下载PDF
Taking the Aviation Industry to New Heights
技术
- 平台即服务 (PaaS) - 应用开发平台
适用行业
- 航天
适用功能
- 商业运营
服务
- 系统集成
- 软件设计与工程服务
挑战
AVIC, a large-scale enterprise managed by the central government of China, was facing pressure from the aviation industry to improve its processes. The company had no top-level design and individualized processes with no collective strategy. The business and IT strategy were misaligned. AVIC had a number of complex, disparate systems and processes that needed to be streamlined if it was going to outshine its competition in terms of efficiency and agility and deliver on its strategy. Its approach was twofold: First, establish its AVIC Operation System (AOS) and get IT management in order and, second, conduct an in-depth process application analysis and smarten up.
关于客户
China Aviation Industry Corporation (AVIC) is a state-owned, large-scale enterprise managed by the central government of China. Its industrial portfolio includes aviation equipment, transport aircraft and engines, trade logistics, asset management, finance, engineering construction, automobile and more. There are in excess of 100 member divisions under the management of the corporation. AVIC is administered according to the regulations associated with China’s planned economy. Rapid development of industrialization processes and information technology meant the aviation industry was soberly aware of its management function limitations compared to its advanced, international competitors.
解决方案
AVIC chose Software AG and the ARIS solution to support and unify its AOS process architecture. Software AG’s ARIS is a process-oriented model architecture based on the idea of information integration. The core idea of ARIS is to describe the various aspects of enterprise business in terms of multiple views, multi-level, multi-relevance and lifecycle. Software AG consultants worked with AVIC to conduct a comprehensive analysis to identify key process issues using their process-oriented modeling philosophy. Next they supported AVIC to describe, understand and improve the present situation of the enterprise. A series of metamodels from ARIS was deployed to establish where efficiency gains would be. Finally enterprise process management activities were implemented through ARIS in the IT environment and throughout the business.
运营影响
相关案例.
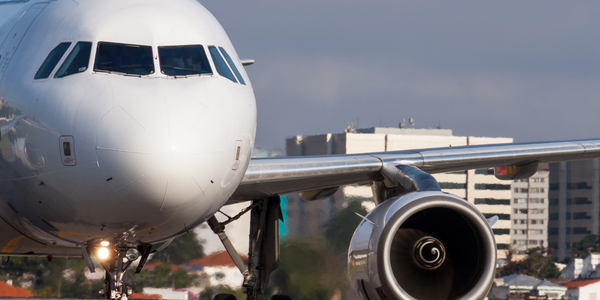
Case Study
Airbus Soars with Wearable Technology
Building an Airbus aircraft involves complex manufacturing processes consisting of thousands of moving parts. Speed and accuracy are critical to business and competitive advantage. Improvements in both would have high impact on Airbus’ bottom line. Airbus wanted to help operators reduce the complexity of assembling cabin seats and decrease the time required to complete this task.
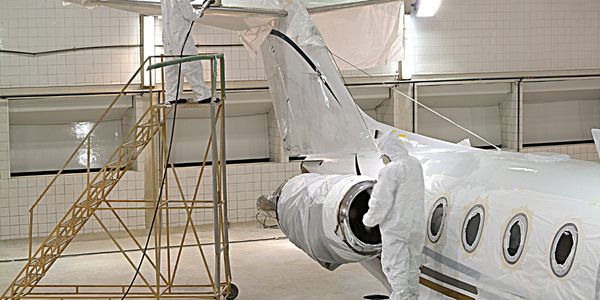
Case Study
Aircraft Predictive Maintenance and Workflow Optimization
First, aircraft manufacturer have trouble monitoring the health of aircraft systems with health prognostics and deliver predictive maintenance insights. Second, aircraft manufacturer wants a solution that can provide an in-context advisory and align job assignments to match technician experience and expertise.
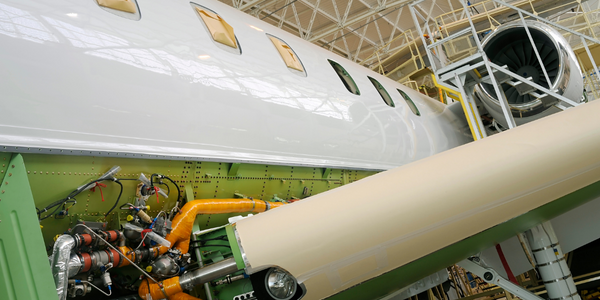
Case Study
Aerospace & Defense Case Study Airbus
For the development of its new wide-body aircraft, Airbus needed to ensure quality and consistency across all internal and external stakeholders. Airbus had many challenges including a very aggressive development schedule and the need to ramp up production quickly to satisfy their delivery commitments. The lack of communication extended design time and introduced errors that drove up costs.
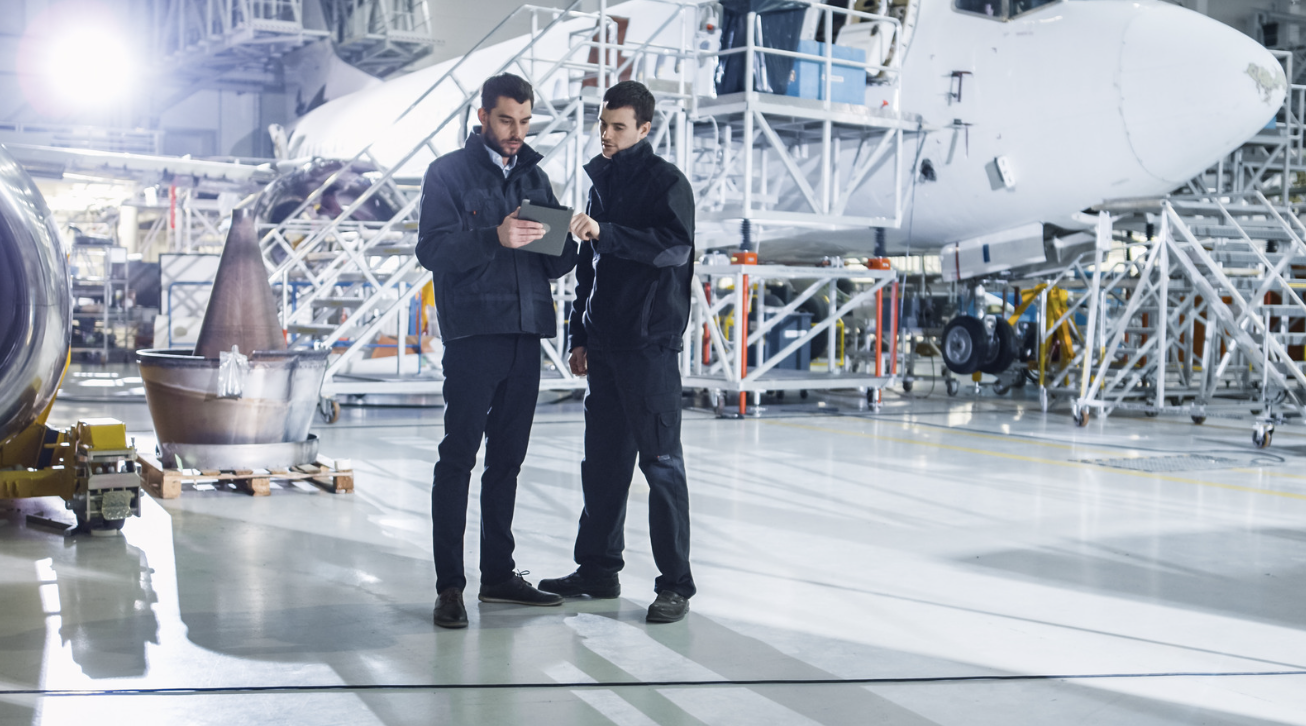
Case Study
Developing Smart Tools for the Airbus Factory
Manufacturing and assembly of aircraft, which involves tens of thousands of steps that must be followed by the operators, and a single mistake in the process could cost hundreds of thousands of dollars to fix, makes the room for error very small.
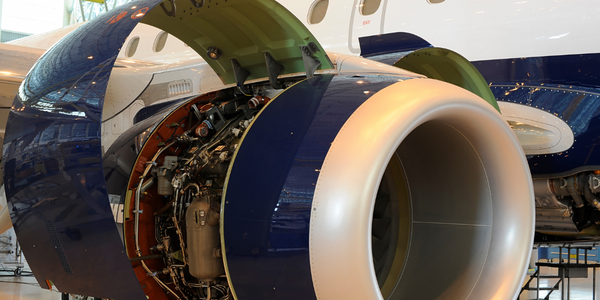
Case Study
Accelerate Production for Spirit AeroSystems
The manufacture and assembly of massive fuselage assemblies and other large structures generates a river of data. In fact, the bill of materials for a single fuselage alone can be millions of rows of data. In-house production processes and testing, as well as other manufacturers and customers created data flows that overwhelmed previous processes and information systems. Spirit’s customer base had grown substantially since their 2005 divestiture from Boeing, resulting in a $41 billion backlog of orders to fill. To address this backlog, meet increased customer demands and minimize additional capital investment, the company needed a way to improve throughput in the existing operational footprint. Spirit had a requirement from customers to increase fuselage production by 30%. To accomplish this goal, Spirit needed real-time information on its value chain and workflow. However, the two terabytes of data being pulled from their SAP ECC was unmanageable and overloaded their business warehouse. It had become time-consuming and difficult to pull aggregate data, disaggregate it for the needed information and then reassemble to create a report. During the 6-8 hours it took to build a report, another work shift (they run three per day) would have already taken place, thus the report content was out-of-date before it was ever delivered. As a result, supervisors often had to rely on manual efforts to provide charts, reports and analysis.