Download PDF
Digital Transformation in Engineering: A Case Study of Williams Engineering Canada
Technology Category
- Analytics & Modeling - Robotic Process Automation (RPA)
- Infrastructure as a Service (IaaS) - Cloud Computing
Applicable Industries
- Cement
- Retail
Applicable Functions
- Quality Assurance
- Sales & Marketing
Use Cases
- Onsite Human Safety Management
- Process Control & Optimization
Services
- Cloud Planning, Design & Implementation Services
- Training
The Challenge
Williams Engineering Canada (WEC), a multidisciplinary firm offering consulting engineering services, was seeking to digitally transform its business. The company wanted to leverage process automation to drive greater efficiencies and free up its employees to focus on innovation and customer service. The challenge was to standardize and improve efficiency across all areas of the business. WEC also faced the challenge of attracting and retaining top-level technology talent, which is in high demand across various sectors. The company needed a solution that would provide agility and scalability to implement their multi-year digital transformation strategy. Additionally, WEC had to ensure a strong safety program to protect its staff and the teams they work with, which included various forms that were previously completed on paper or an editable PDF. This paper-based process was time-consuming and created tracking and reporting challenges.
About The Customer
Founded over 40 years ago, Williams Engineering Canada (WEC) is a multidisciplinary firm offering consulting engineering services for new construction and existing building projects. The company has 180 employees based out of offices in Northern and Western Canada. WEC is committed to ensuring a strong safety program to protect its staff and the teams they work with. The company was seeking to digitally transform its business to drive greater efficiencies, improve productivity, and free up its employees to focus on innovation and customer service.
The Solution
WEC decided to take a non-traditional approach to its IT functions by migrating its information and processes to the cloud and outsourcing IT projects to technology partners. This allowed the company to focus on its overall digital transformation strategy and change management. WEC chose Nintex Forms and Workflow as their process automation tool. The company started by automating the company’s vacation request form and approval process. Following its success, WEC transformed critical HR processes into one cohesive application using Nintex Forms and Nintex Workflow. The forms were made accessible from a centralized dashboard on SharePoint, personalized to each employee, and backed by 19 Nintex Workflows that assign tasks and automate reminders. WEC also automated their job hazard assessment and incident investigation processes with Nintex. Using Nintex Forms, Nintex Workflow and Nintex App Studio, a fully customized and automated solution was created, eliminating the need for paper forms.
Operational Impact
Quantitative Benefit
Related Case Studies.
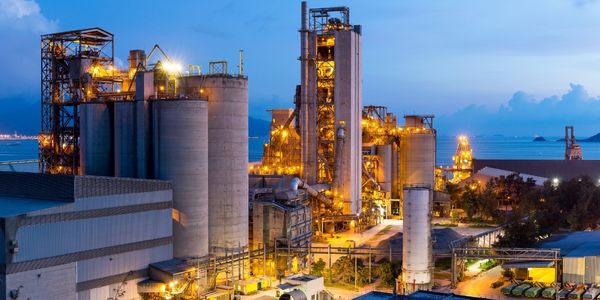
Case Study
System 800xA at Indian Cement Plants
Chettinad Cement recognized that further efficiencies could be achieved in its cement manufacturing process. It looked to investing in comprehensive operational and control technologies to manage and derive productivity and energy efficiency gains from the assets on Line 2, their second plant in India.
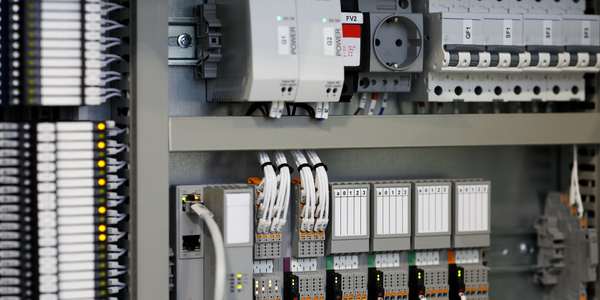
Case Study
Improving Production Line Efficiency with Ethernet Micro RTU Controller
Moxa was asked to provide a connectivity solution for one of the world's leading cosmetics companies. This multinational corporation, with retail presence in 130 countries, 23 global braches, and over 66,000 employees, sought to improve the efficiency of their production process by migrating from manual monitoring to an automatic productivity monitoring system. The production line was being monitored by ABB Real-TPI, a factory information system that offers data collection and analysis to improve plant efficiency. Due to software limitations, the customer needed an OPC server and a corresponding I/O solution to collect data from additional sensor devices for the Real-TPI system. The goal is to enable the factory information system to more thoroughly collect data from every corner of the production line. This will improve its ability to measure Overall Equipment Effectiveness (OEE) and translate into increased production efficiencies. System Requirements • Instant status updates while still consuming minimal bandwidth to relieve strain on limited factory networks • Interoperable with ABB Real-TPI • Small form factor appropriate for deployment where space is scarce • Remote software management and configuration to simplify operations
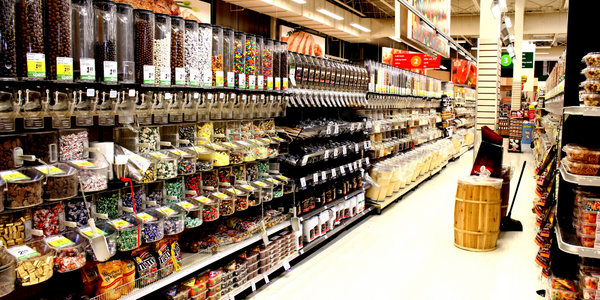
Case Study
How Sirqul’s IoT Platform is Crafting Carrefour’s New In-Store Experiences
Carrefour Taiwan’s goal is to be completely digital by end of 2018. Out-dated manual methods for analysis and assumptions limited Carrefour’s ability to change the customer experience and were void of real-time decision-making capabilities. Rather than relying solely on sales data, assumptions, and disparate systems, Carrefour Taiwan’s CEO led an initiative to find a connected IoT solution that could give the team the ability to make real-time changes and more informed decisions. Prior to implementing, Carrefour struggled to address their conversion rates and did not have the proper insights into the customer decision-making process nor how to make an immediate impact without losing customer confidence.
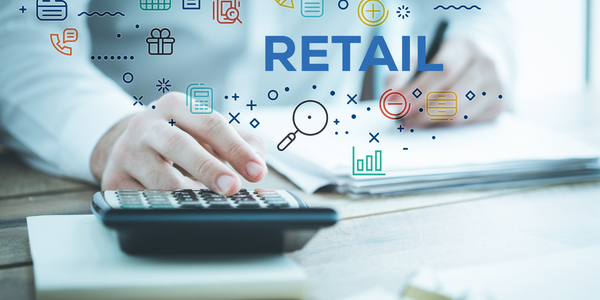
Case Study
Digital Retail Security Solutions
Sennco wanted to help its retail customers increase sales and profits by developing an innovative alarm system as opposed to conventional connected alarms that are permanently tethered to display products. These traditional security systems were cumbersome and intrusive to the customer shopping experience. Additionally, they provided no useful data or analytics.
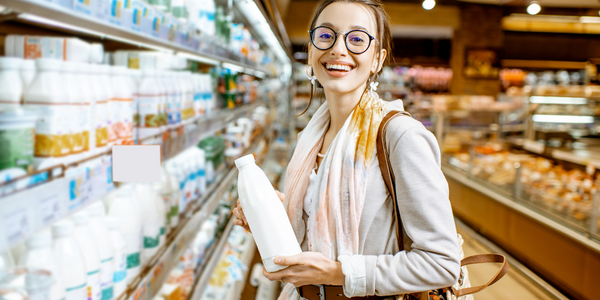
Case Study
Ensures Cold Milk in Your Supermarket
As of 2014, AK-Centralen has over 1,500 Danish supermarkets equipped, and utilizes 16 operators, and is open 24 hours a day, 365 days a year. AK-Centralen needed the ability to monitor the cooling alarms from around the country, 24 hours a day, 365 days a year. Each and every time the door to a milk cooler or a freezer does not close properly, an alarm goes off on a computer screen in a control building in southwestern Odense. This type of alarm will go off approximately 140,000 times per year, equating to roughly 400 alarms in a 24-hour period. Should an alarm go off, then there is only a limited amount of time to act before dairy products or frozen pizza must be disposed of, and this type of waste can quickly start to cost a supermarket a great deal of money.