下载PDF
We Deliver Results in Productivity. Overoming Challenges in the Aerospace Industry
技术
- 功能应用 - 制造执行系统 (MES)
- 分析与建模 - 实时分析
适用行业
- 航天
适用功能
- 离散制造
- 质量保证
用例
- 自动化制造系统
- 预测性维护
- 实时定位系统 (RTLS)
服务
- 系统集成
- 数据科学服务
挑战
Manufacturing processes in aerospace machine shops can be complicated and complex to plan. Finding out how much capacity is really needed for a part to be produced, and accurately planning the total throughput time for a range of components can be a headache for many manufacturers. Often, it can be difficult to do accurate part costing, as many cost centres are involved, and blended rates are used as there are is no exact data on machines and work stations in a process. Many aerospace companies have vast untapped potential for reducing costs by improving processes, reducing WIP and faster throughput times, but in most cases they have no tangible data to base cost saving improvements on. UK aerospace companies are notorious for their excellent technical knowledge and high quality products. But the manufacturing process itself is often far from efficient. The orders are there, the requirements are clear, but capacities are limited and many battle with considerable overload on the shop floor.
关于客户
The customer is a part of the UK aerospace industry, which comprises over 600 businesses and employs 113,000 people directly and 276,000 indirectly. The industry generates an annual revenue of £27.8bn. The companies in this industry are known for their excellent technical knowledge and high-quality products. However, the manufacturing process is often inefficient, with limited capacities and considerable overload on the shop floor. The orders and requirements are clear, but the companies often struggle with complex planning, accurate part costing, and lack of exact data on machines and work stations in a process.
解决方案
FORCAM provides an Industry 4.0 / Industrial IoT solution that specialises in connecting machines and systems so they can exchange information, thus making improvements in the way manufacturers work. The solution includes data recording for a complete manufacturing digital fingerprint, real-time analysis of production data for instant understanding of issues, data collection on machine status and order progress to optimise the plant floor, role-relevant reporting for real time intervention, ERP integration for live order and operations feedback, integration and Interoperability of any third-party solution, and finite scheduling to identify bottlenecks and speed up order throughput. The solution can help identify bottlenecks through automated data collection from all assets and work places. Rescheduling orders on the shop floor can increase machine utilisation and free up capacities, thereby reducing overload on bottleneck assets. The solution also offers accurate run times on machines per product per unit, which can enhance cost models and iron out inefficiencies.
运营影响
相关案例.
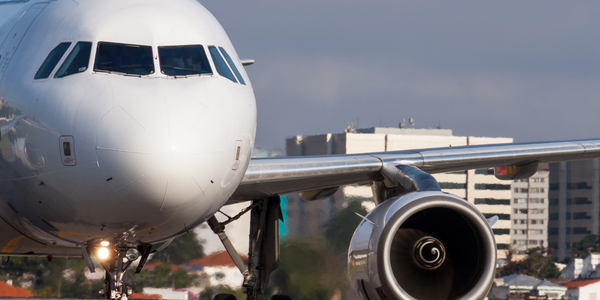
Case Study
Airbus Soars with Wearable Technology
Building an Airbus aircraft involves complex manufacturing processes consisting of thousands of moving parts. Speed and accuracy are critical to business and competitive advantage. Improvements in both would have high impact on Airbus’ bottom line. Airbus wanted to help operators reduce the complexity of assembling cabin seats and decrease the time required to complete this task.
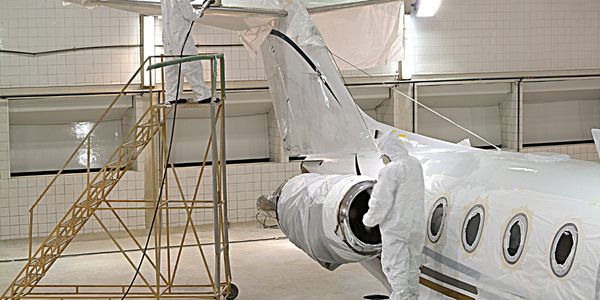
Case Study
Aircraft Predictive Maintenance and Workflow Optimization
First, aircraft manufacturer have trouble monitoring the health of aircraft systems with health prognostics and deliver predictive maintenance insights. Second, aircraft manufacturer wants a solution that can provide an in-context advisory and align job assignments to match technician experience and expertise.
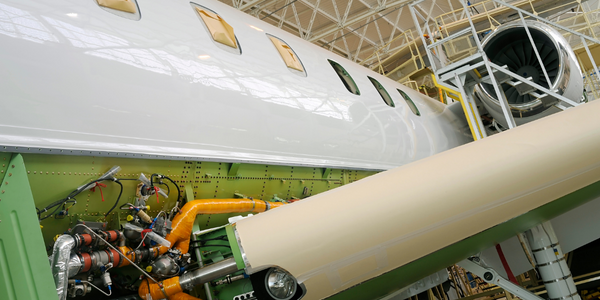
Case Study
Aerospace & Defense Case Study Airbus
For the development of its new wide-body aircraft, Airbus needed to ensure quality and consistency across all internal and external stakeholders. Airbus had many challenges including a very aggressive development schedule and the need to ramp up production quickly to satisfy their delivery commitments. The lack of communication extended design time and introduced errors that drove up costs.
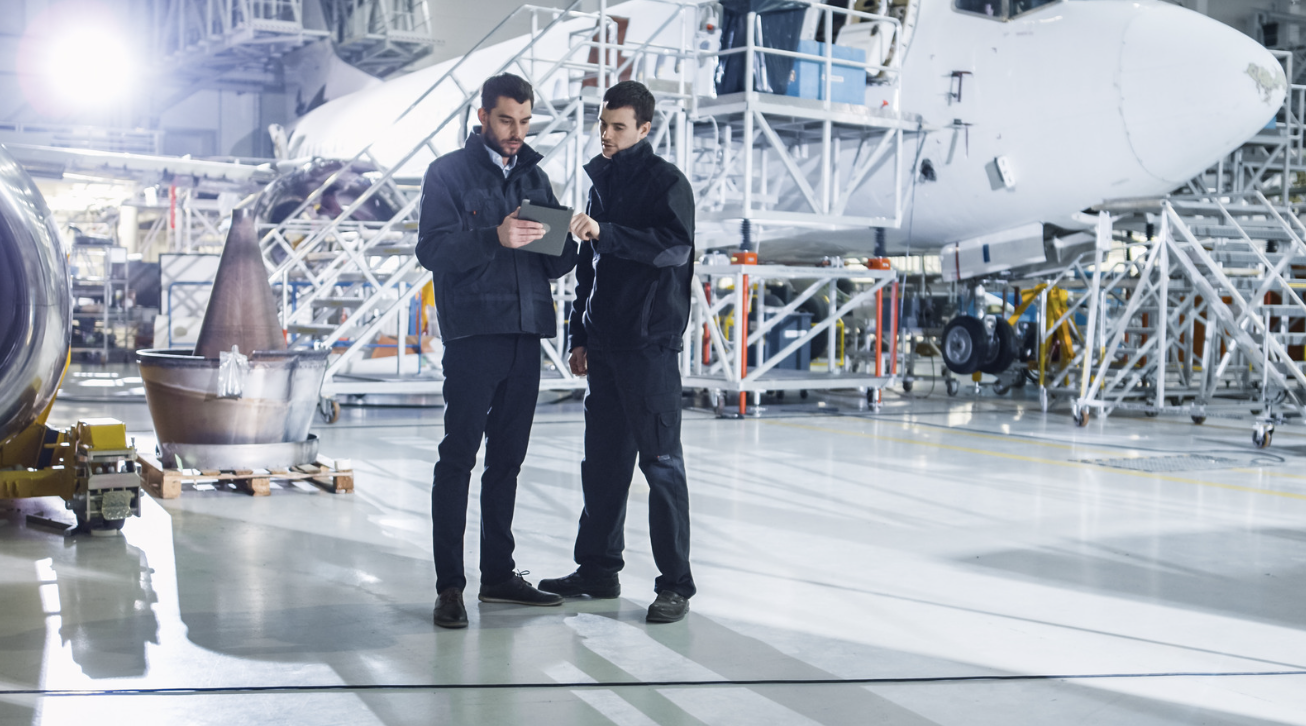
Case Study
Developing Smart Tools for the Airbus Factory
Manufacturing and assembly of aircraft, which involves tens of thousands of steps that must be followed by the operators, and a single mistake in the process could cost hundreds of thousands of dollars to fix, makes the room for error very small.
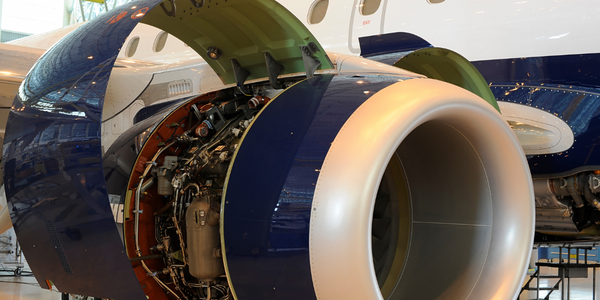
Case Study
Accelerate Production for Spirit AeroSystems
The manufacture and assembly of massive fuselage assemblies and other large structures generates a river of data. In fact, the bill of materials for a single fuselage alone can be millions of rows of data. In-house production processes and testing, as well as other manufacturers and customers created data flows that overwhelmed previous processes and information systems. Spirit’s customer base had grown substantially since their 2005 divestiture from Boeing, resulting in a $41 billion backlog of orders to fill. To address this backlog, meet increased customer demands and minimize additional capital investment, the company needed a way to improve throughput in the existing operational footprint. Spirit had a requirement from customers to increase fuselage production by 30%. To accomplish this goal, Spirit needed real-time information on its value chain and workflow. However, the two terabytes of data being pulled from their SAP ECC was unmanageable and overloaded their business warehouse. It had become time-consuming and difficult to pull aggregate data, disaggregate it for the needed information and then reassemble to create a report. During the 6-8 hours it took to build a report, another work shift (they run three per day) would have already taken place, thus the report content was out-of-date before it was ever delivered. As a result, supervisors often had to rely on manual efforts to provide charts, reports and analysis.