下载PDF
Process Improvement in Stable Bleaching Powder Reactor at Aditya Birla Science and Technology Company
技术
- 传感器 - 气体传感器
- 传感器 - 电表
适用行业
- 金属
- 石油和天然气
适用功能
- 物流运输
- 产品研发
用例
- 最后一英里交付
- 时间敏感网络
挑战
Aditya Birla Science and Technology Company 在稳定漂白粉 (SBP) 制造过程中面临着重大挑战。该工艺涉及通过向 SBP 固体床通入氯气来对熟石灰进行氯化。然而,该公司每批次损失了大约 60 公斤固体,其中包括产品、反应物和中间化合物。这些损失导致了严重的时间和成本效率低下。目标是在不对 SBP 工厂进行重大改造的情况下最大限度地减少这些损失。面临的挑战是确定可以改变的工艺参数以提高工艺效率。然而,作为一个闭环系统,现场物理测量很难进行。
关于客户
Aditya Birla Science and Technology Company Private Limited (ABSTCPL) 是 Aditya Birla 集团的企业研发中心。 ABSTCPL 位于印度孟买郊外的 Taloja,通过由领导基础和应用研究项目的专家科学家和工程师组成的多学科团队支持集团业务的广泛多样性。在 ABSTCPL,研发基于两项强大的能力。过程工程与科学实验室专注于先进工艺和设计、过程控制和自动化以及过程工程平台和放大。科学技术平台实验室提供冶金、纤维科学和纺织、材料和表面科学以及化学方面的专业知识。
解决方案
该公司决定使用 ANSYS CFD 来了解流动模式中存在的问题。曝气固体床被建模为多孔区域,并使用冷冻转子方法和 k-ε 湍流模型捕获叶轮旋转。模拟有助于识别气体通道和流速超过平均固体颗粒尺寸的最终沉降速度的区域。气体注射喷嘴直径和注射位置的数量被确定为设计参数。模拟显示,将喷嘴直径增加 2.5 倍可将出口速度与终端速度之比降低至 0.57,流量分布均匀度提高 92%。添加两个喷射位置进一步将速度比降低至 0.47,但会损失一些流动均匀性。
运营影响
数量效益
相关案例.
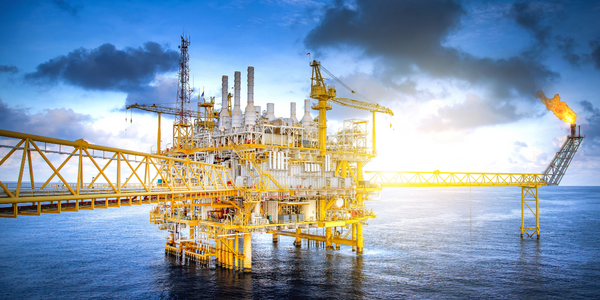
Case Study
Taking Oil and Gas Exploration to the Next Level
DownUnder GeoSolutions (DUG) wanted to increase computing performance by 5 to 10 times to improve seismic processing. The solution must build on current architecture software investments without sacrificing existing software and scale computing without scaling IT infrastructure costs.
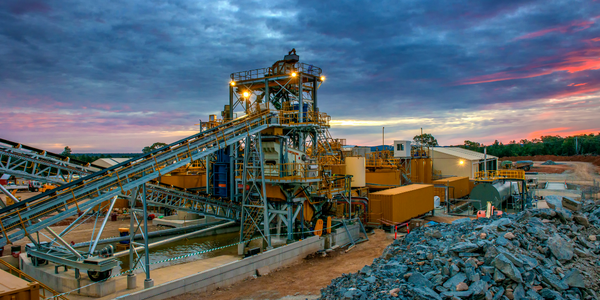
Case Study
Goldcorp: Internet of Things Enables the Mine of the Future
Goldcorp is committed to responsible mining practices and maintaining maximum safety for its workers. At the same time, the firm is constantly exploring ways to improve the efficiency of its operations, extend the life of its assets, and control costs. Goldcorp needed technology that can maximize production efficiency by tracking all mining operations, keep employees safe with remote operations and monitoring of hazardous work areas and control production costs through better asset and site management.
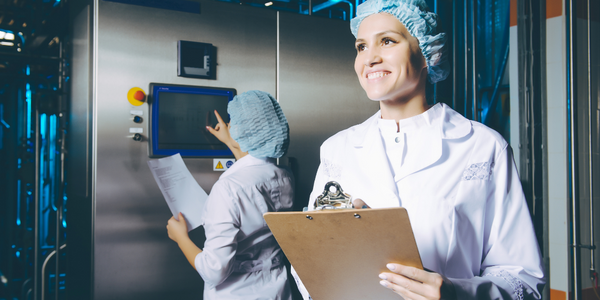
Case Study
Remote Wellhead Monitoring
Each wellhead was equipped with various sensors and meters that needed to be monitored and controlled from a central HMI, often miles away from the assets in the field. Redundant solar and wind generators were installed at each wellhead to support the electrical needs of the pumpstations, temperature meters, cameras, and cellular modules. In addition to asset management and remote control capabilities, data logging for remote surveillance and alarm notifications was a key demand from the customer. Terra Ferma’s solution needed to be power efficient, reliable, and capable of supporting high-bandwidth data-feeds. They needed a multi-link cellular connection to a central server that sustained reliable and redundant monitoring and control of flow meters, temperature sensors, power supply, and event-logging; including video and image files. This open-standard network needed to interface with the existing SCADA and proprietary network management software.
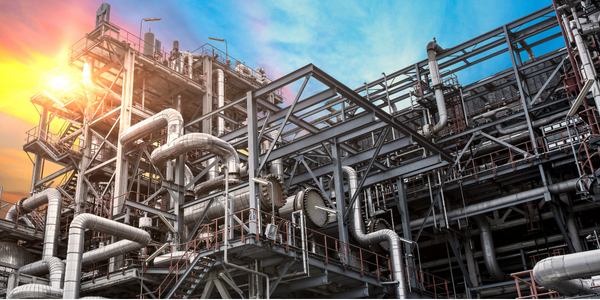
Case Study
Refinery Saves Over $700,000 with Smart Wireless
One of the largest petroleum refineries in the world is equipped to refine various types of crude oil and manufacture various grades of fuel from motor gasoline to Aviation Turbine Fuel. Due to wear and tear, eight hydrogen valves in each refinery were leaking, and each cost $1800 per ton of hydrogen vented. The plant also had leakage on nearly 30 flare control hydrocarbon valves. The refinery wanted a continuous, online monitoring system that could catch leaks early, minimize hydrogen and hydrocarbon production losses, and improve safety for maintenance.
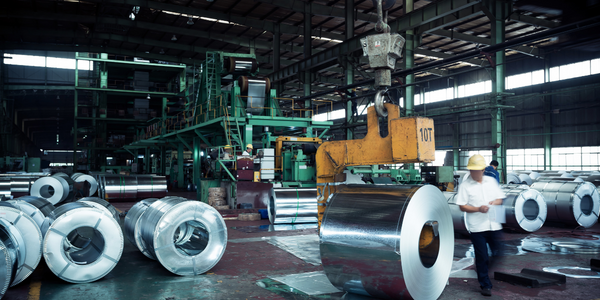
Case Study
KSP Steel Decentralized Control Room
While on-site in Pavlodar, Kazakhstan, the DAQRI team of Business Development and Solutions Architecture personnel worked closely with KSP Steel’s production leadership to understand the steel production process, operational challenges, and worker pain points.