下载PDF
AirAsia's Transformation: Reducing Wait Time by 98% through Automation
适用行业
- 航天
- 水泥
适用功能
- 销售与市场营销
用例
- 对话机器人
- 租赁金融自动化
挑战
亚航面临着客户联系代理的等待时间较长以及支持时间和语言有限的挑战。这使该品牌的声誉面临风险,并阻碍了向国际受众的销售机会。
关于客户
亚洲航空是客户体验领域的全球领导者,每年载运超过 1 亿旅客飞往全球 140 多个目的地。他们希望改善客户服务并跨多个渠道扩展自动化支持。
解决方案
亚洲航空利用 Ada 平台构建并推出了 24/7 多语言聊天机器人,可以立即为客户提供帮助。该聊天机器人允许客户检查航班更新、预订航班、回答问题、更新乘客信息以及在预订中添加辅助产品。
运营影响
数量效益
相关案例.
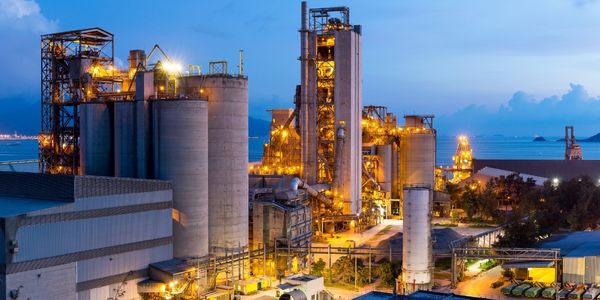
Case Study
System 800xA at Indian Cement Plants
Chettinad Cement recognized that further efficiencies could be achieved in its cement manufacturing process. It looked to investing in comprehensive operational and control technologies to manage and derive productivity and energy efficiency gains from the assets on Line 2, their second plant in India.
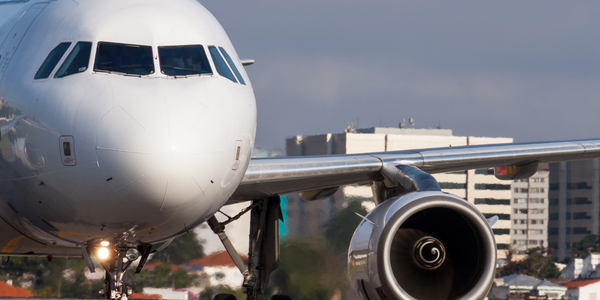
Case Study
Airbus Soars with Wearable Technology
Building an Airbus aircraft involves complex manufacturing processes consisting of thousands of moving parts. Speed and accuracy are critical to business and competitive advantage. Improvements in both would have high impact on Airbus’ bottom line. Airbus wanted to help operators reduce the complexity of assembling cabin seats and decrease the time required to complete this task.
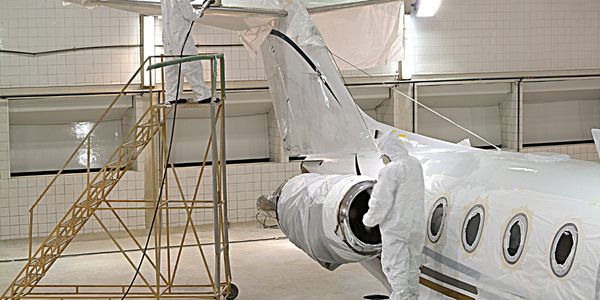
Case Study
Aircraft Predictive Maintenance and Workflow Optimization
First, aircraft manufacturer have trouble monitoring the health of aircraft systems with health prognostics and deliver predictive maintenance insights. Second, aircraft manufacturer wants a solution that can provide an in-context advisory and align job assignments to match technician experience and expertise.
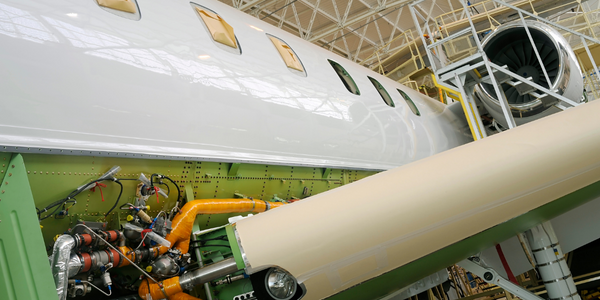
Case Study
Aerospace & Defense Case Study Airbus
For the development of its new wide-body aircraft, Airbus needed to ensure quality and consistency across all internal and external stakeholders. Airbus had many challenges including a very aggressive development schedule and the need to ramp up production quickly to satisfy their delivery commitments. The lack of communication extended design time and introduced errors that drove up costs.
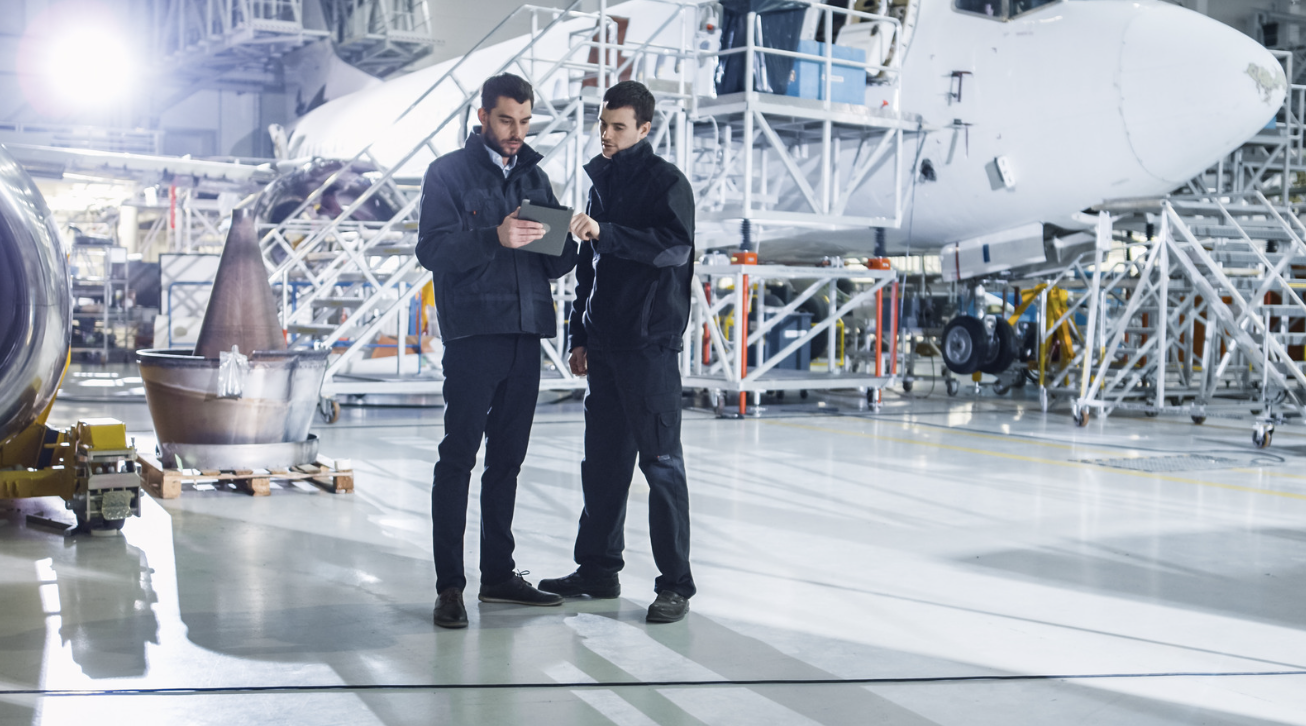
Case Study
Developing Smart Tools for the Airbus Factory
Manufacturing and assembly of aircraft, which involves tens of thousands of steps that must be followed by the operators, and a single mistake in the process could cost hundreds of thousands of dollars to fix, makes the room for error very small.