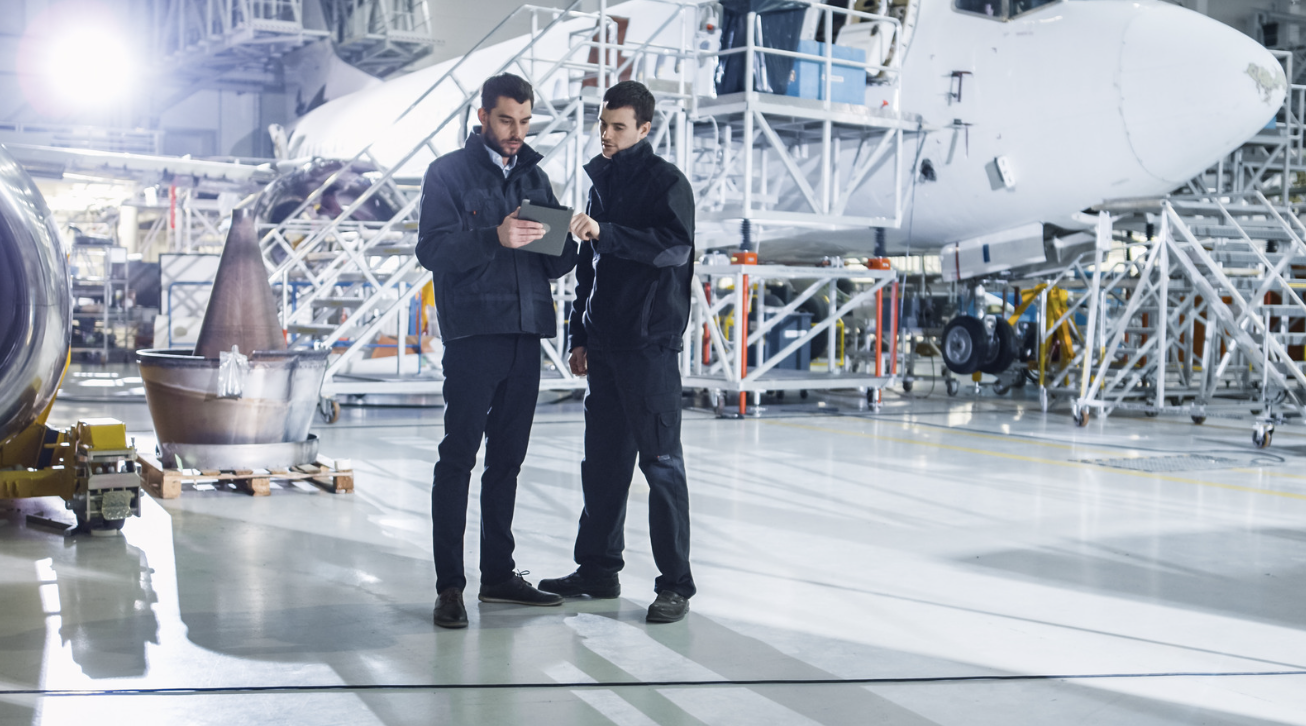
Case Study
Developing Smart Tools for the Airbus Factory
Manufacturing and assembly of aircraft, which involves tens of thousands of steps that must be followed by the operators, and a single mistake in the process could cost hundreds of thousands of dollars to fix, makes the room for error very small.