Virtual Damage Assessment & Repair Tracking for F-35 and F-22 Aircraft

- Analytics & Modeling - Digital Twin / Simulation
- Application Infrastructure & Middleware - Middleware, SDKs & Libraries
- Aerospace
- Maintenance
- Predictive Maintenance
As part of effective maintenance for any aircraft, accurately assessing airframe damage resulting from combat or environmental hazards is crucial. Seemingly small factors — such as the depth of a scratch or the distance of a hole from supporting structures — can impact flight-worthiness, aircraft stealth capability and pilot safety. As well, in an era of reduced spending and personnel, aircraft maintenance technician efficiency is essential. Recognizing these challenges, Lockheed Martin sought to streamline its damage and assessment process for the F-35. Traditionally, maintenance technicians would manually assess and track damaged areas by placing a transparent film over these areas and tracing reference points (such as fasteners and seams) with a marker. They would then cross-reference this information with repair data history captured in a spreadsheet. However, cross-referencing line drawings did not provide the optimal platform to visualize repair information, it was also quite cumbersome and time consuming — leaving more room for maintenance errors.
To help its military customers drive maintenance technician efficiencies and improve maintenance accuracy, Lockheed Martin engineers adopted interactive 3D technology to integrate into their existing information infrastructure for the F-35 — called the Autonomic Logistics Information Systems (ALIS) software suite — streamlining a broad range of capabilities including operations, maintenance, prognostics, supply chain, and customer support services data. Their requirements were rigorous. The solution needed to: provide accuracy within 1/10th of an inch; allow complex 3D datasets to run interactively on tablet computers; and be user friendly for flight line maintainers. To satisfy these demanding requirements, Lockheed Martin selected NGRAIN to transform its damage assessment and repair system. Working closely with Lockheed engineers, NGRAIN developed the industry’s first interactive 3D Virtual Damage Repair and Tracking™ solution. Based on NGRAIN’s volume graphics technology (which provides optimal rendering performance on laptops and supports the high degree of accuracy required), and developed using NGRAIN’s Software Development Kit (SDK), the solution allows aircraft maintainers to capture damage information within a detailed 3D virtual model of the aircraft. When working with the damage assessment solution, the technician specifies the aircraft tail number — the aircraft’s unique identifier. The solution recognizes this number and immediately displays historical damage and repair data for that particular aircraft. The technician then enters metadata — such as damage type and dimensions — which is stored in the ALIS backend for future retrieval. Maintainers can use the solution to identify location of damage, insert photos and notes, as well as visually locate parts for ordering. The virtual damage assessment software — delivered on portable, ruggedized Panasonic Toughbook® computers — works with other software applications within ALIS to help maintainers quickly assess whether or not damages adversely impact aircraft mission capability. It also helps maintainers determine which damages need to be repaired to restore the aircraft to mission capability. The solution was first delivered with F-35 aircraft to United States Air Force (USAF) test sites, and is now being deployed to aircraft procured by other nations participating in the JSF program. When working with the solution, USAF maintainers reported they could more easily visualize damage repair data thanks to this integrated technology and appreciated having immediate access to historical aircraft information post-operations. This has helped maintainers save time and reduce the maintenance time-to-flight hour ratio. After seeing the F-35 VDA solution in action, USAF officials requested the same solution for the F-22 Raptor. This twin-engine aircraft — intended primarily for air-to-air combat — shares similar wing and tail designs with the F-35. Lockheed Martin again selected NGRAIN to configure its software for F-22 maintenance. As part of the project, NGRAIN modified the solution for F-22 part numbers and identifiers. In addition to helping maintainers track and record exterior aircraft damage, the F-22 NGRAIN solution allows technicians to view the interior of wing inlets. NGRAIN engineers also configured the solution for Lockheed’s Integrated Maintenance Information System (IMIS), a software suite that is the information backbone for the F-22.
Related Case Studies.
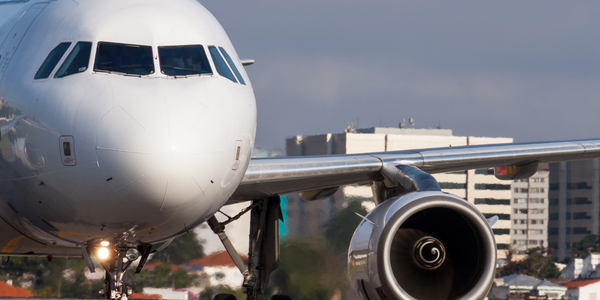
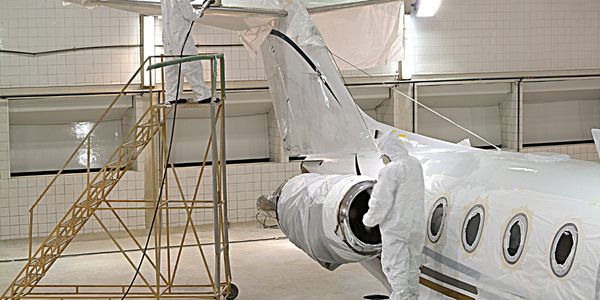
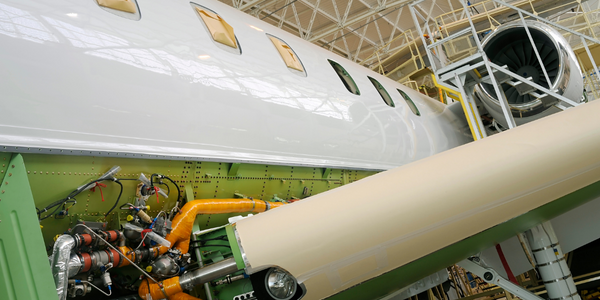
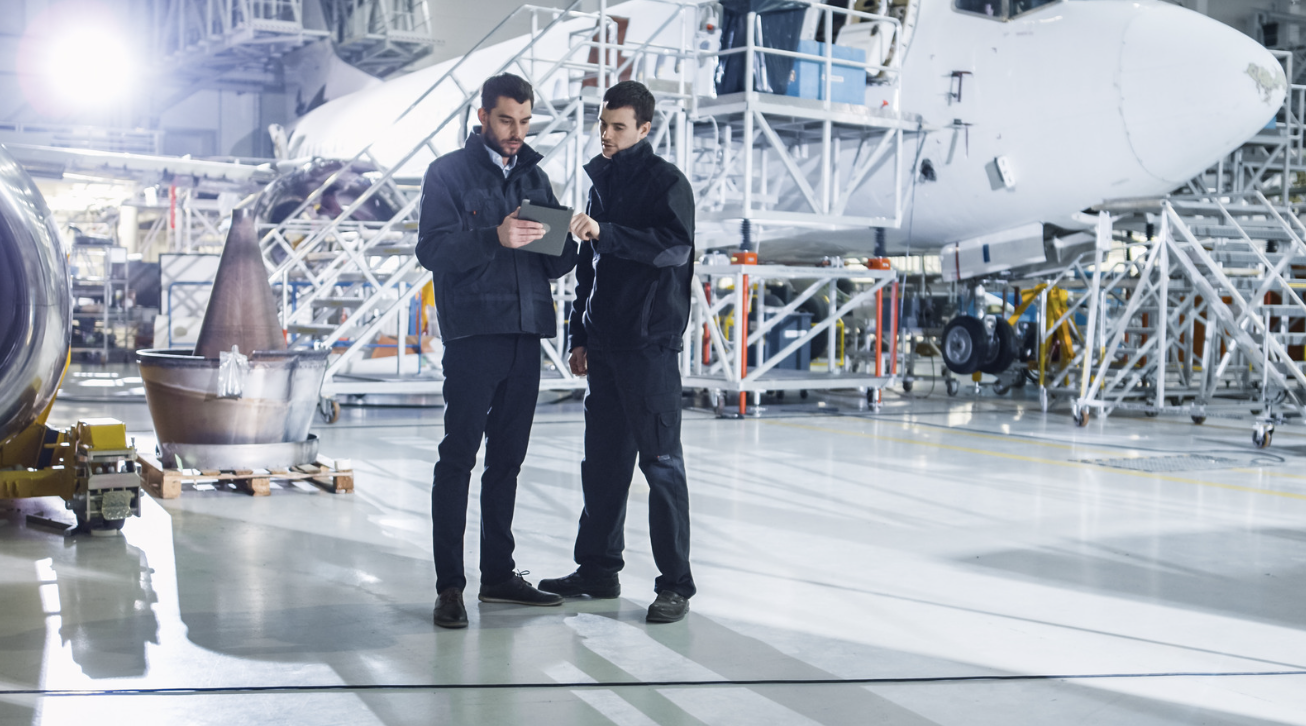
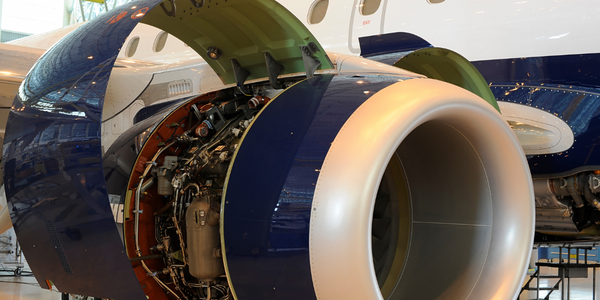