Download PDF
CM Group Drives Virtual Onboarding and Consistent Messaging with Mindtickle
Technology Category
- Platform as a Service (PaaS) - Application Development Platforms
Applicable Functions
- Human Resources
- Business Operation
Use Cases
- Remote Collaboration
- Remote Control
Services
- Software Design & Engineering Services
- System Integration
The Challenge
When the COVID-19 pandemic hit, CM Group’s entire company shifted to working remotely. This meant they were faced with a challenge they hadn’t experienced before: finding ways to onboard new hires virtually. On top of this, CM Group still had to train and motivate their existing employee base remotely. They had access to multiple enablement platforms but were struggling to streamline them into one consistent process. CM Group’s global enablement team needed to bring all of their brands into one unified readiness platform that all of their employees could use. Two of their brands were already using Lessonly, while another used Mindtickle. When the COVID-19 pandemic began, the quarantine accelerated CM Group’s need to implement Mindtickle for its entire workforce across the globe.
About The Customer
CM Group is a company based in Nashville, Tennessee. Founded in 2017, the company operates in the Information Technology and Services industry. The company has over 700 employees globally. CM Group’s global enablement team needed to bring all of their brands into one unified readiness platform that all of their employees could use. Two of their brands were already using Lessonly, while another used Mindtickle. When the COVID-19 pandemic began, the quarantine accelerated CM Group’s need to implement Mindtickle for its entire workforce across the globe.
The Solution
With a pressing need to roll out onboarding and training programs remotely throughout the pandemic, CM Group’s enablement team opted to consolidate their enablement platforms to create the CM Group Knowledge Hub. The Knowledge Hub acts as a collaborative onboarding experience for new hires, while also serving as a source for regular updates for seasoned team members. By implementing new strategies like Missions using Mindtickle, CM Group is able to ensure their entire customer-facing team is trained on consistent messaging and processes. Transitioning to Mindtickle, they created one learning site called the CM Group Knowledge Hub and quickly moved their existing enablement content over to their new readiness platform. Mindtickle’s single sign-on capability made it as simple as clicking a button for employees to get started.
Operational Impact
Quantitative Benefit
Related Case Studies.
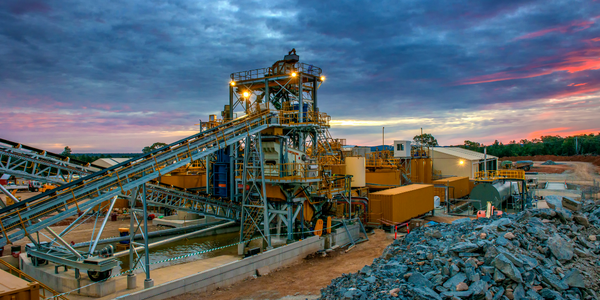
Case Study
Goldcorp: Internet of Things Enables the Mine of the Future
Goldcorp is committed to responsible mining practices and maintaining maximum safety for its workers. At the same time, the firm is constantly exploring ways to improve the efficiency of its operations, extend the life of its assets, and control costs. Goldcorp needed technology that can maximize production efficiency by tracking all mining operations, keep employees safe with remote operations and monitoring of hazardous work areas and control production costs through better asset and site management.
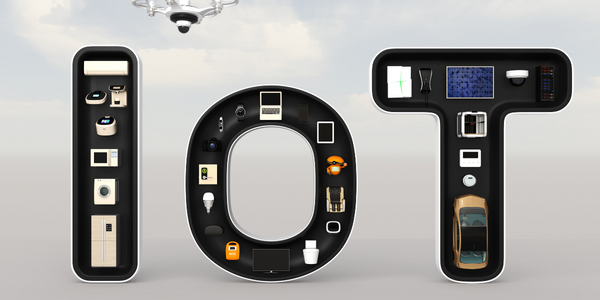
Case Study
Premium Appliance Producer Innovates with Internet of Everything
Sub-Zero faced the largest product launch in the company’s history:It wanted to launch 60 new products as scheduled while simultaneously opening a new “greenfield” production facility, yet still adhering to stringent quality requirements and manage issues from new supply-chain partners. A the same time, it wanted to increase staff productivity time and collaboration while reducing travel and costs.
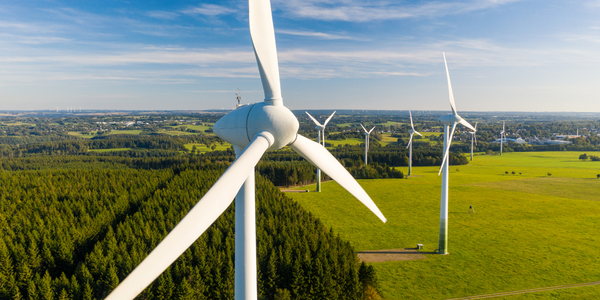
Case Study
Remote Monitoring and Control for a Windmill Generator
As concerns over global warming continue to grow, green technologies are becoming increasingly popular. Wind turbine companies provide an excellent alternative to burning fossil fuels by harnessing kinetic energy from the wind and converting it into electricity. A typical wind farm may include over 80 wind turbines so efficient and reliable networks to manage and control these installations are imperative. Each wind turbine includes a generator and a variety of serial components such as a water cooler, high voltage transformer, ultrasonic wind sensors, yaw gear, blade bearing, pitch cylinder, and hub controller. All of these components are controlled by a PLC and communicate with the ground host. Due to the total integration of these devices into an Ethernet network, one of our customers in the wind turbine industry needed a serial-to-Ethernet solution that can operate reliably for years without interruption.
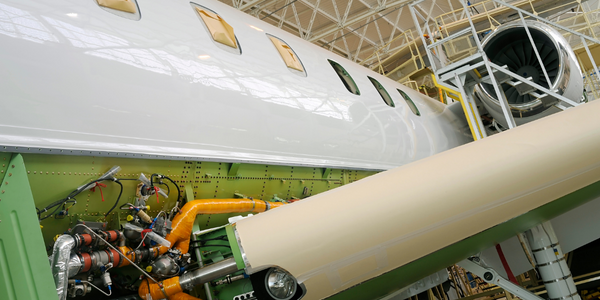
Case Study
Aerospace & Defense Case Study Airbus
For the development of its new wide-body aircraft, Airbus needed to ensure quality and consistency across all internal and external stakeholders. Airbus had many challenges including a very aggressive development schedule and the need to ramp up production quickly to satisfy their delivery commitments. The lack of communication extended design time and introduced errors that drove up costs.
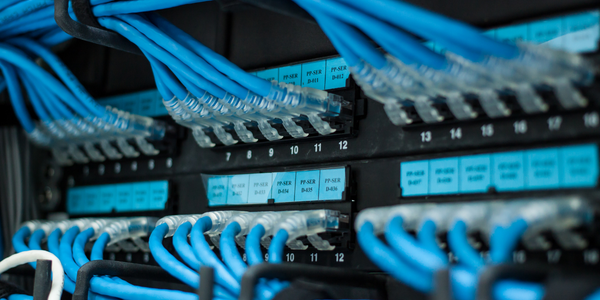
Case Study
Using SNMP for a Ethernet-Based Home Automation System
A startup company was developing a product which provides service partners with an integrated e-services platform that allows customers to remotely monitor and control devices in their home or business. In order to complete their project, the startup needed a control system that could monitor and control the many different devices used by their potential customers, preferably with an open protocol for greater flexibility. SNMP was their first choice, as it is commonly used and well understood in the IT field. The next step was to choose an I/O server to connect to the sensors in a home automation system. System Requirements - Open Ethernet-based procotol - SNMP protocol for I/O control - Compact size to save space - Long-term support and services
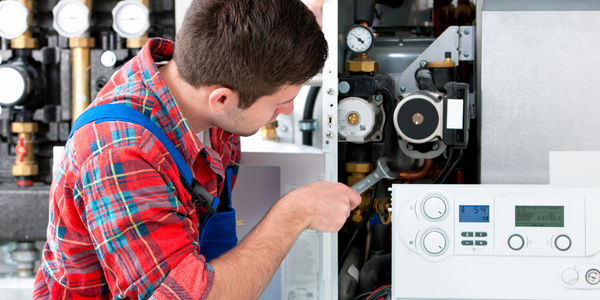
Case Study
Boiler Control System for Plastic Manufacturing Applications
Factory automation applications must be equipped to handle and monitor the myriads of information from attached devices. For plastic manufacturing applications, the boiler control system plays a critical role by gathering and regulating information to ensure production is accurate and smooth. In this particular case, the customer combines eight subsystems that include power meters, water meters, alarm output, displays, and I/O status to be controlled by several intelligent controllers with Modbus RTU interface. The Modbus TCP protocol is used for this application due to the distance. System Requirements: • Modbus serial to Modbus TCP translation • Multiple slaves/masters support • Automatic Modbus TCP response time detection