下载PDF
Revolutionizing Aerospace Industry with 3D Printing: A 63% Lighter Titanium Part
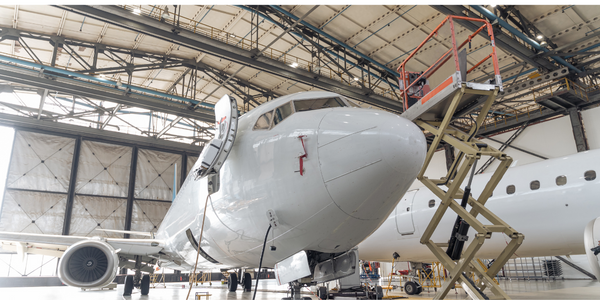
技术
- 分析与建模 - 数字孪生/模拟
- 网络与连接 - 蜂窝
适用行业
- 航天
- 生命科学
适用功能
- 产品研发
用例
- 添加剂制造
- 虚拟原型与产品测试
挑战
在不影响强度的情况下减轻金属支架的重量
客户
GE航空
关于客户
GE Aviation 是通用电气的子公司,总部位于俄亥俄州埃文代尔,位于辛辛那提郊外。 GE Aviation 是顶级飞机发动机供应商之一,为大多数商用飞机提供发动机。 GE Aviation 是通用电气集团的一部分,通用电气集团是世界上最大的公司之一。该部门在 2005 年 9 月之前一直以通用电气飞机发动机 (GEAE) 的名义运营。通用电气航空在发动机市场上的主要竞争对手是普惠和劳斯莱斯。
GE Aviation 不仅在自己的保护伞下制造发动机,而且还与其他制造商合作。 CFM International 是世界领先的飞机发动机供应商,也是 GE 最成功的合作伙伴,是与法国公司 Safran Aircraft Engines 的 50/50 合资企业。截至 2019 年,CFM International 占据全球商用飞机发动机市场份额的 39%(而 GE Aviation 本身则进一步占据 16%)。 GE 和赛峰集团还经营另一家合资企业 CFM Materials。
解决方案
创建细胞结构
使用与仿真和分析软件完美兼容的 Materialise 软件,您可以创建坚固而轻巧的工业金属零件。这个航空部件是在我们位于不来梅的金属技术中心用钛金属 3D 打印的,与传统制造的部件相比,重量减轻了 63%。
运营影响
数量效益
相关案例.
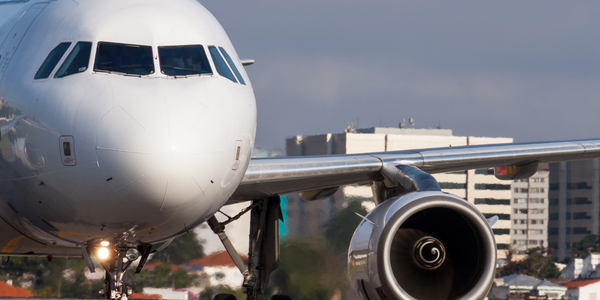
Case Study
Airbus Soars with Wearable Technology
Building an Airbus aircraft involves complex manufacturing processes consisting of thousands of moving parts. Speed and accuracy are critical to business and competitive advantage. Improvements in both would have high impact on Airbus’ bottom line. Airbus wanted to help operators reduce the complexity of assembling cabin seats and decrease the time required to complete this task.
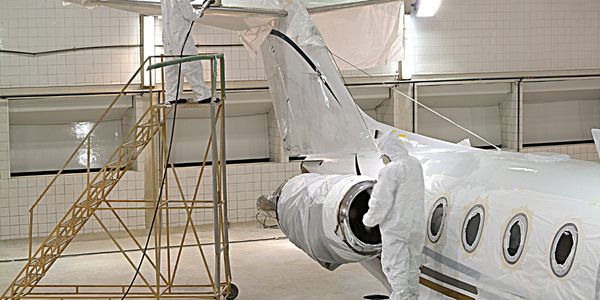
Case Study
Aircraft Predictive Maintenance and Workflow Optimization
First, aircraft manufacturer have trouble monitoring the health of aircraft systems with health prognostics and deliver predictive maintenance insights. Second, aircraft manufacturer wants a solution that can provide an in-context advisory and align job assignments to match technician experience and expertise.
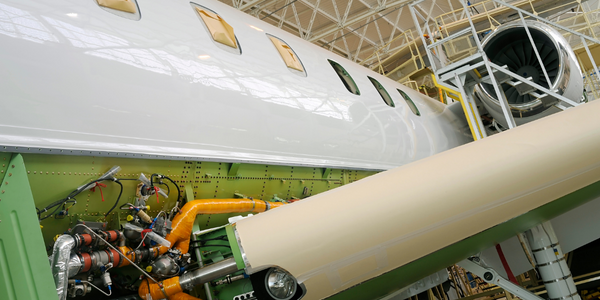
Case Study
Aerospace & Defense Case Study Airbus
For the development of its new wide-body aircraft, Airbus needed to ensure quality and consistency across all internal and external stakeholders. Airbus had many challenges including a very aggressive development schedule and the need to ramp up production quickly to satisfy their delivery commitments. The lack of communication extended design time and introduced errors that drove up costs.
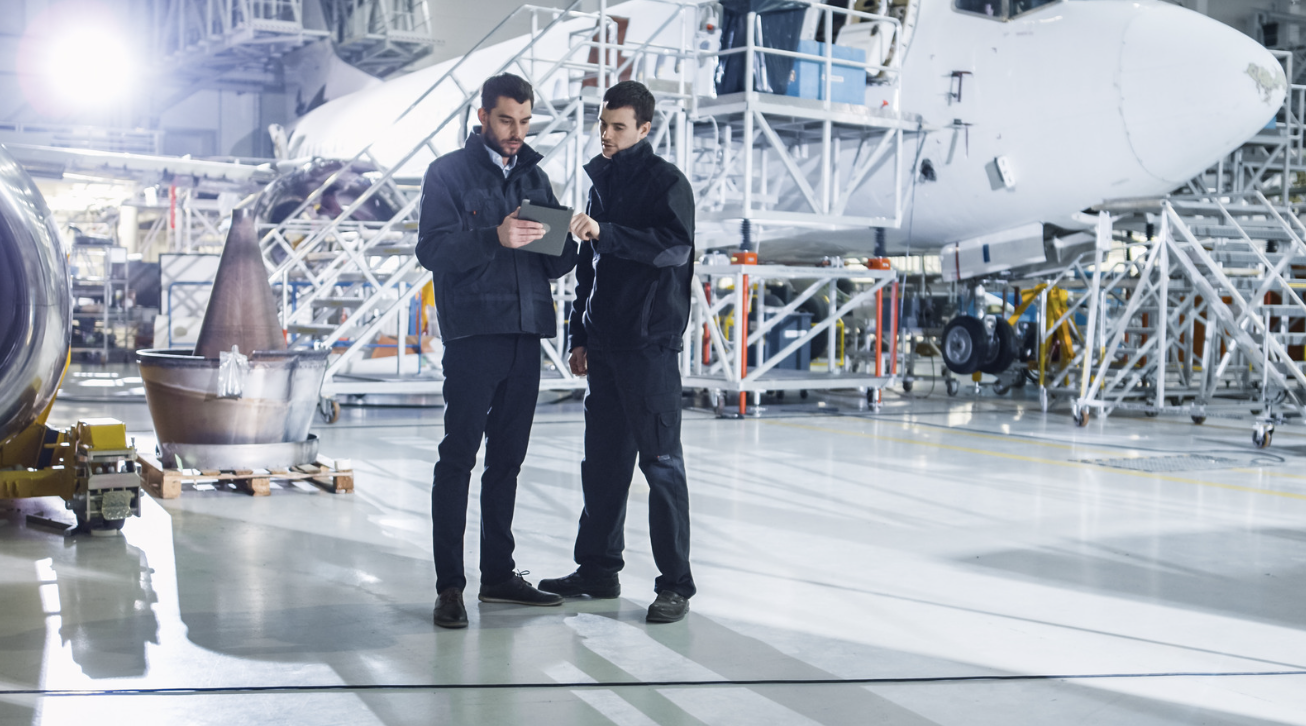
Case Study
Developing Smart Tools for the Airbus Factory
Manufacturing and assembly of aircraft, which involves tens of thousands of steps that must be followed by the operators, and a single mistake in the process could cost hundreds of thousands of dollars to fix, makes the room for error very small.
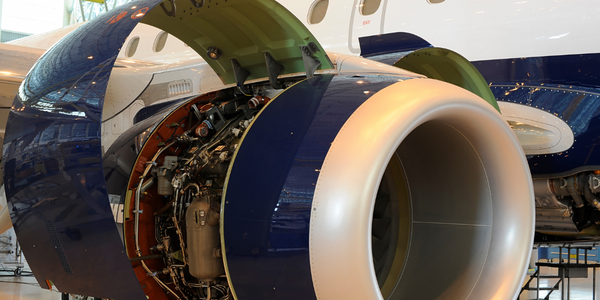
Case Study
Accelerate Production for Spirit AeroSystems
The manufacture and assembly of massive fuselage assemblies and other large structures generates a river of data. In fact, the bill of materials for a single fuselage alone can be millions of rows of data. In-house production processes and testing, as well as other manufacturers and customers created data flows that overwhelmed previous processes and information systems. Spirit’s customer base had grown substantially since their 2005 divestiture from Boeing, resulting in a $41 billion backlog of orders to fill. To address this backlog, meet increased customer demands and minimize additional capital investment, the company needed a way to improve throughput in the existing operational footprint. Spirit had a requirement from customers to increase fuselage production by 30%. To accomplish this goal, Spirit needed real-time information on its value chain and workflow. However, the two terabytes of data being pulled from their SAP ECC was unmanageable and overloaded their business warehouse. It had become time-consuming and difficult to pull aggregate data, disaggregate it for the needed information and then reassemble to create a report. During the 6-8 hours it took to build a report, another work shift (they run three per day) would have already taken place, thus the report content was out-of-date before it was ever delivered. As a result, supervisors often had to rely on manual efforts to provide charts, reports and analysis.