下载PDF
Revolutionizing Aerospace Branding: The Collins Aerospace Case Study
适用行业
- 航天
- 水泥
挑战
2018 年秋季,联合技术公司完成了对罗克韦尔柯林斯公司 300 亿美元的收购,从而诞生了有史以来最大的航空航天供应商:柯林斯航空航天公司。两家合并方与 Iris 合作打造了他们的新品牌。 Iris 最近于 2017 年推出了另一个联合技术公司品牌(奥的斯电梯公司),准备为柯林斯赋予一个强大的形象,就像奥的斯的品牌一样,尊重悠久的传统,但拥抱光明的未来。
关于客户
柯林斯航空航天公司由联合技术公司和罗克韦尔柯林斯公司合并而成,目前是最大的航空航天供应商。他们生产各种飞机零部件,并希望有一个品牌能够展示他们的专业知识以及航空航天对世界的情感影响。
解决方案
Iris 帮助柯林斯航空航天公司建立了强大的品牌形象,尊重其悠久的传统,同时拥抱光明的未来。他们在一个以复杂设计为主的行业中选择了极简主义,使用高对比度的黑白摄影、有限的调色板和简单的线条来展示航空航天对世界的情感影响。该品牌的热情宗旨是“释放智慧”。提升关系。重新定义航空航天。”强调了合作伙伴关系和客户驱动的解决方案。
运营影响
相关案例.
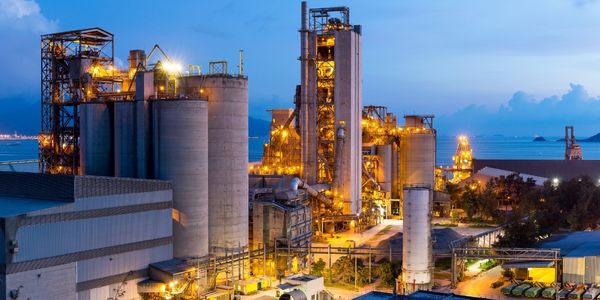
Case Study
System 800xA at Indian Cement Plants
Chettinad Cement recognized that further efficiencies could be achieved in its cement manufacturing process. It looked to investing in comprehensive operational and control technologies to manage and derive productivity and energy efficiency gains from the assets on Line 2, their second plant in India.
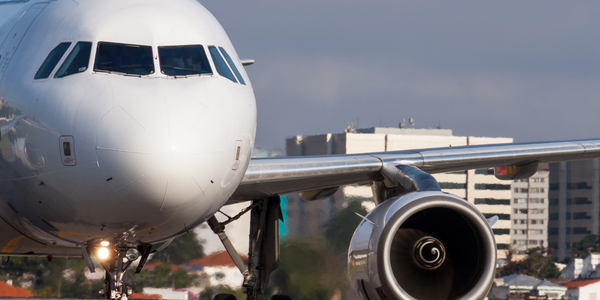
Case Study
Airbus Soars with Wearable Technology
Building an Airbus aircraft involves complex manufacturing processes consisting of thousands of moving parts. Speed and accuracy are critical to business and competitive advantage. Improvements in both would have high impact on Airbus’ bottom line. Airbus wanted to help operators reduce the complexity of assembling cabin seats and decrease the time required to complete this task.
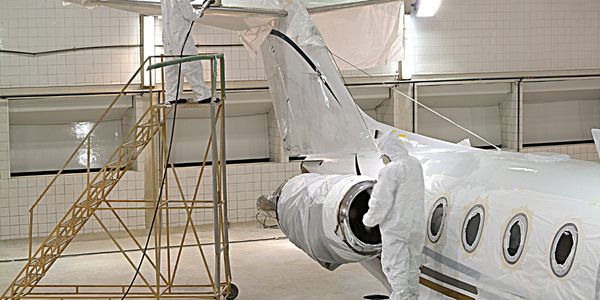
Case Study
Aircraft Predictive Maintenance and Workflow Optimization
First, aircraft manufacturer have trouble monitoring the health of aircraft systems with health prognostics and deliver predictive maintenance insights. Second, aircraft manufacturer wants a solution that can provide an in-context advisory and align job assignments to match technician experience and expertise.
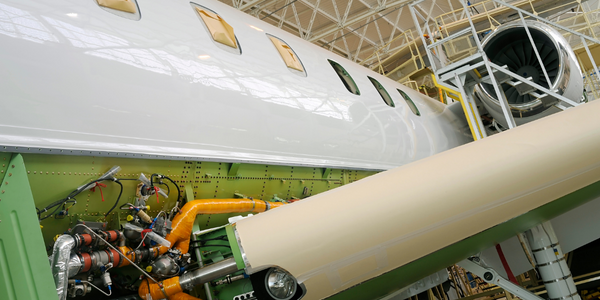
Case Study
Aerospace & Defense Case Study Airbus
For the development of its new wide-body aircraft, Airbus needed to ensure quality and consistency across all internal and external stakeholders. Airbus had many challenges including a very aggressive development schedule and the need to ramp up production quickly to satisfy their delivery commitments. The lack of communication extended design time and introduced errors that drove up costs.
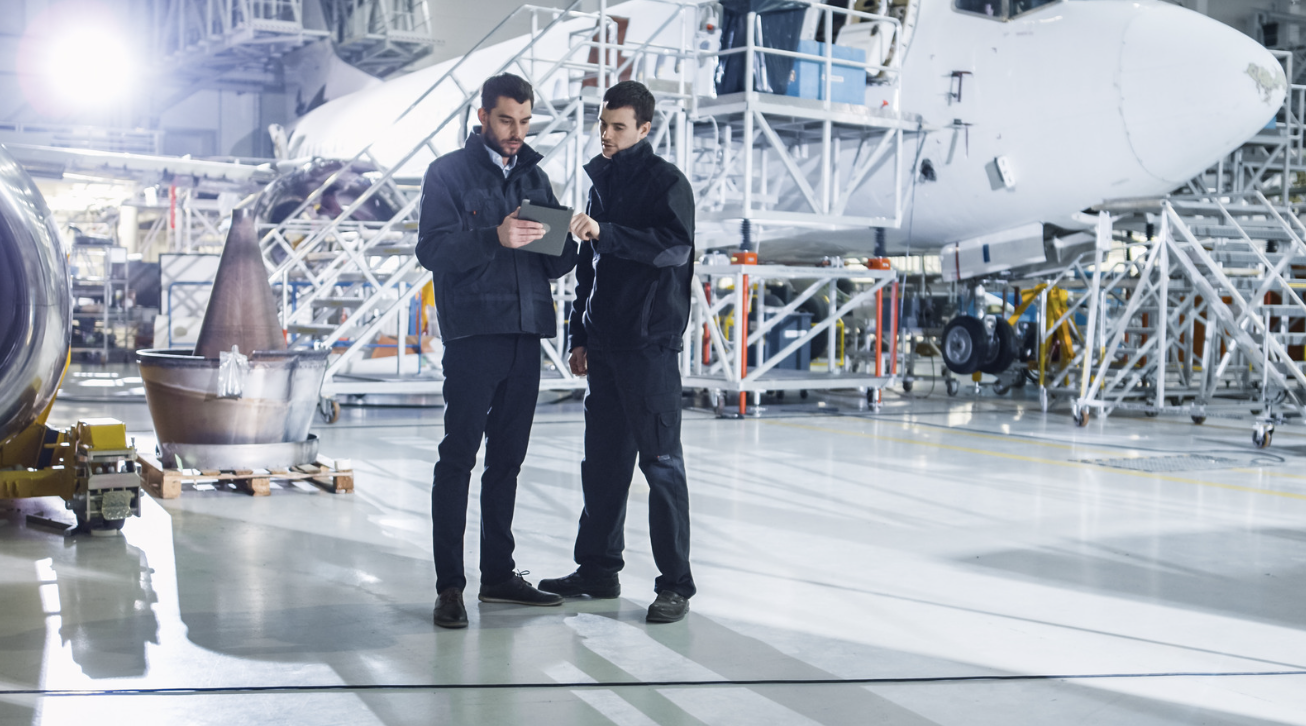
Case Study
Developing Smart Tools for the Airbus Factory
Manufacturing and assembly of aircraft, which involves tens of thousands of steps that must be followed by the operators, and a single mistake in the process could cost hundreds of thousands of dollars to fix, makes the room for error very small.