Download PDF
Dynamic Optimization of Inventory Management in Aerospace Manufacturing
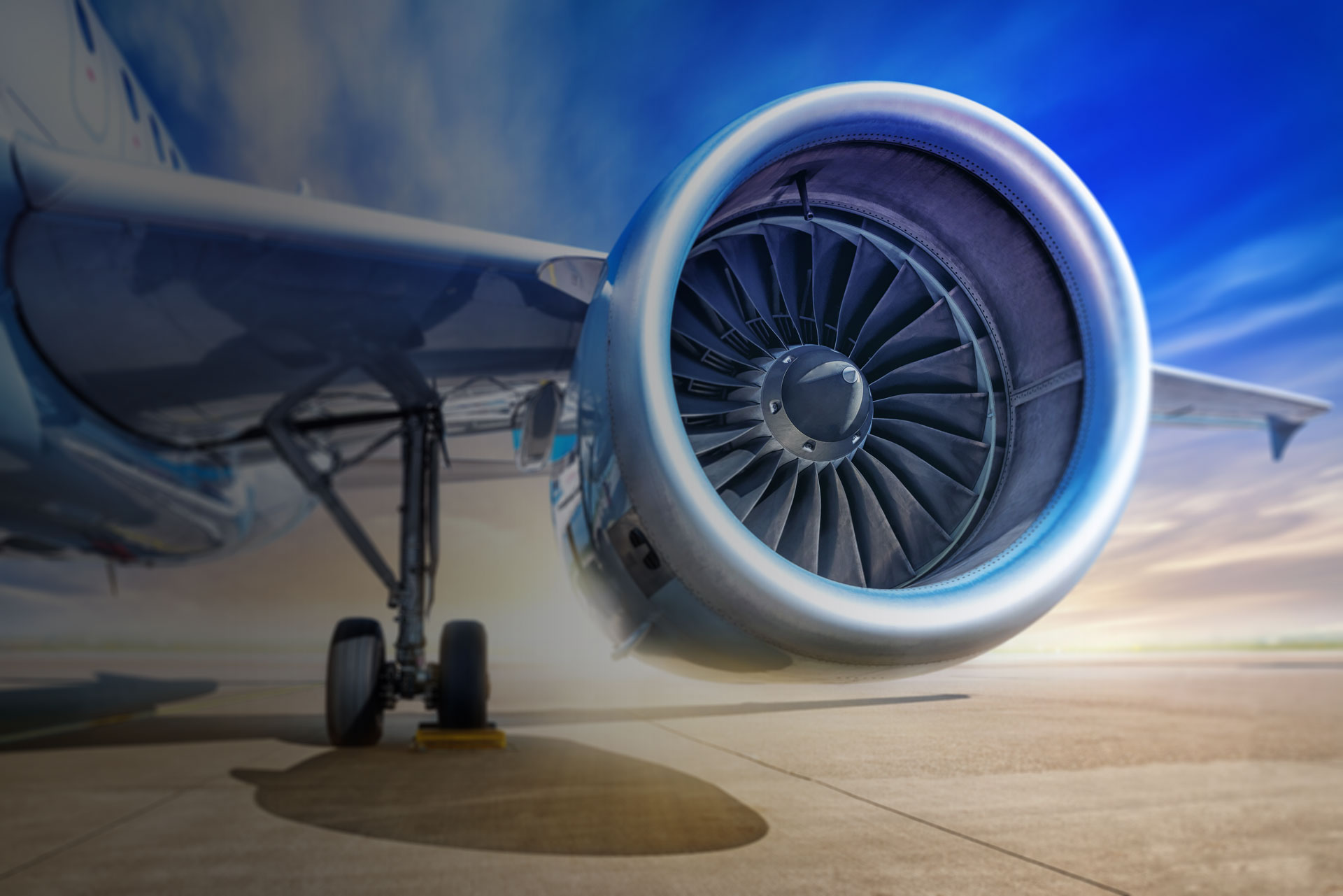
Technology Category
- Application Infrastructure & Middleware - Event-Driven Application
- Functional Applications - Inventory Management Systems
Applicable Industries
- Aerospace
Applicable Functions
- Logistics & Transportation
- Warehouse & Inventory Management
Use Cases
- Inventory Management
- Picking, Sorting & Positioning
The Challenge
A global manufacturer of aircraft engines, avionics, and other aviation products was grappling with the complexity of managing its supply chain. The company maintains 90 major product lines that require tens of thousands of parts from hundreds of manufacturers spread across the globe. The costs of maintaining inventory were significant, with just two components of its aircraft engines accounting for $600 million in parts inventory, including $400 million in fast-moving inventory. The company was seeking ways to optimize inventory levels to mitigate supplier delays and improve gross margins and revenue.
The Customer
Not Disclosed
About The Customer
The customer is a Fortune 100 software-industrial company with $16 billion in worldwide aerospace sales. The company employs 40,000 people and operates 100 manufacturing sites. It maintains six supply chain systems and produces 90 major product lines with variations that require tens of thousands of parts from hundreds of manufacturers spread across the globe. The company's products include aircraft engines, avionics, and other aviation products.
The Solution
The company decided to trial the C3 AI Inventory Optimization application as part of its push to optimize operations and invest in software. The application uses artificial intelligence to build a real-time view of inventory levels and supplier risks, enabling the company to reduce inventory levels while maintaining or even improving service levels. The trial lasted 10 weeks and demonstrated significant savings in inventory holding costs and accurately predicted supplier delays. The company's project objectives included integrating data from six supply chain systems to create a unified federated data image, applying AI to dynamically optimize inventory levels, and creating a production-ready application to detect supplier de-commit risk and streamline workflow and analytics for supply chain managers.
Operational Impact
Quantitative Benefit
Related Case Studies.
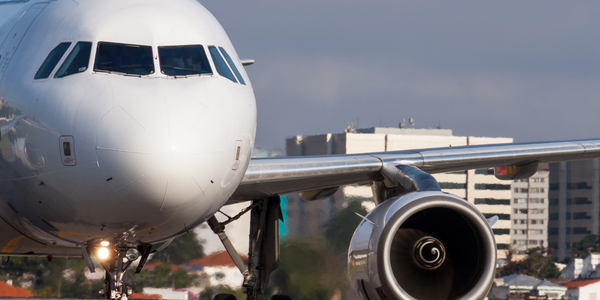
Case Study
Airbus Soars with Wearable Technology
Building an Airbus aircraft involves complex manufacturing processes consisting of thousands of moving parts. Speed and accuracy are critical to business and competitive advantage. Improvements in both would have high impact on Airbus’ bottom line. Airbus wanted to help operators reduce the complexity of assembling cabin seats and decrease the time required to complete this task.
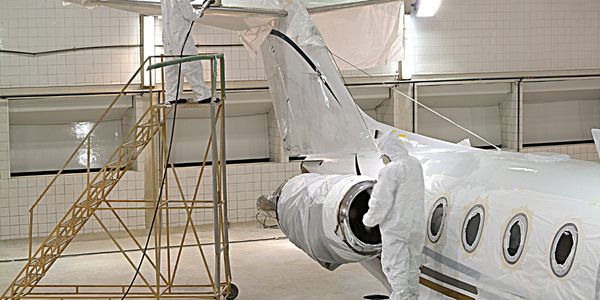
Case Study
Aircraft Predictive Maintenance and Workflow Optimization
First, aircraft manufacturer have trouble monitoring the health of aircraft systems with health prognostics and deliver predictive maintenance insights. Second, aircraft manufacturer wants a solution that can provide an in-context advisory and align job assignments to match technician experience and expertise.
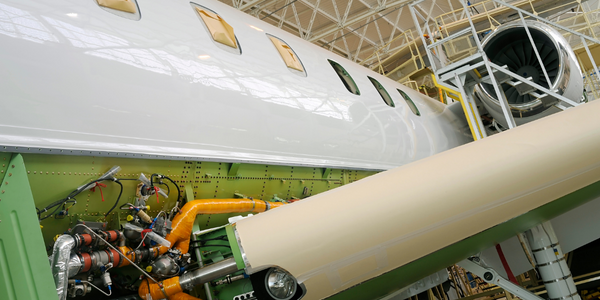
Case Study
Aerospace & Defense Case Study Airbus
For the development of its new wide-body aircraft, Airbus needed to ensure quality and consistency across all internal and external stakeholders. Airbus had many challenges including a very aggressive development schedule and the need to ramp up production quickly to satisfy their delivery commitments. The lack of communication extended design time and introduced errors that drove up costs.
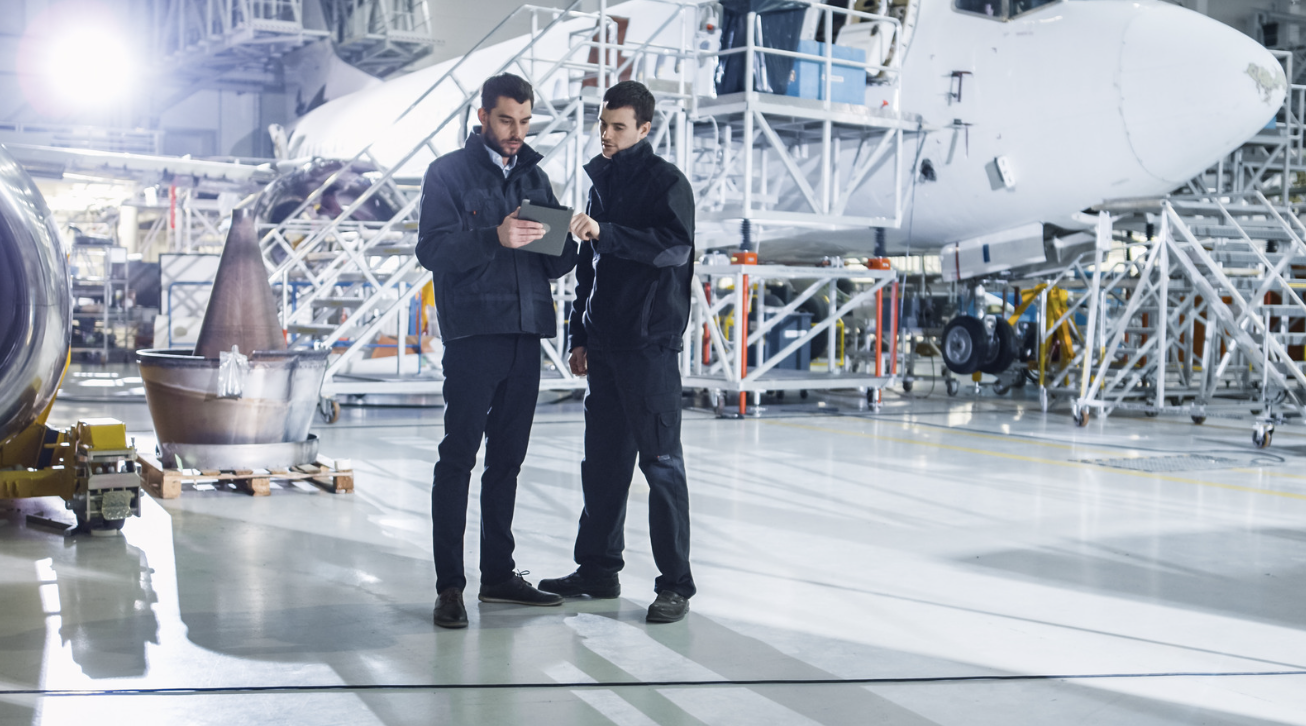
Case Study
Developing Smart Tools for the Airbus Factory
Manufacturing and assembly of aircraft, which involves tens of thousands of steps that must be followed by the operators, and a single mistake in the process could cost hundreds of thousands of dollars to fix, makes the room for error very small.
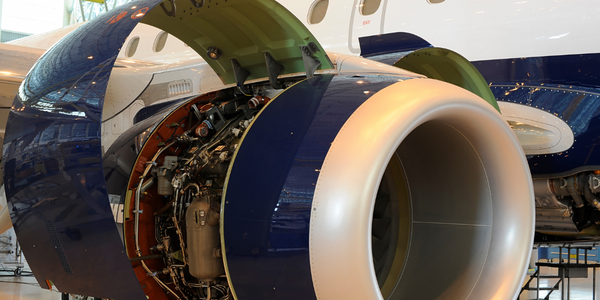
Case Study
Accelerate Production for Spirit AeroSystems
The manufacture and assembly of massive fuselage assemblies and other large structures generates a river of data. In fact, the bill of materials for a single fuselage alone can be millions of rows of data. In-house production processes and testing, as well as other manufacturers and customers created data flows that overwhelmed previous processes and information systems. Spirit’s customer base had grown substantially since their 2005 divestiture from Boeing, resulting in a $41 billion backlog of orders to fill. To address this backlog, meet increased customer demands and minimize additional capital investment, the company needed a way to improve throughput in the existing operational footprint. Spirit had a requirement from customers to increase fuselage production by 30%. To accomplish this goal, Spirit needed real-time information on its value chain and workflow. However, the two terabytes of data being pulled from their SAP ECC was unmanageable and overloaded their business warehouse. It had become time-consuming and difficult to pull aggregate data, disaggregate it for the needed information and then reassemble to create a report. During the 6-8 hours it took to build a report, another work shift (they run three per day) would have already taken place, thus the report content was out-of-date before it was ever delivered. As a result, supervisors often had to rely on manual efforts to provide charts, reports and analysis.