Download PDF
Process Improvement in Stable Bleaching Powder Reactor at Aditya Birla Science and Technology Company
Technology Category
- Sensors - Gas Sensors
- Sensors - Utility Meters
Applicable Industries
- Metals
- Oil & Gas
Applicable Functions
- Logistics & Transportation
- Product Research & Development
Use Cases
- Last Mile Delivery
- Time Sensitive Networking
The Challenge
Aditya Birla Science and Technology Company was facing a significant challenge in their Stable Bleaching Powder (SBP) manufacturing process. The process involved the chlorination of hydrated lime by aerating an SBP solids bed with chlorine gas. However, the company was losing approximately 60 kg/batch of solids, which comprised of products, reactants, and intermediate compounds. These losses were resulting in significant time and cost inefficiencies. The goal was to minimize these losses without making major modifications to the SBP plant. The challenge was to identify process parameters that could be altered to improve the efficiency of the process. However, being a closed-loop system, onsite physical measurements were difficult to carry out.
About The Customer
Aditya Birla Science and Technology Company Private Limited (ABSTCPL) is the corporate research and development centre for the Aditya Birla Group. Located in Taloja, just outside of Mumbai in India, ABSTCPL supports the broad diversity of the Group’s businesses through multidisciplinary teams of expert scientists and engineers who lead fundamental and applied research projects. At ABSTCPL, research and development is based on two strong capabilities. The Process Engineering and Sciences Laboratory focuses on advanced processes and designs, process control and automation, and process engineering platforms and scale-up. The Science and Technology Platforms Laboratory provides expertise in metallurgy, fiber science and textiles, materials and surface sciences, and chemistry.
The Solution
The company decided to use ANSYS CFD to understand the existing issues in the flow patterns. The aerated solids bed was modeled as a porous zone, and impeller rotation was captured using the frozen rotor approach, with the k-ε turbulence model. Simulations helped identify gas channeling and regions where flow velocities exceeded the terminal settling velocity of the average solids particle size. The gas injection nozzle diameters and the number of injection locations were identified as the design parameters. Simulations revealed that increasing the nozzle diameter 2.5 times reduced the outlet-velocity-to-terminal-velocity ratio to 0.57 with 92 percent more uniform flow distribution. Adding two injection locations further reduced the velocity ratio to 0.47, but some flow uniformity was lost.
Operational Impact
Quantitative Benefit
Related Case Studies.
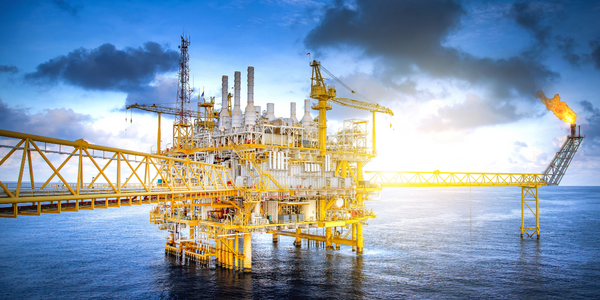
Case Study
Taking Oil and Gas Exploration to the Next Level
DownUnder GeoSolutions (DUG) wanted to increase computing performance by 5 to 10 times to improve seismic processing. The solution must build on current architecture software investments without sacrificing existing software and scale computing without scaling IT infrastructure costs.
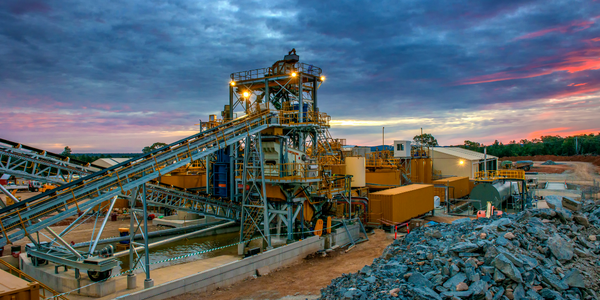
Case Study
Goldcorp: Internet of Things Enables the Mine of the Future
Goldcorp is committed to responsible mining practices and maintaining maximum safety for its workers. At the same time, the firm is constantly exploring ways to improve the efficiency of its operations, extend the life of its assets, and control costs. Goldcorp needed technology that can maximize production efficiency by tracking all mining operations, keep employees safe with remote operations and monitoring of hazardous work areas and control production costs through better asset and site management.
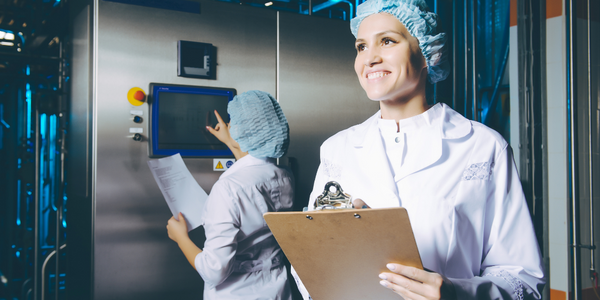
Case Study
Remote Wellhead Monitoring
Each wellhead was equipped with various sensors and meters that needed to be monitored and controlled from a central HMI, often miles away from the assets in the field. Redundant solar and wind generators were installed at each wellhead to support the electrical needs of the pumpstations, temperature meters, cameras, and cellular modules. In addition to asset management and remote control capabilities, data logging for remote surveillance and alarm notifications was a key demand from the customer. Terra Ferma’s solution needed to be power efficient, reliable, and capable of supporting high-bandwidth data-feeds. They needed a multi-link cellular connection to a central server that sustained reliable and redundant monitoring and control of flow meters, temperature sensors, power supply, and event-logging; including video and image files. This open-standard network needed to interface with the existing SCADA and proprietary network management software.
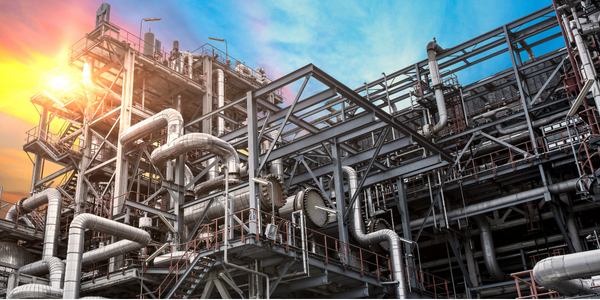
Case Study
Refinery Saves Over $700,000 with Smart Wireless
One of the largest petroleum refineries in the world is equipped to refine various types of crude oil and manufacture various grades of fuel from motor gasoline to Aviation Turbine Fuel. Due to wear and tear, eight hydrogen valves in each refinery were leaking, and each cost $1800 per ton of hydrogen vented. The plant also had leakage on nearly 30 flare control hydrocarbon valves. The refinery wanted a continuous, online monitoring system that could catch leaks early, minimize hydrogen and hydrocarbon production losses, and improve safety for maintenance.
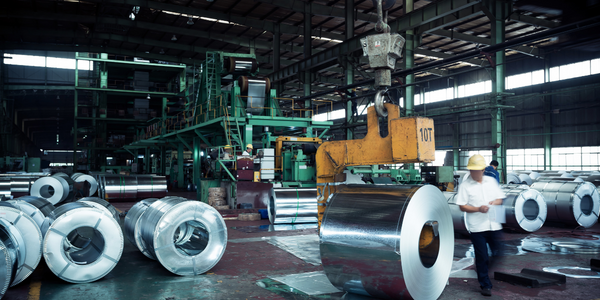
Case Study
KSP Steel Decentralized Control Room
While on-site in Pavlodar, Kazakhstan, the DAQRI team of Business Development and Solutions Architecture personnel worked closely with KSP Steel’s production leadership to understand the steel production process, operational challenges, and worker pain points.