Download PDF
Streamlining Reimbursement and Contract Management Processes at Metro Pacific Investments Corporation
Technology Category
- Application Infrastructure & Middleware - Event-Driven Application
- Cybersecurity & Privacy - Security Compliance
Applicable Industries
- Finance & Insurance
- Railway & Metro
Applicable Functions
- Procurement
- Quality Assurance
Use Cases
- Leasing Finance Automation
- Smart Contracts
Services
- System Integration
The Challenge
Metro Pacific Investments Corporation (MPIC), an infrastructure investment holding company with extensive projects in water, power, toll roads, and healthcare services, was facing significant challenges with its expense/reimbursement and contract management processes. The company's reimbursement and expense management processes were paper-based, manually completed, and labor-intensive, which impeded finance and accounting operations. There were instances of misplaced or duplicate applications, leading to slow turnaround times. Additionally, due to the stringent requirements of 3rd party audit firms, MPIC was also in need of a solution that enables instant review and retrieval of contracts. Newly signed contracts did not have a proper workflow for the legal department’s review and retrieving these contracts for update or audit purposes were a chore.
About The Customer
Metro Pacific Investments Corporation (MPIC) is an infrastructure investment holding company based in the Philippines. The company has extensive projects in various sectors including water, power, toll roads, and healthcare services. Process efficiency and compliance are of utmost importance to MPIC due to the nature of its operations. The company was previously using paper-based, manually completed processes for expense/reimbursement and contract management, which were labor-intensive and impeded finance and accounting operations.
The Solution
MPIC implemented K2 Software to automate its expense/reimbursement and contract management processes. The system automatically routes forms and applications to the appropriate approvers based on Cost Center, providing MPIC staff visibility and tracking, notifications, and escalations. For expense/reimbursement requests, any MPIC staff member is now able to submit company-related expenses and reimbursements to Finance and Accounting for approval. The solution’s escalation rule enables the expense and reimbursement requests to be tracked with automatic reminders to ensure SLAs are met. To manage contracts, a portal was set up using K2 Five, a workflow was developed for the Legal Department to review contracts thoroughly before releasing them into the portal. The solution integrates seamlessly with Microsoft SharePoint and InfoPath, allowing an all-in-one system for MPIC to render forms that are tied to workflows, making it accessible to all MPIC staff wherever they are, as long as Internet access is available.
Operational Impact
Quantitative Benefit
Related Case Studies.

Case Study
Real-time In-vehicle Monitoring
The telematic solution provides this vital premium-adjusting information. The solution also helps detect and deter vehicle or trailer theft – as soon as a theft occurs, monitoring personnel can alert the appropriate authorities, providing an exact location.“With more and more insurance companies and major fleet operators interested in monitoring driver behaviour on the grounds of road safety, efficient logistics and costs, the market for this type of device and associated e-business services is growing rapidly within Italy and the rest of Europe,” says Franco.“The insurance companies are especially interested in the pay-per-use and pay-as-you-drive applications while other organisations employ the technology for road user charging.”“One million vehicles in Italy currently carry such devices and forecasts indicate that the European market will increase tenfold by 2014.However, for our technology to work effectively, we needed a highly reliable wireless data network to carry the information between the vehicles and monitoring stations.”
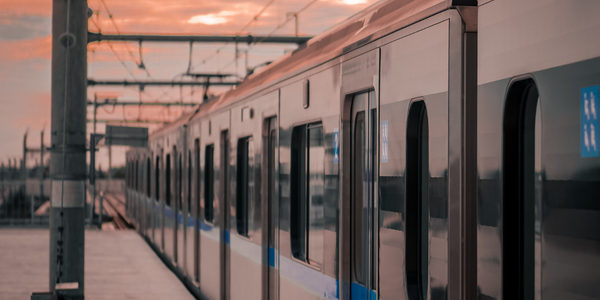
Case Study
Building Smart IoT-Connected Railways
• Difficult environment. Communications equipment on trains must function properly in harsh conditions, such as environment temperatures ranging from -25°C to +85°C, according to the EU standard EN50155.• Railway regulations. All products in a train must adhere to strict standards, relating to working vibration, power consumption, and lifetime.• Lengthy process. Time to market in the railway industry can take years from concept to mass production, so product design requires a solid long term vision.

Case Study
Safety First with Folksam
The competitiveness of the car insurance market is driving UBI growth as a means for insurance companies to differentiate their customer propositions as well as improving operational efficiency. An insurance model - usage-based insurance ("UBI") - offers possibilities for insurers to do more efficient market segmentation and accurate risk assessment and pricing. Insurers require an IoT solution for the purpose of data collection and performance analysis
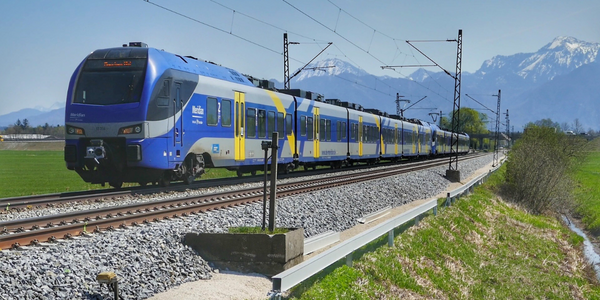
Case Study
Connected Transportation: A Smarter Brain for Your Train with Intel
A modern locomotive, for example, has as many as 200 sensors generating more than a billion data points per second. Vibration sensors surround critical components, video cameras scan the track and cab, while other sensors monitor RPM, power, temperature, the fuel mix, exhaust characteristics, and more.Most of today’s locomotives lack sufficient on-board processing power to make full use of all this data. To make matters worse, the data from different subsystems, such as the brakes, fuel system, and engine, remain separate, stored in isolated “boxes” that prevent unified analysis. The data is available, but the technology needed to process it in the most effective manner is not. As new sensors are added to the machine, the problem escalates.

Case Study
Smooth Transition to Energy Savings
The building was equipped with four end-of-life Trane water cooled chillers, located in the basement. Johnson Controls installed four York water cooled centrifugal chillers with unit mounted variable speed drives and a total installed cooling capacity of 6,8 MW. Each chiller has a capacity of 1,6 MW (variable to 1.9MW depending upon condenser water temperatures). Johnson Controls needed to design the equipment in such way that it would fit the dimensional constraints of the existing plant area and plant access route but also the specific performance requirements of the client. Morgan Stanley required the chiller plant to match the building load profile, turn down to match the low load requirement when needed and provide an improvement in the Energy Efficiency Ratio across the entire operating range. Other requirements were a reduction in the chiller noise level to improve the working environment in the plant room and a wide operating envelope coupled with intelligent controls to allow possible variation in both flow rate and temperature. The latter was needed to leverage increased capacity from a reduced number of machines during the different installation phases and allow future enhancement to a variable primary flow system.
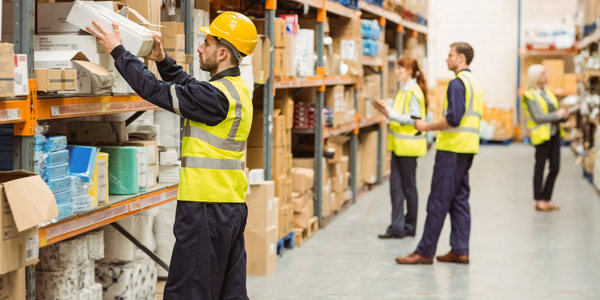
Case Study
Automated Pallet Labeling Solution for SPR Packaging
SPR Packaging, an American supplier of packaging solutions, was in search of an automated pallet labeling solution that could meet their immediate and future needs. They aimed to equip their lines with automatic printer applicators, but also required a solution that could interface with their accounting software. The challenge was to find a system that could read a 2D code on pallets at the stretch wrapper, track the pallet, and flag any pallets with unread barcodes for inspection. The pallets could be single or double stacked, and the system needed to be able to differentiate between the two. SPR Packaging sought a system integrator with extensive experience in advanced printing and tracking solutions to provide a complete traceability system.