Download PDF
Leveraging Digital Manufacturing for a Resilient EV Supply Chain: A Case Study on Eaton
Technology Category
- Analytics & Modeling - Digital Twin / Simulation
- Functional Applications - Manufacturing Execution Systems (MES)
Applicable Industries
- Aerospace
- Automotive
Applicable Functions
- Logistics & Transportation
- Product Research & Development
Use Cases
- Digital Thread
- Digital Twin
Services
- Hardware Design & Engineering Services
- System Integration
The Challenge
Eaton, a premier power management company, was facing challenges in improving time to market and profitability in the highly competitive electric vehicle (EV) market. The traditional manufacturing environment, characterized by siloed departments each with its own database and processes, was hindering timely, accurate, and effective collaboration. This was particularly problematic given the current prevalence of supply chain shortages. The company needed a solution that would allow it to quickly understand the impact of design on the supply chain, identify potential manufacturability issues early in the design process, and innovate faster.
About The Customer
Eaton is a leading power management company with approximately 90,000 employees in 175 different countries. The company, which has a history spanning over a hundred years, started by manufacturing axles. Over the last two decades, Eaton has undergone a dramatic transformation, expanding into sectors such as electrical, aerospace, hydraulics, and vehicle eMobility. In 2020, the company made roughly $18 billion in sales, with the electrical sector accounting for just over $11 billion and the industrial sector, which includes vehicle eMobility, representing just over $6 million.
The Solution
Eaton embraced manufacturing simulation to improve sourcing and build a resilient supply chain. The company adopted aPriori, a cloud-based digital manufacturing tool, which allowed for a single, consistent database accessible by all departments. This created a 'digital thread' between all departments, enabling seamless connection throughout the product development lifecycle. The aPriori system allowed Eaton to examine new product designs from both a design engineering and sourcing perspective, generating data-rich content with minimal user inputs. The system also enabled the company to understand how the geometry of a product would affect manufacturability and cost, generate cost models in just a few minutes, and make instant design and materials changes. Furthermore, aPriori allowed Eaton to compare pricing for their product across multiple regions around the world, helping them identify where they could save the most time, money, and resources.
Operational Impact
Quantitative Benefit
Related Case Studies.
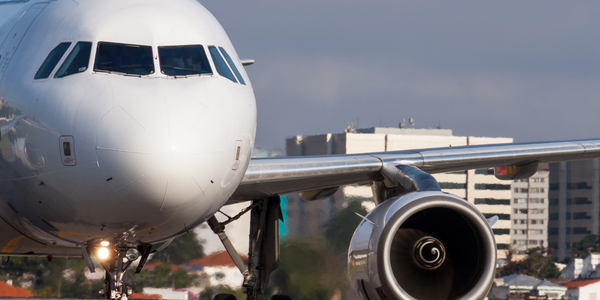
Case Study
Airbus Soars with Wearable Technology
Building an Airbus aircraft involves complex manufacturing processes consisting of thousands of moving parts. Speed and accuracy are critical to business and competitive advantage. Improvements in both would have high impact on Airbus’ bottom line. Airbus wanted to help operators reduce the complexity of assembling cabin seats and decrease the time required to complete this task.
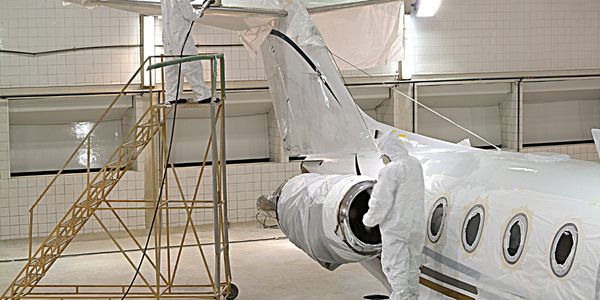
Case Study
Aircraft Predictive Maintenance and Workflow Optimization
First, aircraft manufacturer have trouble monitoring the health of aircraft systems with health prognostics and deliver predictive maintenance insights. Second, aircraft manufacturer wants a solution that can provide an in-context advisory and align job assignments to match technician experience and expertise.
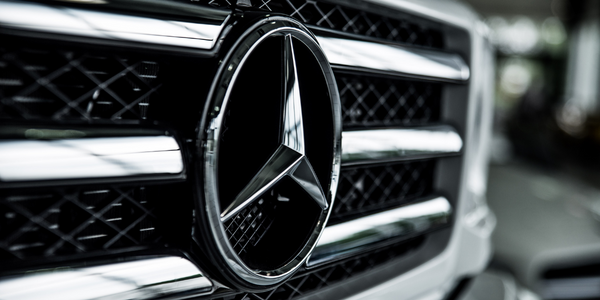
Case Study
Integral Plant Maintenance
Mercedes-Benz and his partner GAZ chose Siemens to be its maintenance partner at a new engine plant in Yaroslavl, Russia. The new plant offers a capacity to manufacture diesel engines for the Russian market, for locally produced Sprinter Classic. In addition to engines for the local market, the Yaroslavl plant will also produce spare parts. Mercedes-Benz Russia and his partner needed a service partner in order to ensure the operation of these lines in a maintenance partnership arrangement. The challenges included coordinating the entire maintenance management operation, in particular inspections, corrective and predictive maintenance activities, and the optimizing spare parts management. Siemens developed a customized maintenance solution that includes all electronic and mechanical maintenance activities (Integral Plant Maintenance).
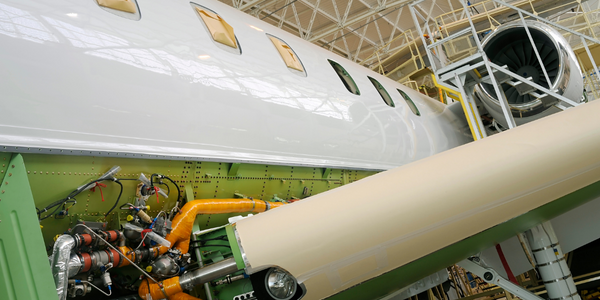
Case Study
Aerospace & Defense Case Study Airbus
For the development of its new wide-body aircraft, Airbus needed to ensure quality and consistency across all internal and external stakeholders. Airbus had many challenges including a very aggressive development schedule and the need to ramp up production quickly to satisfy their delivery commitments. The lack of communication extended design time and introduced errors that drove up costs.