Download PDF
Exploring the Potential of Topology Optimization and Additive Manufacturing in Architecture
Technology Category
- Infrastructure as a Service (IaaS) - Cloud Computing
Applicable Industries
- Buildings
- Education
Applicable Functions
- Logistics & Transportation
- Product Research & Development
Use Cases
- Additive Manufacturing
- Rapid Prototyping
The Challenge
The case study revolves around the exploration of the potential benefits of combining topology optimization and additive manufacturing in architectural projects. While this combination is common in industries like automotive or aerospace, it is rarely used in architecture. The challenge was to investigate the potential of this symbiosis for architectural projects. Bayu Prayudhi, an architectural student of the University of Delft, took up this challenge and re-designed an existing architectural project, the outdoor canopy at Baku international airport in Azerbaijan, originally designed by ARUP. The goal was to include topology optimization upfront in the design process and adapt the design for 3D printing. The challenge also involved dealing with boundary conditions such as costs, lead times, and technological limits while striving to combine function, shape, and innovation.
About The Customer
The customer in this case study is Bayu Prayudhi, an architectural student at the University of Delft. He undertook the project to investigate the potential of the symbiosis of topology optimization and additive manufacturing for architectural projects. He chose an existing project, an outdoor canopy, designed by ARUP, located at Baku international airport in Azerbaijan for his study. Bayu was supported and supervised by his mentor, Dr. Michela Turrin and Prof. Dr. Ing. U. Knaack, from the department of Architectural Engineering and Technology at TU Delft and Shibo Ren, a Senior Structural Engineer, Buildings Amsterdam at ARUP. The Faculty of Architecture and the Built Environment of TU Delft, where Bayu is studying, has a leading role in architecture education and research in the broadest sense.
The Solution
The solution involved the use of Altair's HyperWorks suite, especially OptiStruct for optimization tasks. The geometry was imported into HyperWorks and the occurring load cases were applied. Manufacturing constraints arising in additive manufacturing, such as supporting structures and printing direction, were then applied. The design space was defined and the optimization was performed on one node, using the numerical data of different occurring forces. The results were then extrapolated to estimate the impact an overall structural optimization might have. Since no 3D model of the original project was available, the design of the original structure had to be remodeled relying on approximation and assumptions. The total weight of all nodes was averaged. The new 3D printed design led to a potential weight reduction of approximately 32 percent. The use of OptiStruct helped to create a functional and visually captivating design ready for additive manufacturing.
Operational Impact
Quantitative Benefit
Related Case Studies.
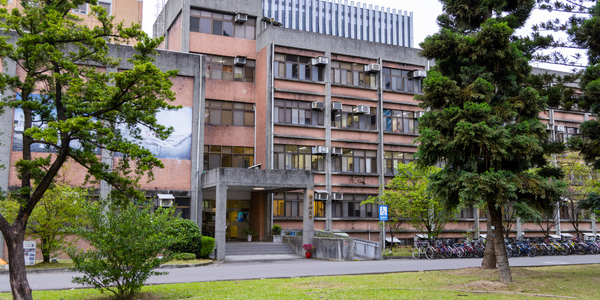
Case Study
Energy Saving & Power Monitoring System
Recently a university in Taiwan was experiencing dramatic power usage increases due to its growing number of campus buildings and students. Aiming to analyze their power consumption and increase their power efficiency across 52 buildings, the university wanted to build a power management system utilizing web-based hardware and software. With these goals in mind, they contacted Advantech to help them develop their system and provide them with the means to save energy in the years to come.
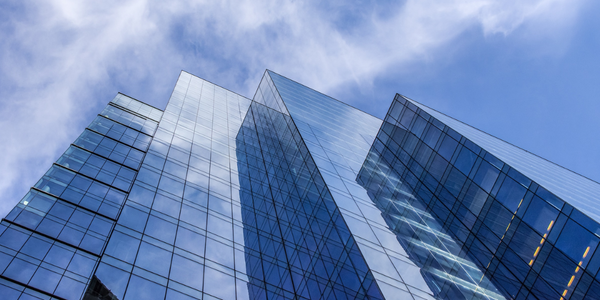
Case Study
Intelligent Building Automation System and Energy Saving Solution
One of the most difficult problems facing the world is conserving energy in buildings. However, it is not easy to have a cost-effective solution to reduce energy usage in a building. One solution for saving energy is to implement an intelligent building automation system (BAS) which can be controlled according to its schedule. In Indonesia a large university with a five floor building and 22 classrooms wanted to save the amount of energy being used.
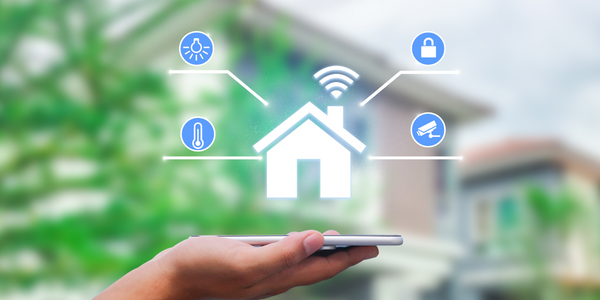
Case Study
Powering Smart Home Automation solutions with IoT for Energy conservation
Many industry leaders that offer Smart Energy Management products & solutions face challenges including:How to build a scalable platform that can automatically scale-up to on-board ‘n’ number of Smart home devicesData security, solution availability, and reliability are the other critical factors to deal withHow to create a robust common IoT platform that handles any kind of smart devicesHow to enable data management capabilities that would help in intelligent decision-making
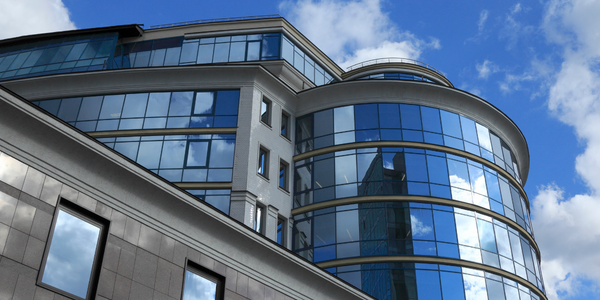
Case Study
Commercial Building Automation Boosts Energy Efficiency
One of the challenges to building automation is the multitude of non-interoperable communications protocols that have evolved over the years. Buildings have several islands of automation. Bridging the islands of different automation without losing the considerable investment in each specialized control network is the main focus in this solution.

Case Study
Protecting a Stadium from Hazardous Materials Using IoT2cell's Mobility Platform
There was a need for higher security at the AT&T Stadium during the NFL draft. There was a need to ensure that nuclear radiation material was not smuggled inside the stadium. Hazmat materials could often be missed in a standard checkpoint when gaining entry into a stadium.