下载PDF
Avantis Solution provides solid Enterprise Planning, Scheduling and Compliance Management for Ash Grove Cement
技术
- 功能应用 - 企业资产管理系统 (EAM)
适用行业
- 金属
- 矿业
适用功能
- 维护
- 采购
用例
- 预测性维护
- 库存管理
服务
- 系统集成
挑战
Ash Grove Cement Company, the fifth largest cement manufacturer in the United States, was facing the challenge of maximizing profit in a highly cost-competitive market. The company needed to continuously innovate and find better ways to balance both availability and utilization of its production assets. This challenge was compounded by having to develop a standardized solution that worked for each of its nine separate production facilities. The company's long-term goal was to automate maintenance data collection at each of its facilities for a well-defined enterprise asset management process to support equipment performance reliability while interfacing with its financial software, JD Edwards One World. They needed a system that they could implement to improve operations, with the scalability to contribute to sustainable development.
关于客户
Ash Grove Cement Company is the fifth largest cement manufacturer in the United States, with an annual production capacity of more than 8 million tons per year. The company's headquarters are in Overland Park, Kansas, with production facilities located throughout the U.S. The Portland and masonry cements produced at these plants are used in the construction of highways, bridges, commercial and industrial complexes, residential homes, and numerous other applications. The company's enterprise includes management, finance, and administration functions at headquarters in Overland Park, Kansas, and autonomous mining, transportation, production, and distribution facilities in nine U.S. states.
解决方案
Ash Grove Cement Company implemented Avantis.EAM, Avantis.PRO, and Avantis VIP Advanced Scheduling to automate all data collection on kiln-related maintenance activity at one plant and extended it to remaining facilities in the following year. The Avantis software builds a detailed history of equipment information based on day-to-day maintenance activities. Equipment statistics include hours of operation, cause and frequency of downtime, and labor and material changes, all of which can be easily reviewed and analyzed. The software also supports contingency planning for unanticipated equipment failures. Technicians can review work backlogs easily, adjust work schedules, and determine appropriate maintenance procedures by studying the equipment history. Pre-entered coding helps technicians determine which equipment must be shut down during the maintenance and which can continue running.
运营影响
数量效益
相关案例.
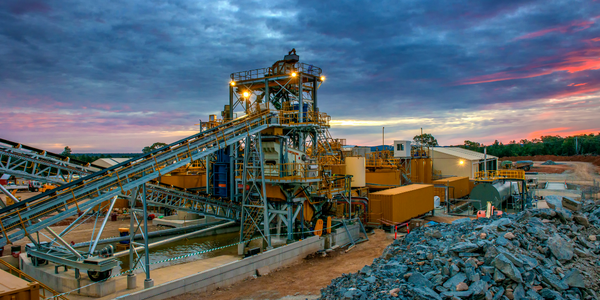
Case Study
Goldcorp: Internet of Things Enables the Mine of the Future
Goldcorp is committed to responsible mining practices and maintaining maximum safety for its workers. At the same time, the firm is constantly exploring ways to improve the efficiency of its operations, extend the life of its assets, and control costs. Goldcorp needed technology that can maximize production efficiency by tracking all mining operations, keep employees safe with remote operations and monitoring of hazardous work areas and control production costs through better asset and site management.
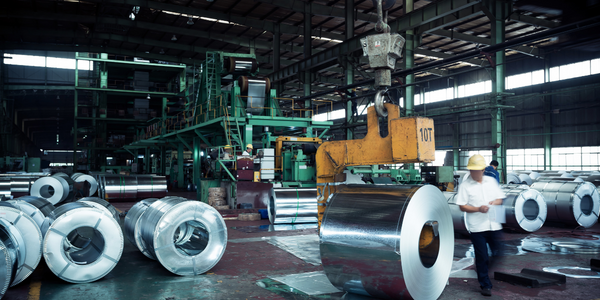
Case Study
KSP Steel Decentralized Control Room
While on-site in Pavlodar, Kazakhstan, the DAQRI team of Business Development and Solutions Architecture personnel worked closely with KSP Steel’s production leadership to understand the steel production process, operational challenges, and worker pain points.
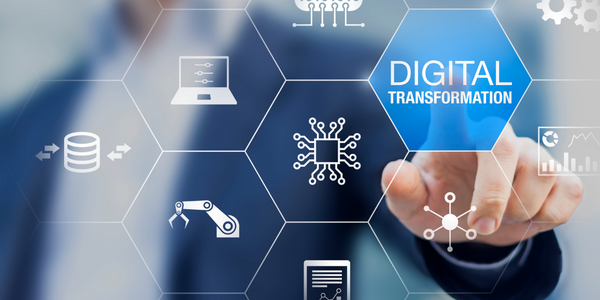
Case Study
Bluescope Steel on Path to Digitally Transform Operations and IT
Increasing competition and fluctuations in the construction market prompted BlueScope Steel to look toward digital transformation of its four businesses, including modern core applications and IT infrastructure. BlueScope needed to modernize its infrastructure and adopt new technologies to improve operations and supply chain efficiency while maintaining and updating an aging application portfolio.
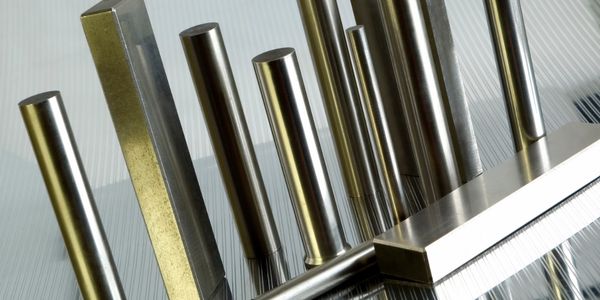
Case Study
RobotStudio Case Study: Benteler Automobiltechnik
Benteler has a small pipe business area for which they produce fuel lines and coolant lines made of aluminum for Porsche and other car manufacturers. One of the problems in production was that when Benteler added new products, production had too much downtime.
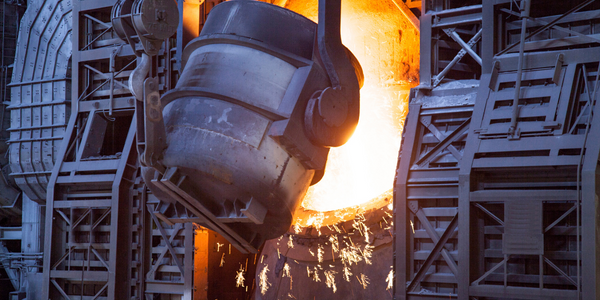
Case Study
Continuous Casting Machines in a Steel Factory
With a very broad range of applications, steel is an important material and has been developed into the most extensive alloy in the engineering world. Since delivering high quality is absolutely crucial for steel plants, ensuring maximum productivity and the best quality production are the keys to competitiveness in the steel industry. Additionally, working conditions in steel factories are not suitable for workers to stay in for long periods of time, so manufactures usually adopt various machines to complete the steel production processes. However, the precision of these machines is often overestimated and the lack of flexibility also makes supervisors unable to adjust operating procedures. A renowned steel factory in Asia planned to improve its Distributed Control System (DCS) of furnaces as well as addressing the problem of insufficient accuracy. However, most well-known international equipment suppliers can not provide a satisfactory solution and local maintenance because the project needed new technologies to more accurately control equipment operations. By implementing Advantech’s automated monitoring and control solution, steel factories can not only improve the manufacturing processes but can also allow users to add additional functions to the existing system so as to make sure the operation runs at high efficiency.
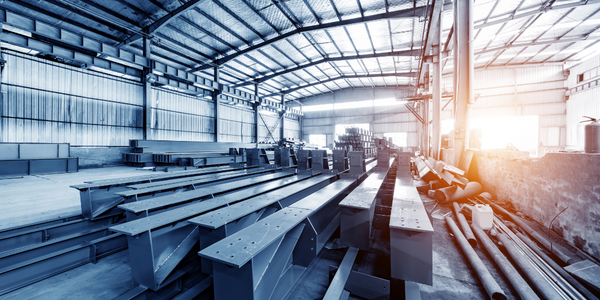
Case Study
Automated Predicitive Analytics For Steel/Metals Industry
Asset to be monitored: Wire Compactor that produces Steel RebarCustomer Faced The Following Challenges:Dependent upon machine uptime.Pressure cylinders within the compactor fail to control compression and speed causing problems in binding the coil.Equipment failure occurs in the final stage of production causing the entire line to stop, can you say bottleneck?Critical asset unequipped with sensors to produce data.