Download PDF
Blue River Solves Analysis Paralysis with Spotfire
Technology Category
- Analytics & Modeling - Predictive Analytics
- Analytics & Modeling - Machine Learning
- Application Infrastructure & Middleware - Data Visualization
Applicable Industries
- Oil & Gas
Applicable Functions
- Business Operation
- Quality Assurance
Use Cases
- Predictive Maintenance
- Process Control & Optimization
Services
- Training
- Data Science Services
- System Integration
The Challenge
The oil and gas industry faces significant challenges in maximizing the use of analytics tools like TIBCO Spotfire. Companies need to increase production and reduce costs while dealing with competitive pressures and commodity price fluctuations. Inefficient workflows and the use of multiple tools can hinder decision-making and lead to falling behind competitors. Standardizing on a single, powerful tool like Spotfire can help companies become more efficient and make better decisions.
About The Customer
Blue River Analytics is a company that specializes in helping upstream oil and gas production companies gain a competitive advantage through advanced visual and predictive analytic tools. The company collaborates with customers to understand their data assets, training needs, and the most effective ways to use TIBCO Spotfire. Blue River's experts work to transform a wide array of data into interactive applications that save time, reduce costs, and increase productivity. The company was founded by former TIBCO employees who saw the potential of Spotfire and decided to create a business around it.
The Solution
Blue River Analytics started its relationship with TIBCO several years ago, with the founders being former TIBCO employees. They saw a need to extend the capabilities of Spotfire for specific uses in the oil and gas industry. Blue River offers three main services: training, templates for common business use cases, and advanced data science techniques. The company aims to enable a broad spectrum of Spotfire users, from beginners to advanced data scientists. Blue River's industry background and expertise help customers improve their business by leveraging Spotfire's capabilities. The platform's integration with the R programming language provides advanced statistical computing and modeling, enhancing the overall analytics experience.
Operational Impact
Quantitative Benefit
Related Case Studies.
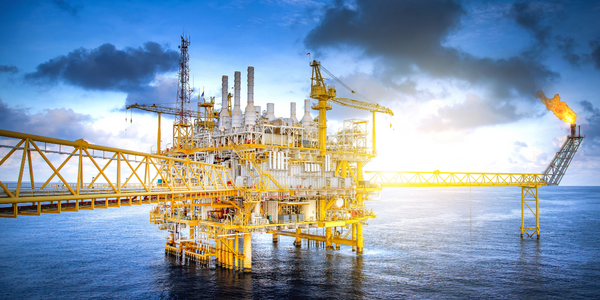
Case Study
Taking Oil and Gas Exploration to the Next Level
DownUnder GeoSolutions (DUG) wanted to increase computing performance by 5 to 10 times to improve seismic processing. The solution must build on current architecture software investments without sacrificing existing software and scale computing without scaling IT infrastructure costs.
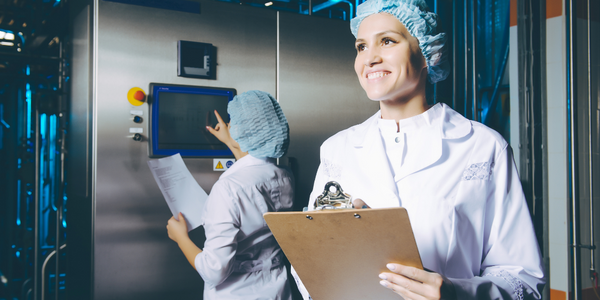
Case Study
Remote Wellhead Monitoring
Each wellhead was equipped with various sensors and meters that needed to be monitored and controlled from a central HMI, often miles away from the assets in the field. Redundant solar and wind generators were installed at each wellhead to support the electrical needs of the pumpstations, temperature meters, cameras, and cellular modules. In addition to asset management and remote control capabilities, data logging for remote surveillance and alarm notifications was a key demand from the customer. Terra Ferma’s solution needed to be power efficient, reliable, and capable of supporting high-bandwidth data-feeds. They needed a multi-link cellular connection to a central server that sustained reliable and redundant monitoring and control of flow meters, temperature sensors, power supply, and event-logging; including video and image files. This open-standard network needed to interface with the existing SCADA and proprietary network management software.
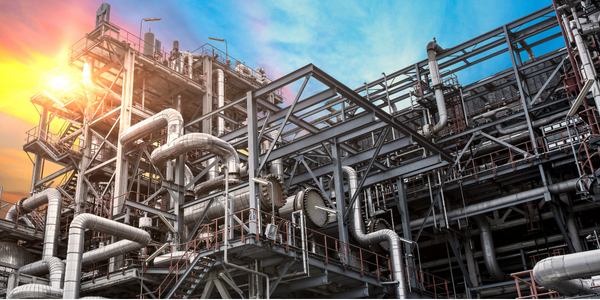
Case Study
Refinery Saves Over $700,000 with Smart Wireless
One of the largest petroleum refineries in the world is equipped to refine various types of crude oil and manufacture various grades of fuel from motor gasoline to Aviation Turbine Fuel. Due to wear and tear, eight hydrogen valves in each refinery were leaking, and each cost $1800 per ton of hydrogen vented. The plant also had leakage on nearly 30 flare control hydrocarbon valves. The refinery wanted a continuous, online monitoring system that could catch leaks early, minimize hydrogen and hydrocarbon production losses, and improve safety for maintenance.