下载PDF
Amphenol's Migration to POWER9 and Implementation of Reliable Backup with Robot HA
技术
- 基础设施即服务 (IaaS) - 云计算
- 网络与连接 - 以太网
适用行业
- 航天
- 国家安全与国防
适用功能
- 质量保证
用例
- 施工管理
- 时间敏感网络
服务
- 测试与认证
挑战
当 IBM 宣布停止支持该公司所依赖的 POWER7 生产服务器时,全球军事和航空航天工业连接器制造商 Amphen 面临着重大挑战。与此同时,在纽约数据中心发生两起飓风和洪水之后,安费诺需要改善其业务连续性和灾难响应基础设施。该公司的恢复时间和停机时间是重要的考虑因素,因为全球用户社区依赖于 24/7 的正常运行时间和信息访问。此前,IBM i box 需要整整两天才能从磁带备份中恢复,这种情况对公司来说将是灾难性的。面临的挑战是通过新硬件和高可用性实现后端现代化。
关于客户
安费诺是一家为军事和航空航天工业提供坚固耐用、适合恶劣环境的连接器的全球制造商。他们的连接器用于这些行业的每个主要平台,包括商用飞机、军用地面车辆、士兵系统和卫星。该公司是世界上最大的军事和航空航天互连集团的一部分,其最大的部门 Amphenano Aerospace 位于纽约州悉尼。该公司的全球用户社区依赖于 24/7 的正常运行时间和信息访问,使业务连续性和灾难响应成为其运营的关键方面。
解决方案
安费诺决定在亚利桑那州梅萨建立一个新的数据中心,并过渡到 POWER9 服务器。该计划涉及在纽约州悉尼办事处建立一个新的生产服务器,并完全复制到亚利桑那州的第二个服务器。这需要将数据从旧的 POWER7 服务器迁移到新的 POWER9 服务器,执行角色交换,从 IBM 购买 CBU 盒子,并行复制一段时间,将 CBU 盒子运送到梅萨的灾难恢复站点,然后通过每日复制将 Mesa 服务器建立为长期故障转移选项。为了实现这一目标,Amphen 使用了 Fortra 的 IBM i 机器人 HA 高可用性解决方案。该解决方案经济高效,将预期项目时间从 12-15 小时缩短至仅 10 分钟。该团队还与 Fortra 合作,确定需要日常复制的用户库和文档。
运营影响
数量效益
相关案例.
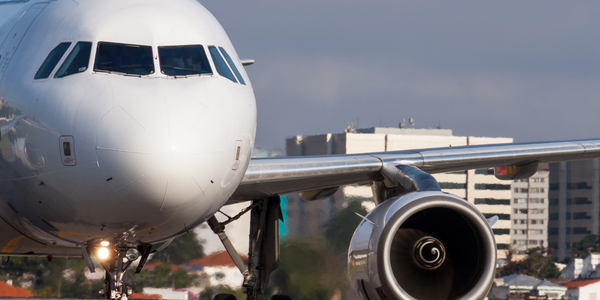
Case Study
Airbus Soars with Wearable Technology
Building an Airbus aircraft involves complex manufacturing processes consisting of thousands of moving parts. Speed and accuracy are critical to business and competitive advantage. Improvements in both would have high impact on Airbus’ bottom line. Airbus wanted to help operators reduce the complexity of assembling cabin seats and decrease the time required to complete this task.
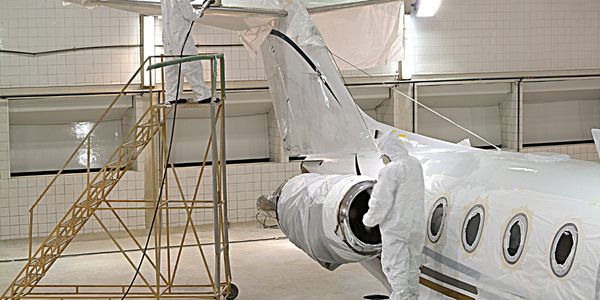
Case Study
Aircraft Predictive Maintenance and Workflow Optimization
First, aircraft manufacturer have trouble monitoring the health of aircraft systems with health prognostics and deliver predictive maintenance insights. Second, aircraft manufacturer wants a solution that can provide an in-context advisory and align job assignments to match technician experience and expertise.
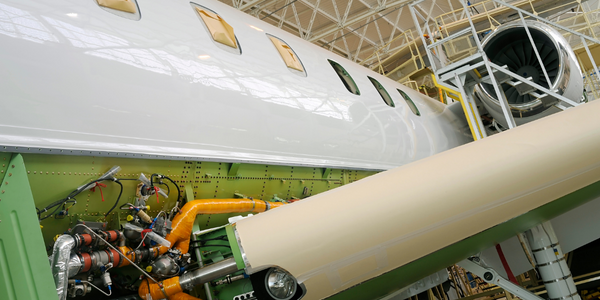
Case Study
Aerospace & Defense Case Study Airbus
For the development of its new wide-body aircraft, Airbus needed to ensure quality and consistency across all internal and external stakeholders. Airbus had many challenges including a very aggressive development schedule and the need to ramp up production quickly to satisfy their delivery commitments. The lack of communication extended design time and introduced errors that drove up costs.
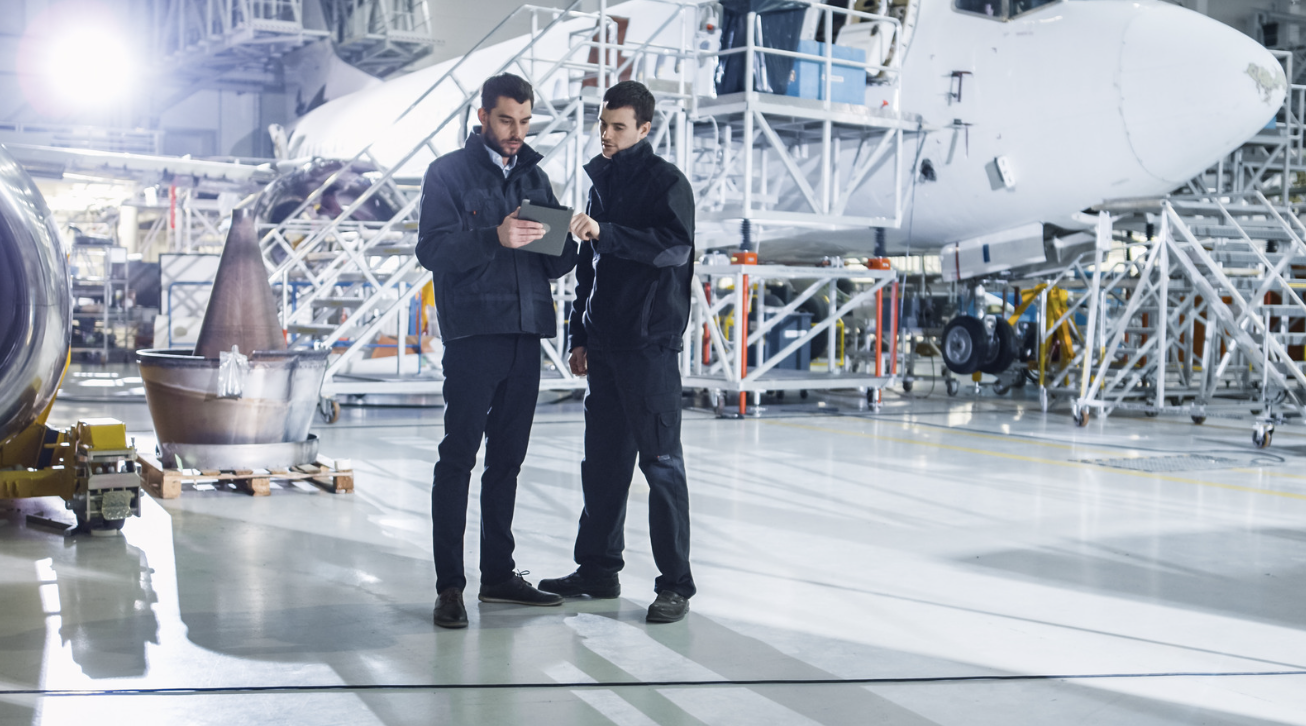
Case Study
Developing Smart Tools for the Airbus Factory
Manufacturing and assembly of aircraft, which involves tens of thousands of steps that must be followed by the operators, and a single mistake in the process could cost hundreds of thousands of dollars to fix, makes the room for error very small.
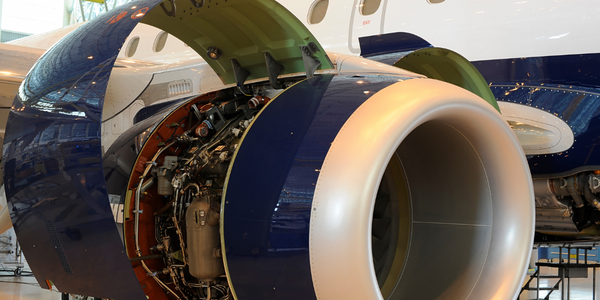
Case Study
Accelerate Production for Spirit AeroSystems
The manufacture and assembly of massive fuselage assemblies and other large structures generates a river of data. In fact, the bill of materials for a single fuselage alone can be millions of rows of data. In-house production processes and testing, as well as other manufacturers and customers created data flows that overwhelmed previous processes and information systems. Spirit’s customer base had grown substantially since their 2005 divestiture from Boeing, resulting in a $41 billion backlog of orders to fill. To address this backlog, meet increased customer demands and minimize additional capital investment, the company needed a way to improve throughput in the existing operational footprint. Spirit had a requirement from customers to increase fuselage production by 30%. To accomplish this goal, Spirit needed real-time information on its value chain and workflow. However, the two terabytes of data being pulled from their SAP ECC was unmanageable and overloaded their business warehouse. It had become time-consuming and difficult to pull aggregate data, disaggregate it for the needed information and then reassemble to create a report. During the 6-8 hours it took to build a report, another work shift (they run three per day) would have already taken place, thus the report content was out-of-date before it was ever delivered. As a result, supervisors often had to rely on manual efforts to provide charts, reports and analysis.