Download PDF
General Dynamics’ Journey to Paperless
Technology Category
- Functional Applications - Manufacturing Execution Systems (MES)
- Analytics & Modeling - Real Time Analytics
Applicable Industries
- Aerospace
Applicable Functions
- Quality Assurance
Use Cases
- Manufacturing System Automation
- Digital Thread
- Process Control & Optimization
Services
- System Integration
- Training
- Software Design & Engineering Services
The Challenge
General Dynamics AIS Integrated Space Systems faced the challenge of transitioning from a highly paper-based and manually controlled manufacturing process to a digital, paperless environment. The complexity and criticality of their work, which involves producing high-reliability space hardware, required a comprehensive system to control workflow, provide checkpoints, and house detailed data. The existing process was labor-intensive, with information and data distributed across multiple locations and numerous manual checkpoints. This setup was not only inefficient but also prone to errors, which could compromise the integrity of the hardware costing tens of millions of dollars per unit. The need for a streamlined, integrated system became evident to ensure superior control of product workflow, engineering change incorporation, and to support continuous improvement efforts.
About The Customer
General Dynamics AIS Integrated Space Systems, located in Scottsdale, Arizona, has been a key player in delivering critical communications products to space programs for over 40 years. Their contributions include hardware for missions such as Explorer, Voyager, Space Station, Orion, NATO Satellites, Mars Pathfinder, and Mars Rover. The company boasts an impressive track record with no mission failures associated with their hardware. Their in-house manufacturing capabilities span from microelectronics to end-item system integration of digital and RF hardware. The Scottsdale facility specializes in producing microelectronics, printed circuit boards, and assemblies used in satellites. The company’s mission is to provide smarter mission-critical systems and products to defense, civil government, intelligence, and cybersecurity customers, with a vision of creating a safer world through smarter platforms and missions.
The Solution
To address the challenges, General Dynamics AIS implemented iBASEt’s Solumina MES/QMS system. This system became the focal point for building hardware, providing a comprehensive solution to control workflow, prevent unauthorized work, and house detailed data. The transition to a paperless shop floor was a significant milestone, achieved through the dedication of the management and execution team. The Solumina system enabled the collection and extraction of all production-related data, superior control of product workflow, and the incorporation of engineering changes. It also provided data and metrics to support Lean, Six Sigma, and Kaizen efforts. The system’s automated quality metrics eliminated the need for dedicated personnel to generate reports, and the standardized process and data integrity were noted as best-in-class by customers like Boeing, Lockheed Martin, and NASA. Training on the MES/Quality system was streamlined, reducing the learning curve for new personnel and ensuring consistency across projects.
Operational Impact
Quantitative Benefit
Related Case Studies.
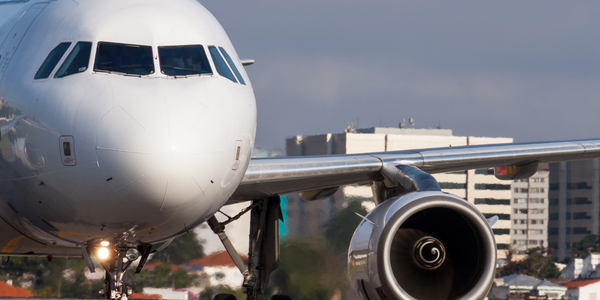
Case Study
Airbus Soars with Wearable Technology
Building an Airbus aircraft involves complex manufacturing processes consisting of thousands of moving parts. Speed and accuracy are critical to business and competitive advantage. Improvements in both would have high impact on Airbus’ bottom line. Airbus wanted to help operators reduce the complexity of assembling cabin seats and decrease the time required to complete this task.
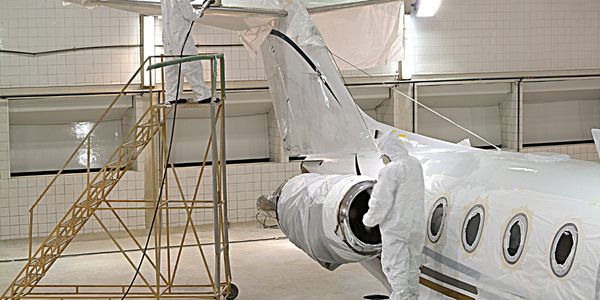
Case Study
Aircraft Predictive Maintenance and Workflow Optimization
First, aircraft manufacturer have trouble monitoring the health of aircraft systems with health prognostics and deliver predictive maintenance insights. Second, aircraft manufacturer wants a solution that can provide an in-context advisory and align job assignments to match technician experience and expertise.
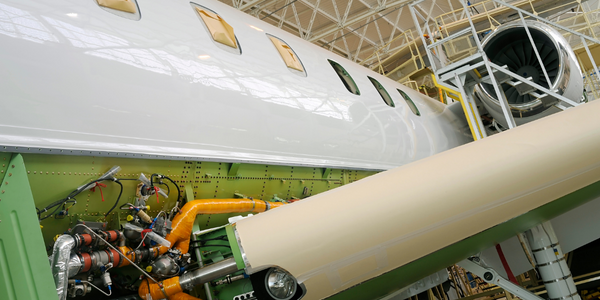
Case Study
Aerospace & Defense Case Study Airbus
For the development of its new wide-body aircraft, Airbus needed to ensure quality and consistency across all internal and external stakeholders. Airbus had many challenges including a very aggressive development schedule and the need to ramp up production quickly to satisfy their delivery commitments. The lack of communication extended design time and introduced errors that drove up costs.
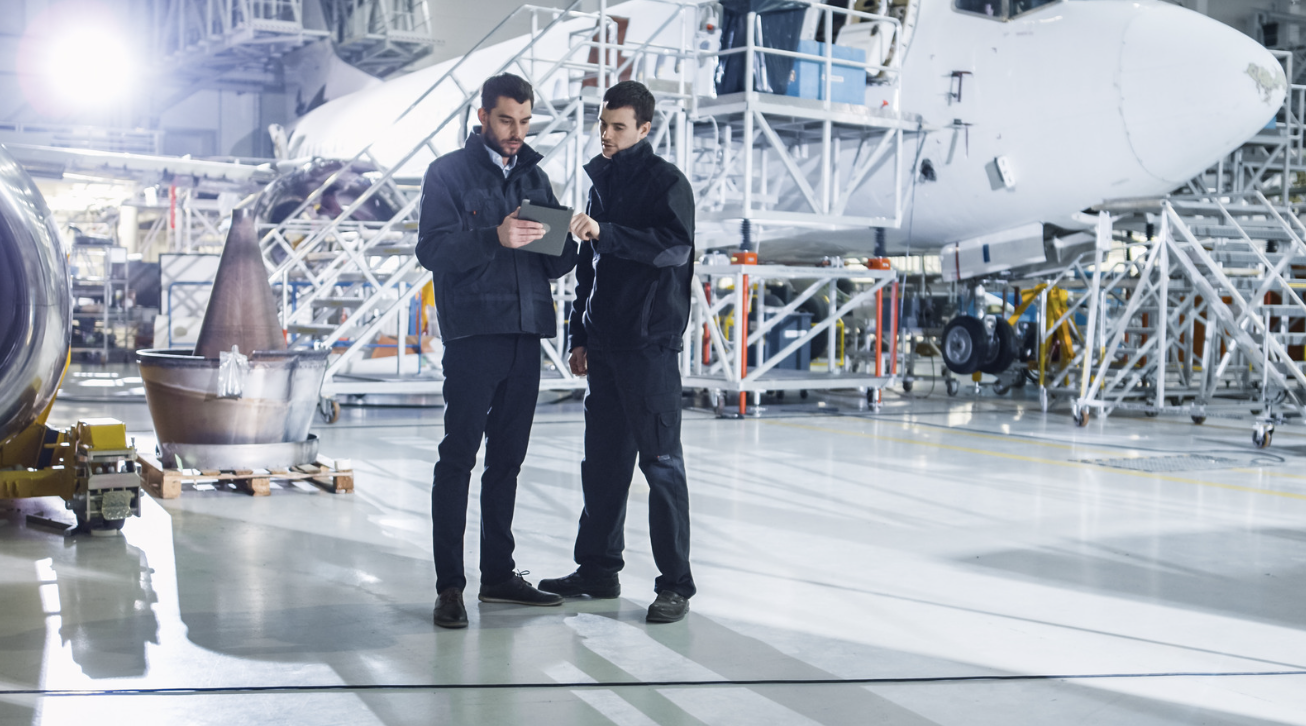
Case Study
Developing Smart Tools for the Airbus Factory
Manufacturing and assembly of aircraft, which involves tens of thousands of steps that must be followed by the operators, and a single mistake in the process could cost hundreds of thousands of dollars to fix, makes the room for error very small.
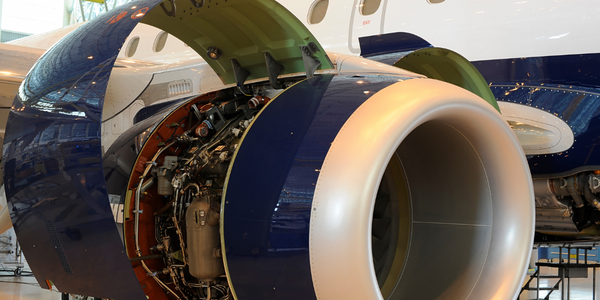
Case Study
Accelerate Production for Spirit AeroSystems
The manufacture and assembly of massive fuselage assemblies and other large structures generates a river of data. In fact, the bill of materials for a single fuselage alone can be millions of rows of data. In-house production processes and testing, as well as other manufacturers and customers created data flows that overwhelmed previous processes and information systems. Spirit’s customer base had grown substantially since their 2005 divestiture from Boeing, resulting in a $41 billion backlog of orders to fill. To address this backlog, meet increased customer demands and minimize additional capital investment, the company needed a way to improve throughput in the existing operational footprint. Spirit had a requirement from customers to increase fuselage production by 30%. To accomplish this goal, Spirit needed real-time information on its value chain and workflow. However, the two terabytes of data being pulled from their SAP ECC was unmanageable and overloaded their business warehouse. It had become time-consuming and difficult to pull aggregate data, disaggregate it for the needed information and then reassemble to create a report. During the 6-8 hours it took to build a report, another work shift (they run three per day) would have already taken place, thus the report content was out-of-date before it was ever delivered. As a result, supervisors often had to rely on manual efforts to provide charts, reports and analysis.