Download PDF
Cooking Up Success
Technology Category
- Functional Applications - Warehouse Management Systems (WMS)
Applicable Industries
- Food & Beverage
- Retail
Applicable Functions
- Logistics & Transportation
- Warehouse & Inventory Management
Use Cases
- Inventory Management
- Warehouse Automation
Services
- Cloud Planning, Design & Implementation Services
- System Integration
The Challenge
Gousto, a London-based recipe box service, was facing a significant challenge due to its exponential growth in consumer demand and increasing product offerings. The company buys products like rice and potatoes in bulk, then these are broken down into smaller quantities. These ingredients support the assembly of 40 different weekly recipes. As specific work orders are created, about 60 unique SKUs are assembled into each individual box, which is then shipped to the consumer. Because many ingredients are perishable, or have special handling needs, time is always of the essence. The company's volume has grown considerably since 2012, increasing their warehouse logistics challenges significantly. The global market for meal kits is projected to reach $10 billion in sales by 2020, indicating that Gousto's growth is expected to continue.
About The Customer
Founded in 2012 as a start-up company, today Gousto — a London-based recipe box service — serves nearly 2 million meals a month. Based on its ingredients and service, the business has been voted the UK’s best recipe kit service by the Independent, BBC Good Food, The Guardian, The Metro, and Time Out London. One of the key challenges for this business is the sheer size and scope of its warehouse logistics. Gousto buys products like rice and potatoes in bulk, then these are broken down into smaller quantities. These ingredients support the assembly of 40 different weekly recipes. As specific work orders are created, about 60 unique SKUs are assembled into each individual box, which is then shipped to the consumer.
The Solution
In 2016, Gousto partnered with Socius24, JDA’s UK-based reseller partner, on an implementation of JDA Dispatcher Warehouse Management System (WMS). The software is designed to manage sophisticated logistics challenges via increased visibility and automation. JDA Dispatcher WMS is the master system throughout Gousto’s warehouse, interfacing with the company’s ERP system and pick-by-light-conveyor system running on a third-party cloud provider. The company also relies on a Socius24-developed User Service Portal to help with specialized tasks like converting bulk food quantities to smaller SKUs. Currently, Socius24 is partnering with Gousto to add a second automated picking line supported by JDA Dispatcher WMS.
Operational Impact
Quantitative Benefit
Related Case Studies.
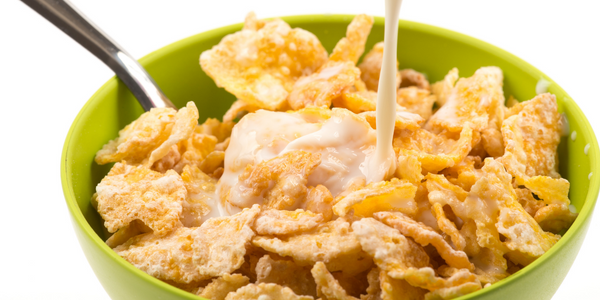
Case Study
The Kellogg Company
Kellogg keeps a close eye on its trade spend, analyzing large volumes of data and running complex simulations to predict which promotional activities will be the most effective. Kellogg needed to decrease the trade spend but its traditional relational database on premises could not keep up with the pace of demand.
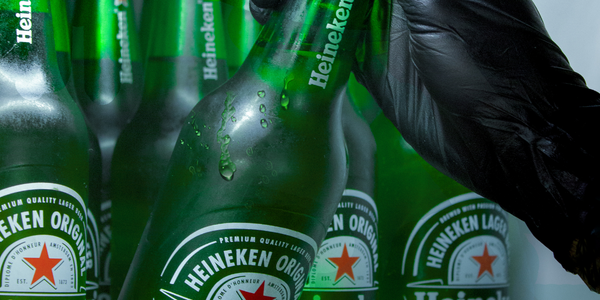
Case Study
HEINEKEN Uses the Cloud to Reach 10.5 Million Consumers
For 2012 campaign, the Bond promotion, it planned to launch the campaign at the same time everywhere on the planet. That created unprecedented challenges for HEINEKEN—nowhere more so than in its technology operation. The primary digital content for the campaign was a 100-megabyte movie that had to play flawlessly for millions of viewers worldwide. After all, Bond never fails. No one was going to tolerate a technology failure that might bruise his brand.Previously, HEINEKEN had supported digital media at its outsourced datacenter. But that datacenter lacked the computing resources HEINEKEN needed, and building them—especially to support peak traffic that would total millions of simultaneous hits—would have been both time-consuming and expensive. Nor would it have provided the geographic reach that HEINEKEN needed to minimize latency worldwide.
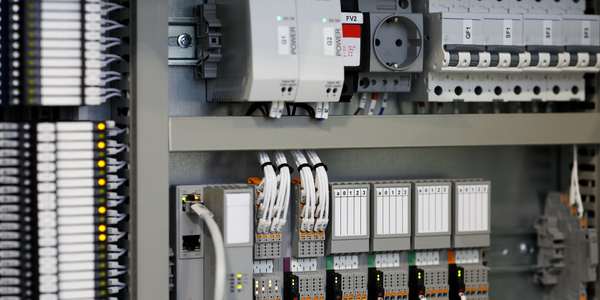
Case Study
Improving Production Line Efficiency with Ethernet Micro RTU Controller
Moxa was asked to provide a connectivity solution for one of the world's leading cosmetics companies. This multinational corporation, with retail presence in 130 countries, 23 global braches, and over 66,000 employees, sought to improve the efficiency of their production process by migrating from manual monitoring to an automatic productivity monitoring system. The production line was being monitored by ABB Real-TPI, a factory information system that offers data collection and analysis to improve plant efficiency. Due to software limitations, the customer needed an OPC server and a corresponding I/O solution to collect data from additional sensor devices for the Real-TPI system. The goal is to enable the factory information system to more thoroughly collect data from every corner of the production line. This will improve its ability to measure Overall Equipment Effectiveness (OEE) and translate into increased production efficiencies. System Requirements • Instant status updates while still consuming minimal bandwidth to relieve strain on limited factory networks • Interoperable with ABB Real-TPI • Small form factor appropriate for deployment where space is scarce • Remote software management and configuration to simplify operations
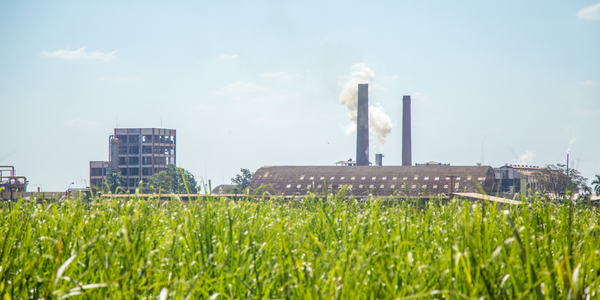
Case Study
Energy Management System at Sugar Industry
The company wanted to use the information from the system to claim under the renewable energy certificate scheme. The benefit to the company under the renewable energy certificates is Rs 75 million a year. To enable the above, an end-to-end solution for load monitoring, consumption monitoring, online data monitoring, automatic meter data acquisition which can be exported to SAP and other applications is required.
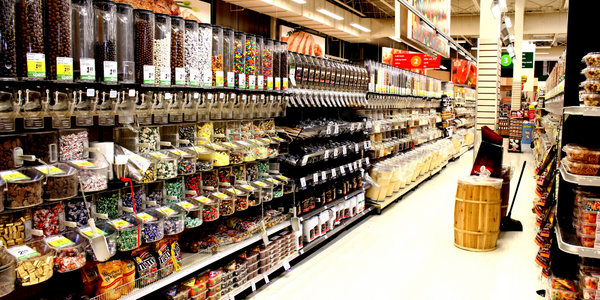
Case Study
How Sirqul’s IoT Platform is Crafting Carrefour’s New In-Store Experiences
Carrefour Taiwan’s goal is to be completely digital by end of 2018. Out-dated manual methods for analysis and assumptions limited Carrefour’s ability to change the customer experience and were void of real-time decision-making capabilities. Rather than relying solely on sales data, assumptions, and disparate systems, Carrefour Taiwan’s CEO led an initiative to find a connected IoT solution that could give the team the ability to make real-time changes and more informed decisions. Prior to implementing, Carrefour struggled to address their conversion rates and did not have the proper insights into the customer decision-making process nor how to make an immediate impact without losing customer confidence.