下载PDF
How a major player in the oil & gas industry decreased downtime
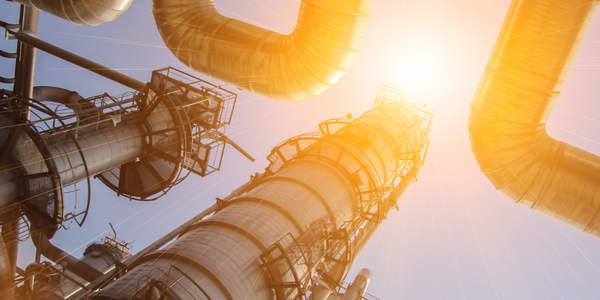
技术
- 功能应用 - 计算机化维护管理系统 (CMMS)
适用行业
- 石油和天然气
适用功能
- 维护
用例
- 预测性维护
挑战
Sean Simon 是 CIG Logistics 的运营高级副总裁,负责为石油和天然气行业的第三方转运和储存沙子。在研究 CMMS 解决方案之前,他的团队花了三年时间尝试使用基于纸质的系统来管理他们的维护操作,这给他们留下了无法收集或访问数据的主要问题。 “没有办法开采纸张。没有每日摘要,无法将评论或关键词联系在一起。”因此,试图跟踪和安排预防性维护几乎是不可能的。 “这就像在 1950 年代拥有一辆汽车。你必须试着记住你上次做某事的时间,并猜测未来需要做的维护”。
客户
CIG物流
关于客户
CIG Logistics,石油和天然气市场大规模转运和储存的合作伙伴。他们在美国的 15 个航站楼运营。
解决方案
Sean 对 CMMS 的首要要求是获得一个可以灵活适应团队需求的解决方案。他们需要一个允许他们每天做两次检查表的系统——每班一个。他探索的其他软件包很难支持这个 PM。 “我们希望确保第二个清单会触发第一个清单是否完成。当我们开始与 Fiix 交谈并表示我们需要这样做时,他们还没有这种能力,但他们实际上在短短几周内就为我们构建了它,这是任何竞争对手都无法提供的。”对于 Sean 来说,根据自己的特定需求定制解决方案的意愿最终将 Fiix 推向了胜利者的边缘。
数量效益
相关案例.
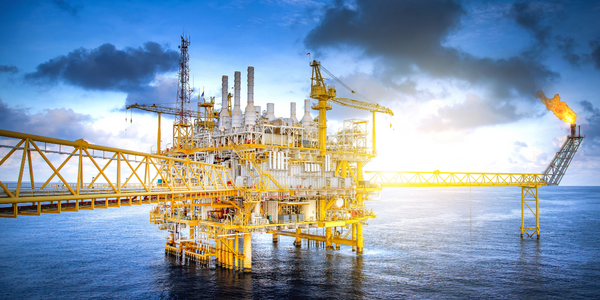
Case Study
Taking Oil and Gas Exploration to the Next Level
DownUnder GeoSolutions (DUG) wanted to increase computing performance by 5 to 10 times to improve seismic processing. The solution must build on current architecture software investments without sacrificing existing software and scale computing without scaling IT infrastructure costs.
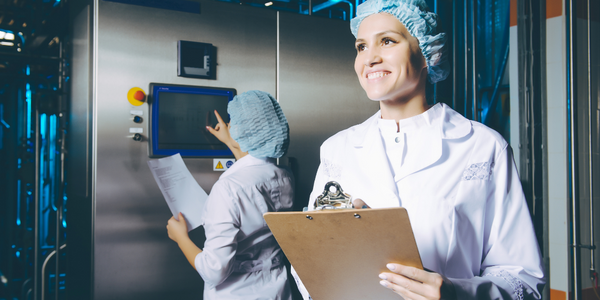
Case Study
Remote Wellhead Monitoring
Each wellhead was equipped with various sensors and meters that needed to be monitored and controlled from a central HMI, often miles away from the assets in the field. Redundant solar and wind generators were installed at each wellhead to support the electrical needs of the pumpstations, temperature meters, cameras, and cellular modules. In addition to asset management and remote control capabilities, data logging for remote surveillance and alarm notifications was a key demand from the customer. Terra Ferma’s solution needed to be power efficient, reliable, and capable of supporting high-bandwidth data-feeds. They needed a multi-link cellular connection to a central server that sustained reliable and redundant monitoring and control of flow meters, temperature sensors, power supply, and event-logging; including video and image files. This open-standard network needed to interface with the existing SCADA and proprietary network management software.
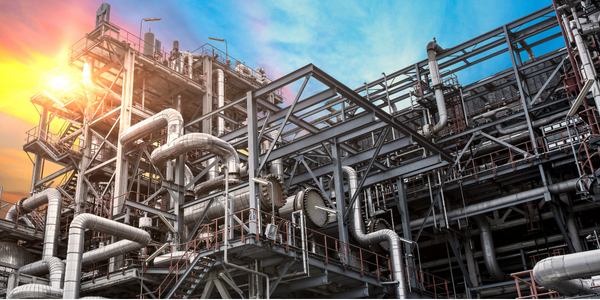
Case Study
Refinery Saves Over $700,000 with Smart Wireless
One of the largest petroleum refineries in the world is equipped to refine various types of crude oil and manufacture various grades of fuel from motor gasoline to Aviation Turbine Fuel. Due to wear and tear, eight hydrogen valves in each refinery were leaking, and each cost $1800 per ton of hydrogen vented. The plant also had leakage on nearly 30 flare control hydrocarbon valves. The refinery wanted a continuous, online monitoring system that could catch leaks early, minimize hydrogen and hydrocarbon production losses, and improve safety for maintenance.